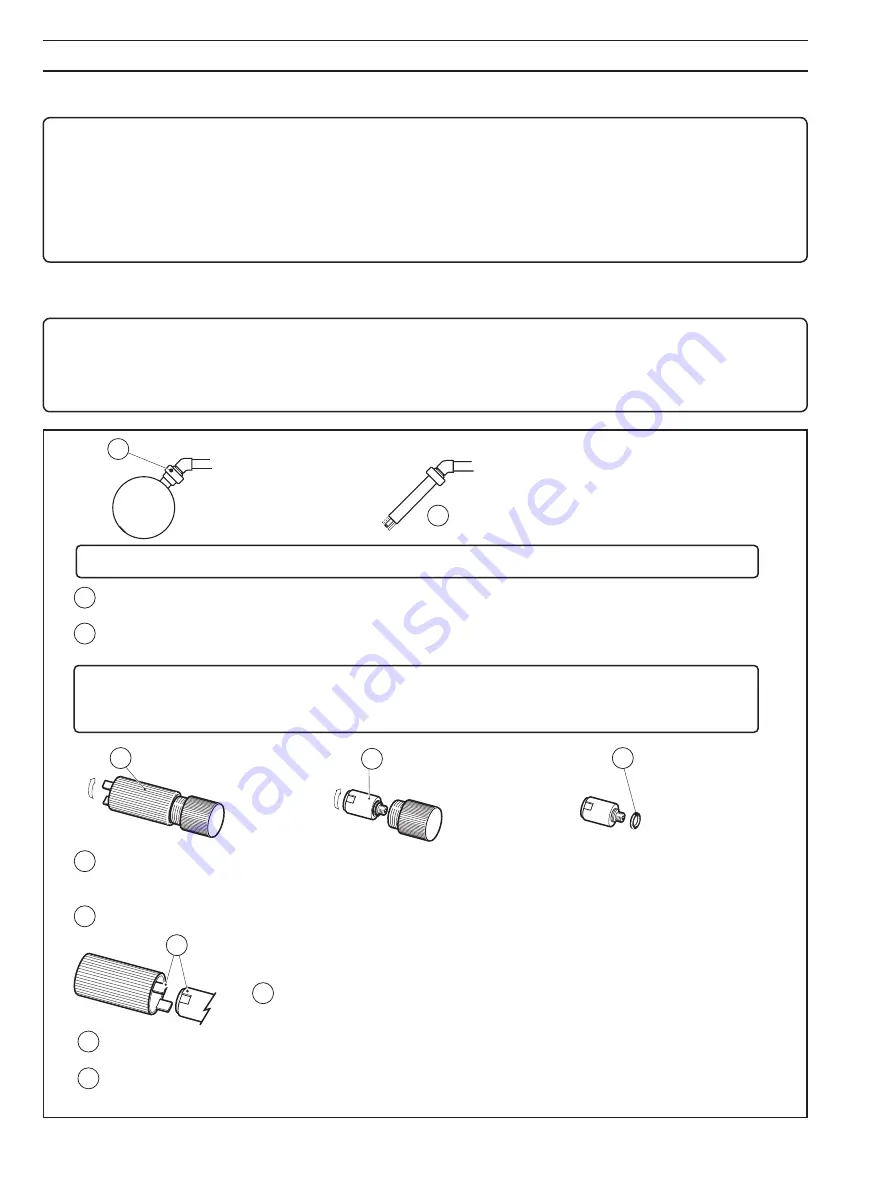
10
Access the new capsule by
unscrewing the capsule housing
Unscrew the capsule from the
shorting cap using the reverse end
of the capsule housing as a tool.
Remove and discard
the rubber sealing
ring from the new
capsule.
Dry the capsule with a paper tissue taking care not to damage the delicate, transparent membrane covering
the silver cathode. Ensure that the gold contacts, and the threaded portion of the capsule are clean and
completely dry.
Fit the new sealing ring supplied – see
7
above and screw the capsule into the sensor block by hand, firmly.
Tighten the securing ring whilst restraining the ball from turning; rotation of the ball may damage the sensing
end of the system.
Caution. Clean and dry the area around the sensor capsule before removal, as indicated below.
Use the capsule housing as a tool to unscrew the old capsule from the sensor block (see
0
for method);
discard the old capsule in accordance with local regulations.
Dry the sensor block with a paper tissue; ensure that the gold electrical contacts, and the recess into
which the capsule screws, are clean and completely dry.
Unscrew the securing ring whilst restraining the ball from turning.
Remove the ball from the sensor pipe.
Reverse the capsule housing and locate the lugs into the keyways on top of the capsule.Then
using the capsule housing as a tool, tighten the the sensor firmly by hand to ensure a good
seal.
Calibrate the sensor - see Section 4.2 Calibrating the Sensor.
Caution.
• Do not leave the new capsule exposed to air for more than 30 minutes as the membrane will dry out.
• Ensure the following steps are done carefully to avoid damaging the membrane covering the silver cathode.
Align the holes in the end of the ball with the protruding sensor capsule and temperature compensator and
replace the ball assembly over the sensor pipe. Ensure that an 'O' ring is in place in the union half.
1
3
2
4
5
6
7
8
9
10
11
12
13
5.1 Replacing the Oxygen Sensor Capsule
5.1.1 Floating Ball System – Fig. 5.1
Refer to Fig. 3.2 for information about accessing the floating ball. Use the necessary procedure steps in reverse order.
Notes.
• For systems fitted with the standard bracket the boom will have to be freed from the bracket clamp to access the floating
ball.
• For systems fitted with a swivel bracket, when the boom is in the horizontal position, unscrew the swivel plate locking
bolt sufficiently to release the swivel plate. Swing the boom so that the floating ball is accessible.
Fig. 5.1 Replacing the Oxygen Sensor Capsule
5 MAINTENANCE
Storage
DO:
— use sensors in date rotation to prevent them being
stored longer than necessary.
— at all times, store sensors in a dry and cool environment.
— store sensors in a refrigerator to extend their life, but
DO NOT allow them to freeze.
DO NOT:
— allow sensors to dry out, either in storage or in use.
— leave sensors in vehicles where they are likely to freeze or be
exposed to high temperatures.
— leave sensors on-site without protection from direct sun or
high temperatures.
— use the sensor if it's sealed environment has dried out.