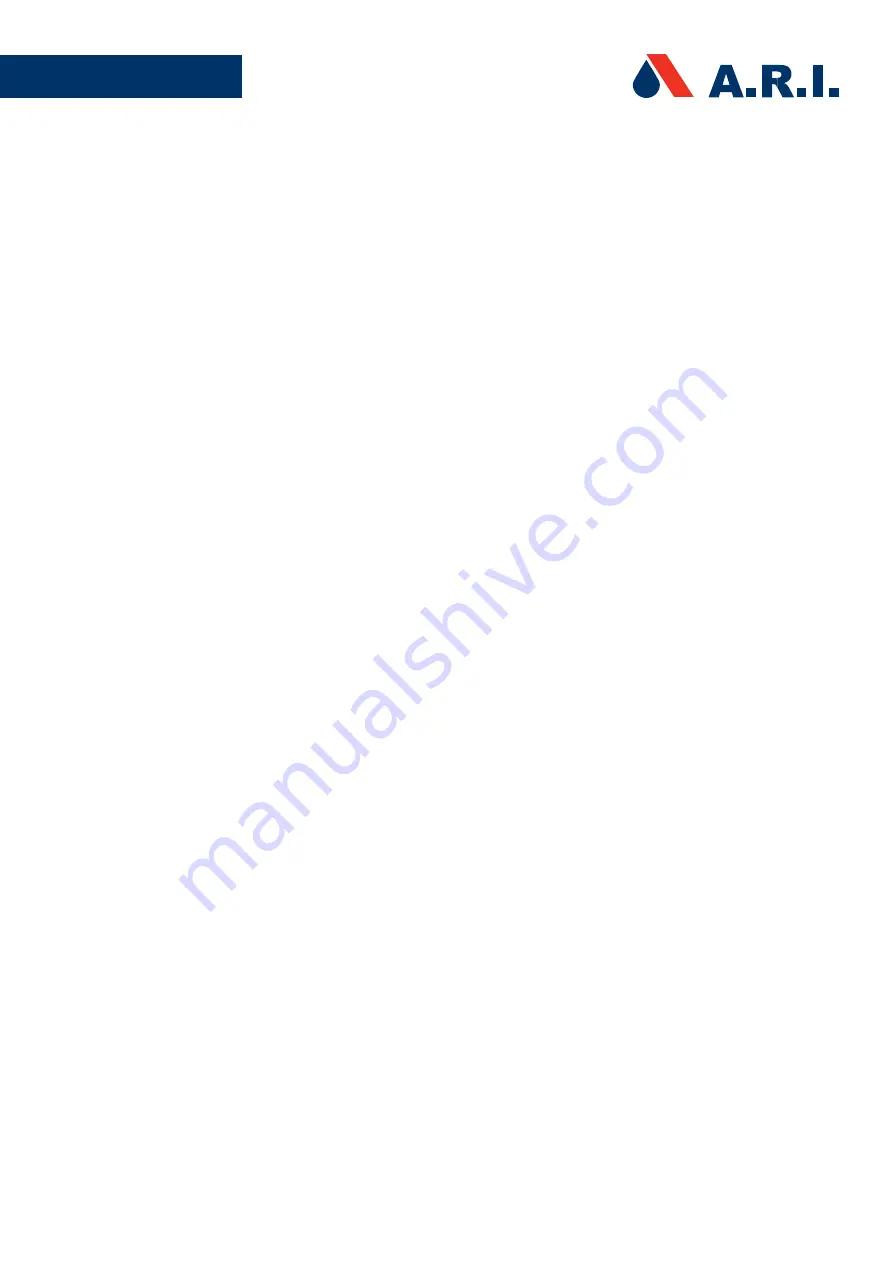
5
IOM D-070-P
Before returning to regular operation
1.
Re-assemble any protection covers or protection mechanisms removed during service or maintenance
operations.
2.
Make sure that all the tools, ladders, lifting devices, etc. used during the maintenance procedures are taken
away from the product area and stored.
3.
Remove grease and fat material residues in order to avoid slipping.
4.
In order to return the product to regular operation, follow the First Start-up Operation instructions as detailed in
your user manual.