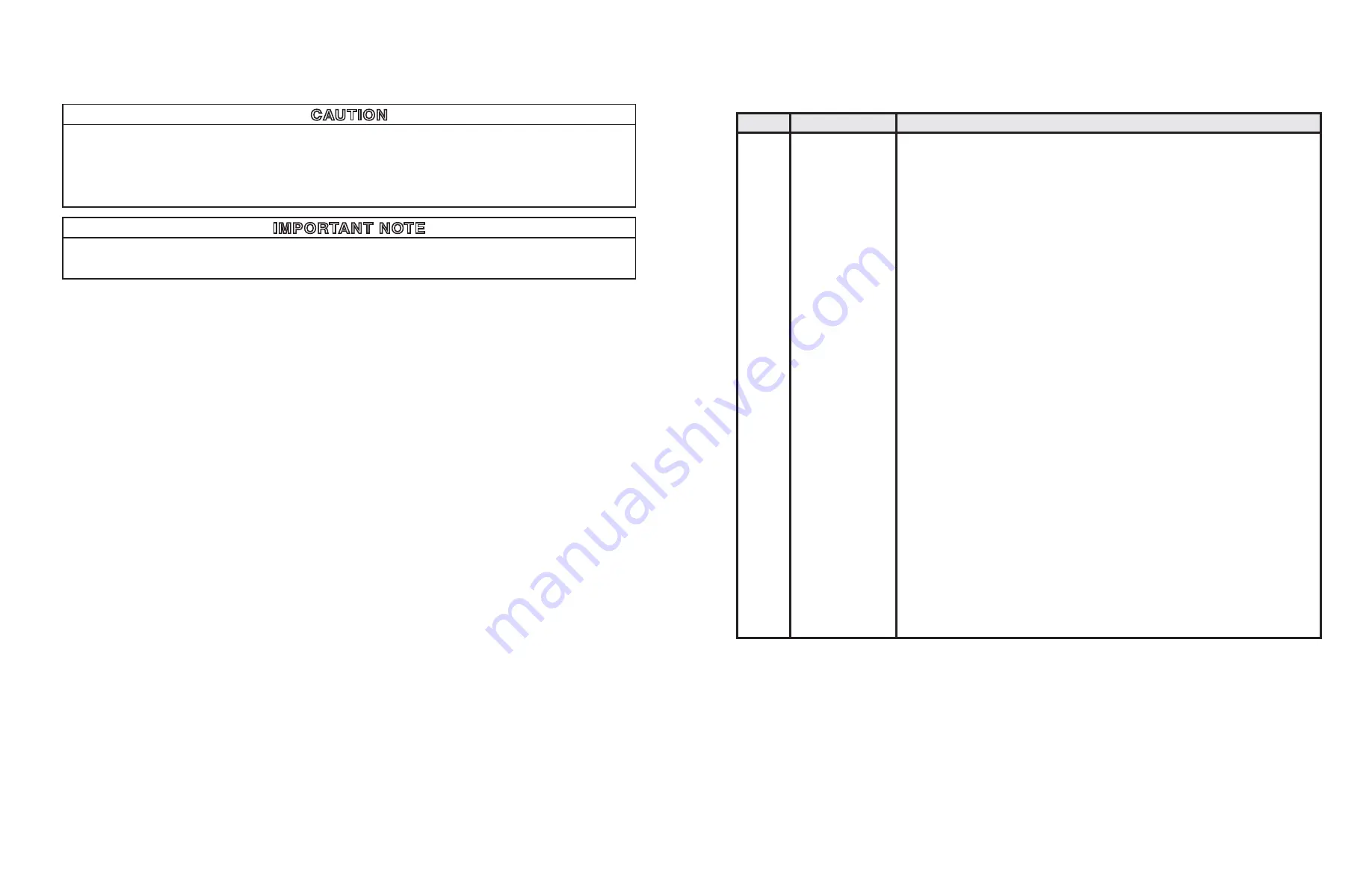
CHECK WATER PRESSURE AND PUMPING RATE:
Two water system conditions must be checked carefully to avoid unsatisfactory operation or equipment damage:
1) MINIMUM water pressure required at the softener tank inlet is 20 psi. IF PRESSURE IS OVER 100 PSI, A PRESSURE REDUC-
ING VALVE MUST BE INSTALLED IN THE WATER SUPPLY LINE AHEAD OF THE WATER SOFTENER.
CAUTION
To reduce the risk associated with property damage due to water leakage:
•
Do not
install if water pressure exceeds 100 psi (689 kPa). If the system water pressure exceeds 100 psi, the installation
must
use a pressure limiting valve. Contact a licensed plumbing professional if you are uncertain how to check your water
pressure.
•
Do not install system where water lines could be subjected to vacuum conditions without appropriate measures for vacuum
prevention.
IMPORTANT NOTE
If the source is a municipal or a community water supply and daytime water pressure is 85 psi or more, nighttime pressure may
exceed 100 psi. Call the local water department or plant operator to obtain pressure readings. If the source is a private well, the
gauge on the pressure tank will indicate the high and low system pressure. Record water pressure data below:
WATER PRESSURE
Low _______ psi High _______ psi
2) If the source of water is a private well, the pumping rate of the well pump must be suffi cient for satisfactory operation and BACK-
WASHING of the WATER SOFTENER. (See SPECIFICATIONS AND OPERATING DATA, Section 5).
LOCATE WATER CONDITIONING EQUIPMENT CORRECTLY:
Select the location of the water softener with care. Various conditions which contribute to proper location are as follows:
1) Locate as close as possible to water supply source.
2) Locate as close as possible to a fl oor or other adequate drain.
3) Locate in correct relationship to other water conditioning equipment (Figure 1).
4) Temperatures above 150° F (66° C) will damage the softener and void the factory warranty.
5) Do NOT install the softener in a location where freezing temperatures occur. Freezing may cause permanent damage and will also
void the factory warranty.
6) Allow suffi cient space around the unit for easy servicing.
7) Provide a non-switched 110V, 60Hz power source for the control. (Reference transformer to verify proper power supply voltage.)
1-2
A
B
C
D
E
F
G
H
1
25
26
28
36
50
49
60
61
62
63
65
66
67
68
69
70
71
72
73
74
79
80
81
82
83
84
85
86
92
DESCRIPTION
PART NO.
REF.
14381X
13010XT
60514-02
60102-031
60125-05
60022-501
10090X
60040
22602
19659
11384
13170
U321
13304
10381-01
13361
13497
12638-01
13301-01
10226-1
10227
10225-1
13303-01
13166
13387
13315
12091
13173
12338
12767
10332
10330
10329
13305
13709
13255
13314
14105
ONLY THOSE PARTS CIRCLED IN DRAWING AND/OR LISTED BELOW ARE STOCK ITEMS
ALL OTHERS ARE SPECIAL ORDER, NON-RETURNABLE
PARTS LIST - 12 DAY TIMER
Skipper Wheel Assy. (Incl. Ref. Items 4-10)
24-Hour Gear Assy. (Incl. Ref. Items 11-16)
Brine Cam Assy. Minutes of Refi ll Salt (Incl. Ref. Items 30 - 34)
Piston Kit (Incl. Ref. Items 41-45)
Seal Kit, HW (Incl. Ref. Items 46 & 47)
Brine Line Flow Control Assy., 0.50 GPM, (Incl. Ref. Items 75-78)
Adapter Coupling Assy. (Incl. 2 ea. Ref. Items 84-86 & 4 ea. Item 83)
3/4" Bypass Valve, 316SS, Hot/Cold
Valve Cover, Specify Model
Motor, 24V/60 Hz
Motor Mtg. & Ground Screw
Main Gear
Transformer, 110V/60Hz - 24V/60Hz
Distributor Tube O-Ring
Tank O-Ring
Stand-off
Air Disperser
Drain O-Ring, HW
Injector O-Ring, HW
Injector Throat - Specify Size
Injector Screen
Injector Nozzle - Specify Size
Injector Cover O-Ring
Injector Cover
Screw, Injector Mounting
Injector Mounting Screw
Drain Line Flow Control Button:
4.0 GPM
Drain Line Flow Control Retainer
Drain Line Fitting
Brine Line Screen
Brine Line Tube Insert
Brine Line Ferrule
Brine Line Fitting Nut
Adapter Coupling O-Ring
Adapter Coupling
Adapter Clip (Incl. 2 ea. Ref. Item 83)
Adapter Coupling Screw
Seal, Bypass
6-4