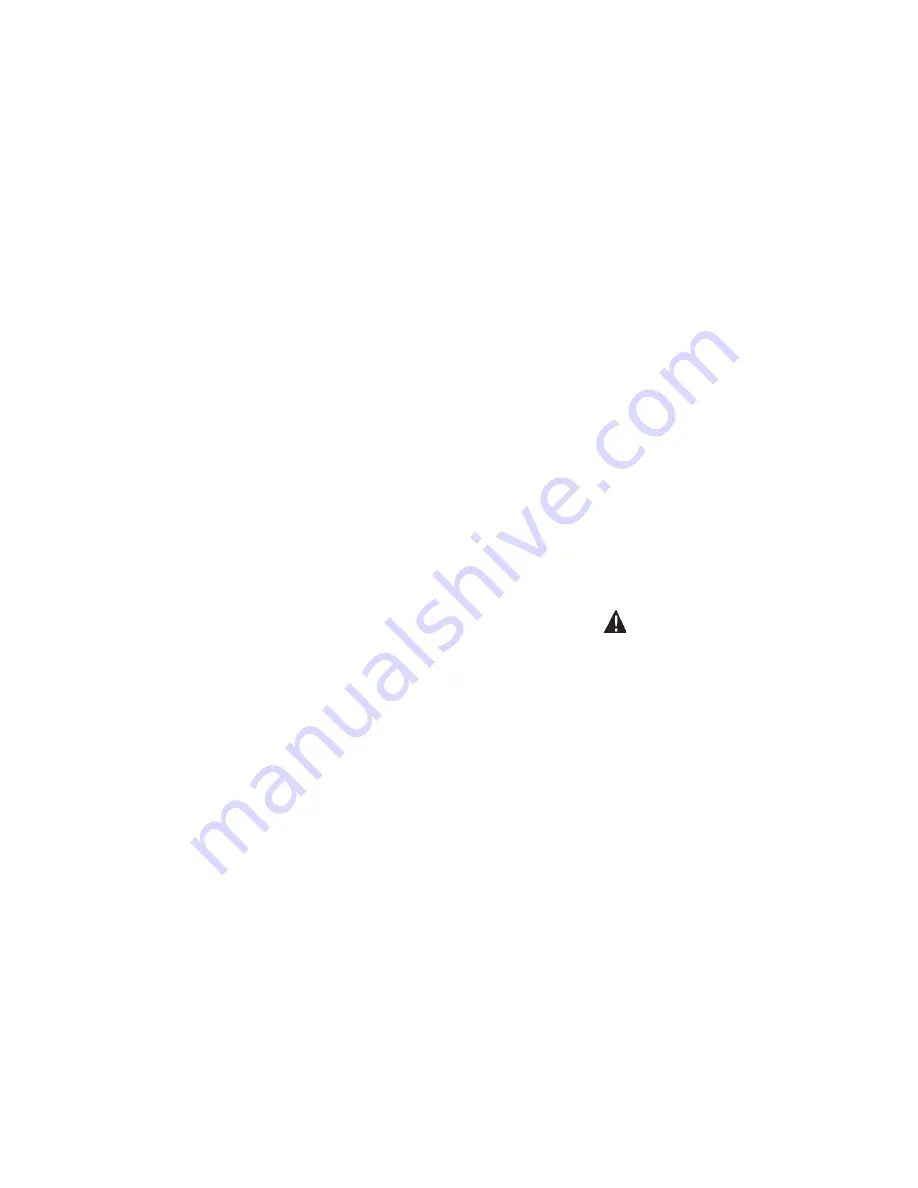
30
MOTOR WILL NOT RUN
1. Confirm 120V AC to the controller. Also, to verify correct polarity, check
for 120 V AC between hot supply and ground.
If there is no voltage, check for a loose connection where it connects to
the controller.
2. If there is 120 volts to the controller, check for loose connections or a
locked rotor. If the rotor cannot be freed the motor and blower assembly
must be replaced.
MOTOR RUNS, PREPURGE TIME ELAPSES BUT MAIN
FLAME NOT ESTABLISHED.
1. Check to see if main manual gas valve is open.
2. Check for a loose connection at the transformer, or a defective
transformer.
3. Check for a loose connection at the gas valve.
4. Check for open pressure switches or open reset button. Check for
blockage in the intake and exhaust venting or at the vent hoods. If no
blockage is found, check vinyl tubing for cuts or crimps. If this tubing is
damaged it must be replaced. If these steps do not eliminate the problem,
replace the pressure switches.
5. Check to see if there is resistance across the igniter terminal with an
OHM meter. If there is no continuity, the igniter is broken and should be
replaced.
If the igniter appears to function properly, then verify that the inlet
pressure is 12" Natural Gas (3 kPa) and 14.0" L.P. Gas (3.45 kPa) W.C.
maximum. The gas valve supplied on this appliance is not designed to
open against a higher pressure. At this time also check that the inlet
pressure is not lower than the minimal gas supply pressure, as shown
in Table 4: that is, for Natural Gas, 5.0" (1.25 kPa) W.C. for BTH 120 &
250 or 4.5" (1.1 kPa) W.C. for BTH 150 & 199 or; for L.P. Gas, 11.0"
(2.74 kPa) W.C. if the inlet pressure is not within these limits then adjust
the supply pressure accordingly.
If the inlet pressure falls within the allowable limits, then verify that the
manifold pressure, when the gas is fully open, with the heater running,
is as called out in Table 4: that is, for Natural Gas, 4.0" (1 kPa) W.C. for
BTH 120 & 250 or 3.5" (.9 kPa) W.C. for BTH 150 & 199 or; for L.P. Gas,
10.0" (2.5 kPa) W.C. If the manifold pressure is not correct then adjust
accordingly. See ADJUSTMENT PROCEDURE in OPERATING
INSTRUCTIONS selection, page 18, for the manifold pressure adjustment
procedure.
6. If the inlet and manifold pressures are within the limits specified in step
5, then reset the appliance. Verify 24V AC at the gas valve during the
three (3) second ignition trial, after the igniter reaches operating
temperature. If 24V AC at the gas valve is not seen during this period,
the controller must be replaced.
If there is 24V AC at the gas valve during the four second ignition trial
and the manifold pressure does not increase above 0" W.C. then verify
that the manual gas control valve is in the “ON” position (see page 20).
If the valve is in the “ON” position and the previous voltage and gas
pressure conditions are met, then the gas valve is defective and must
be replaced.
Note that a positive manifold pressure reading of approximately
1.5" (.38 kPa) W.C. is normal during the prepurge portion of the ignition
cycle due to the location of the gas orifice.
MOTOR RUNS, BURNER LIGHTS MOMENTARILY,
THEN LOCKS OUT
1. Reset the appliance two more times to ensure that all of the air has been
purged from the gas line.
2. If the burner lights momentarily but does not sustain ignition, verify that
the inlet pressure is not greater than 14.0" (3.5 kPa) W.C. or lower than
the minimal gas supply pressure, as shown in Table 4: that is, for
Natural Gas, 5.0" (1.25 kPa) W.C. for BTH 120 & 250 or 4.5" (1.1 kPa)
W.C. for BTH 150 & 199 or; for L.P. Gas, 11.0" (2.74 kPa) W.C. pressure.
Also, the manifold pressure should rise during the three (3) second trial
for ignition to the manifold pressure value for the individual unit listed in
Table 4: that is, for Natural Gas, 4.0" (1 kPa) W.C. for BTH 120 & 250 or
3.5" (.9 kPa) W.C. for BTH 150 & 199 or; for L.P. Gas, 10.0" (2.5 kPa)
W.C. If the manifold pressure is not correct then adjust accordingly. See
ADJUSTMENT PROCEDURE in OPERATING INSTRUCTIONS section, page
18, for the manifold pressure adjustment procedure.
3. Check for the reversed polarity in the supply wiring. This controller is
polarity sensitive. If the hot and neutral supply wires are reversed, the
controller will not sense flame. Reverse the supply wires and try to fire
the unit.
NOTE:
Always turn off and disconnect main supply wiring before servicing
the unit.
4. Check connecting wire to the flame sensor. Verify that the flame sensor
has not been damaged in any way.
5. Verify that the air supply is adequate. The air inlet screen or blower
wheel may be restricted. Also, check the installation for proper ventilation.
See AIR REQUIREMENTS.
6. Check the venting system for the correct sizing, excess or insufficient.
See VENTING.
7. Check for a maximum inlet pressure of 12" Natural Gas (3 kPa), 14.0"
L.P. Gas (3.45 kPa) W.C. and the manifold pressure as listed in Table 4:
that is, for Natural Gas, 4.0" (1 kPa) W.C. for BTH 120 & 250 or 3.5" (.9
kPa) W.C. for BTH 150 & 199 or; for L.P. Gas, 10.0" (2.5 kPa) W.C.
Please note that the manifold pressure listed is the maximum value for
the manifold pressure. Do not set the manifold pressure higher than the
value shown for your heater in Table 4. Overfiring the heater will result
in rough ignition and/or noisy operation.
8. Confirm that the air inlet screen (see Figures 7 & 8) is free of obstructions.
CAUTION
Do not reach into the burner housing or combustion chamber if
the heater is still hot. Allow the heater to cool and always use
gloves as the combustion chamber and the burner sleeve and
housing can become very hot after operation. Overfiring is a
dangerous condition that must be corrected immediately.
NOISY BURNER OPERATION
The exhaust of this unit produces some noise. This noise may be
objectionable if the exhaust terminal is located too close to the opening of
an occupied space. The noise may also be objectionable if the exhaust is
located in the confined space between two buildings such as an alley or
walkway. Since everyone's perception and tolerance for background noise
varies, there is no standard recommendation. The best option when the
noise is a concern is to locate the exhaust as far away from any occupied
spaces as practical.
If noise becomes more than one can tolerate, a dampening muffler is available
through our Product Service Division. See “REPLACEMENT PARTS” segment
below.
GAS FAILS TO SHUT OFF
Check for defective gas valve or thermostat. If operation is incorrect,
replace.
REPLACEMENT PARTS
Replacement parts may be ordered through A.O. Smith dealers, authorized
servicers or distributors. Refer to the Yellow Pages for where to call or
contact the A.O. Smith Water Products Company, 5621 W. 115th Street,
Alsip, IL 60803, 1-800-433-2545. When ordering parts be sure to state the
quantity, part number and description of the items including the complete
model and serial number as it appears on the product. Refer to the parts list
for more information.