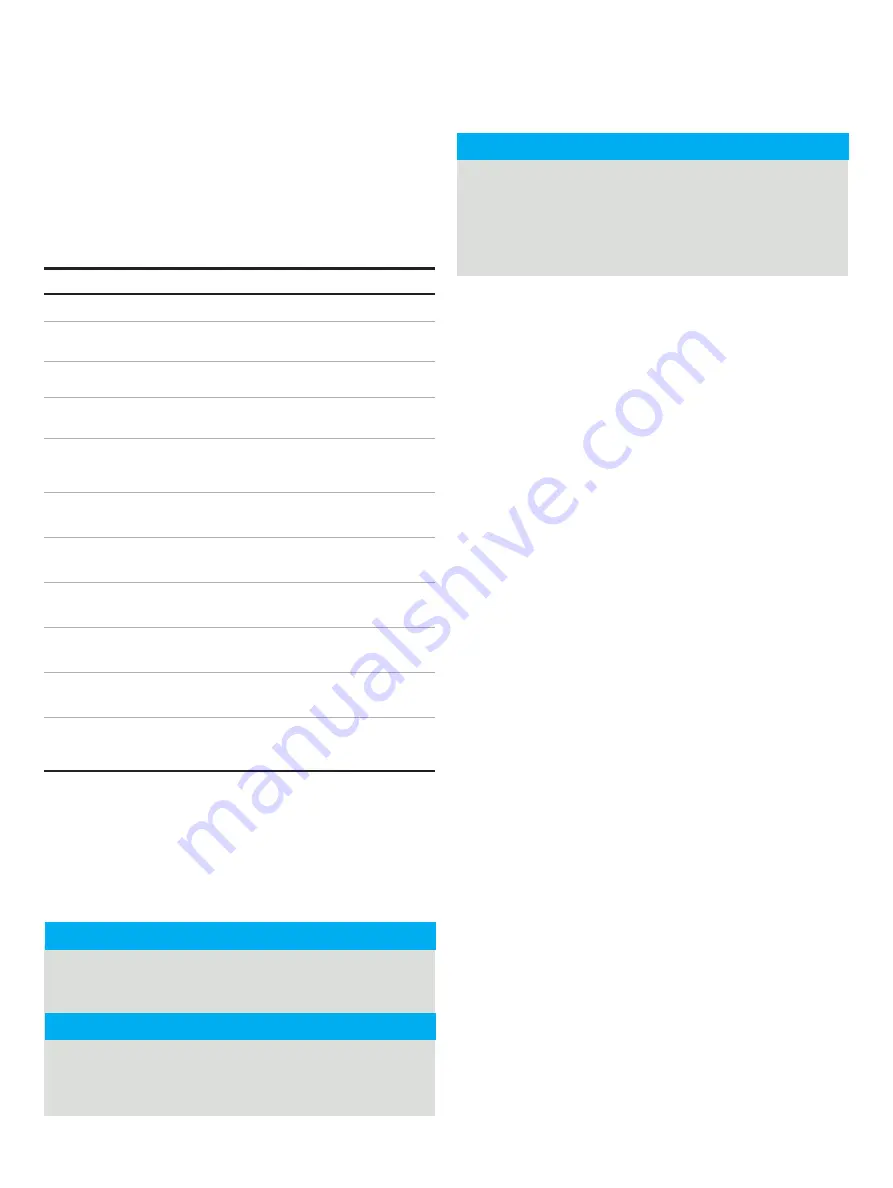
2 6 6 DDS H A RT |
P R E SSU R E T R A N SM I T T ER S | O I/ 2 6 6 D DS - EN R E V. B
25
HMI as feedback of the local push button
operations
As described, when the Z or S buttons are released, the
feedback of the executed operation is displayed in the bottom
of the LCD (same position as per diagnostic messages):
Message
Description
! Oper Done
The push button operation has been successfully executed
! Proc Too
Low
The Pressure measured in input is too low and not acceptable
for the requested operation
! Proc Too
High
The Pressure measured in input is too high and not acceptable
for the requested operation
! New URV
Error
The Zero (Z) operation cannot be accepted because the URV
would be shifted outside the Upper Sensor limit
! Span Error
The Span (S) operation cannot be accepted because the new
URV would be too close to the LRV and their difference lower
than the Minimum Span value
! Oper
Disabled
The push button operation has been refused because the Write
Protection is enabled
! LRV Too
Low
New LRV is too low and not acceptable for the requested
operation
! LRV Too
High
New LRV is too high low and not acceptable for the requested
operation
URV Too
Low
New URV is too low and not acceptable for the requested
operation
URV Too
High
New URV is too high and not acceptable for the requested
operation
Armed
Device is armed to accept HART command 73 “Find Device”.
This message can be triggered only during the device wakeup
operation
Correction of zero shift caused by
installation with PV Zero Bias / Offset
• Raise the dip switch 3 in 1 (up) position.
• Press the “Z” button. This sets the output current to 4 mA, the
digital PV value will be set to 0 (zero).
• To reset the PV zero bias setting, press the “S” button.
When the transmitter has been rezeroed following the above
procedure, a zero bias/offset value is applied and stored in
the transmitter memory.
This action can be performed both by using the external, non-
intrusive push buttons and the on-board buttons of the
integrated LCD display, which become respectively
associated to B and R letters in the lower corners.
After releasing Z and S buttons (on LCD or external) during
range values configuration or PV to zero bias/Reset PV bias
setting, the transmitter displays a message to confirm or abort
the operation, showing Yes and No in the bottom corners of the
display. Proceed accordingly by acting on the corresponding
button: Z for NO and S for YES.
Hardware settings
There are 6 dip switches located on this kind of secondary
electronics.
• Switch 1 and 2 allow the REPLACE MODE for sensor or
secondary electronics.
• Switch 3 identifies the external push buttons functionalities:
Zero/Span adjustments or PV Bias-Offset / PV Bias Reset.
• Switch 4 and 5 are for Fail Low/Fail High selection.
• Switch 6: not used.
The electronic label explains how to perform all the possible
selection. All operations with the dip switches should be
carried out when the transmitter is powered off so as to upload
new configurations at instrument start-up.
Replace mode (switches 1 and 2)
Usually switches 1 and 2 are down in “0” position. They are
moved when a replace operation is required.
Switch 1 up in “1” position is required before power up the
transmitter, when user needs to replace the electronics or the
sensor.
Switch 2 down in “0” position allows the replace of the
secondary electronics. It must be moved in this position before
power up the transmitter.
Switch 2 up in “1” position indicates that a new sensor has been
installed.
AFTER ANY REPLACE OPERATION MOVE DOWN IN “0” POSITION
THE RELEVANT SWITCHES
Push buttons mode (switch 3)
Dip switch 3 is set at the factory on “0” position. This means
that the external push buttons perform the zero/span
adjustments. If the user puts this switch on “1” position, the
zero push buttons will modify the PV Bias-Offset and the span
push button will reset the PV Bias-Offset value.
Fail mode (switch 4 and 5)
Should the user modify the factory-defined parameters for the
fail safe output condition in case of transmitter failure, it is
necessary to enable the modification by putting dip switch 4 on
“1” position. Consequently, it is necessary to choose whether
the output has to go Upscale or Downscale.
Dip switch 5:
on “0” position the output is driven upscale (High alarm 21mA)
on “1” position the output is driven downscale (Low alarm 3.6 mA)
For exceptions please refer to diagnostics chapter.
IMPORTANT
IMPORTANT
IMPORTANT
Содержание 266 DDS
Страница 30: ...Device Set up 30 266 DDS HART PRESSURE TR ANSMITTERS OI 266DDS EN REV B ...
Страница 31: ...266 DDS HART PRESSURE TR ANSMITTERS OI 266DDS EN REV B 31 ...
Страница 32: ...32 266 DDS HART PRESSURE TR ANSMITTERS OI 266DDS EN REV B ...
Страница 33: ...266 DDS HART PRESSURE TR ANSMITTERS OI 266DDS EN REV B 33 ...
Страница 34: ...Display 34 266 DDS HART PRESSURE TR ANSMITTERS OI 266DDS EN REV B ...
Страница 35: ...266 DDS HART PRESSURE TR ANSMITTERS OI 266DDS EN REV B 35 ...
Страница 36: ...36 266 DDS HART PRESSURE TR ANSMITTERS OI 266DDS EN REV B ...
Страница 41: ...Device Info 266 DDS HART PRESSURE TR ANSMITTERS OI 266DDS EN REV B 41 ...
Страница 42: ...Communication 42 266 DDS HART PRESSURE TR ANSMITTERS OI 266DDS EN REV B ...
Страница 59: ...266 DDS HART PRESSURE TR ANSMITTERS OI 266DDS EN REV B 59 Notes ...