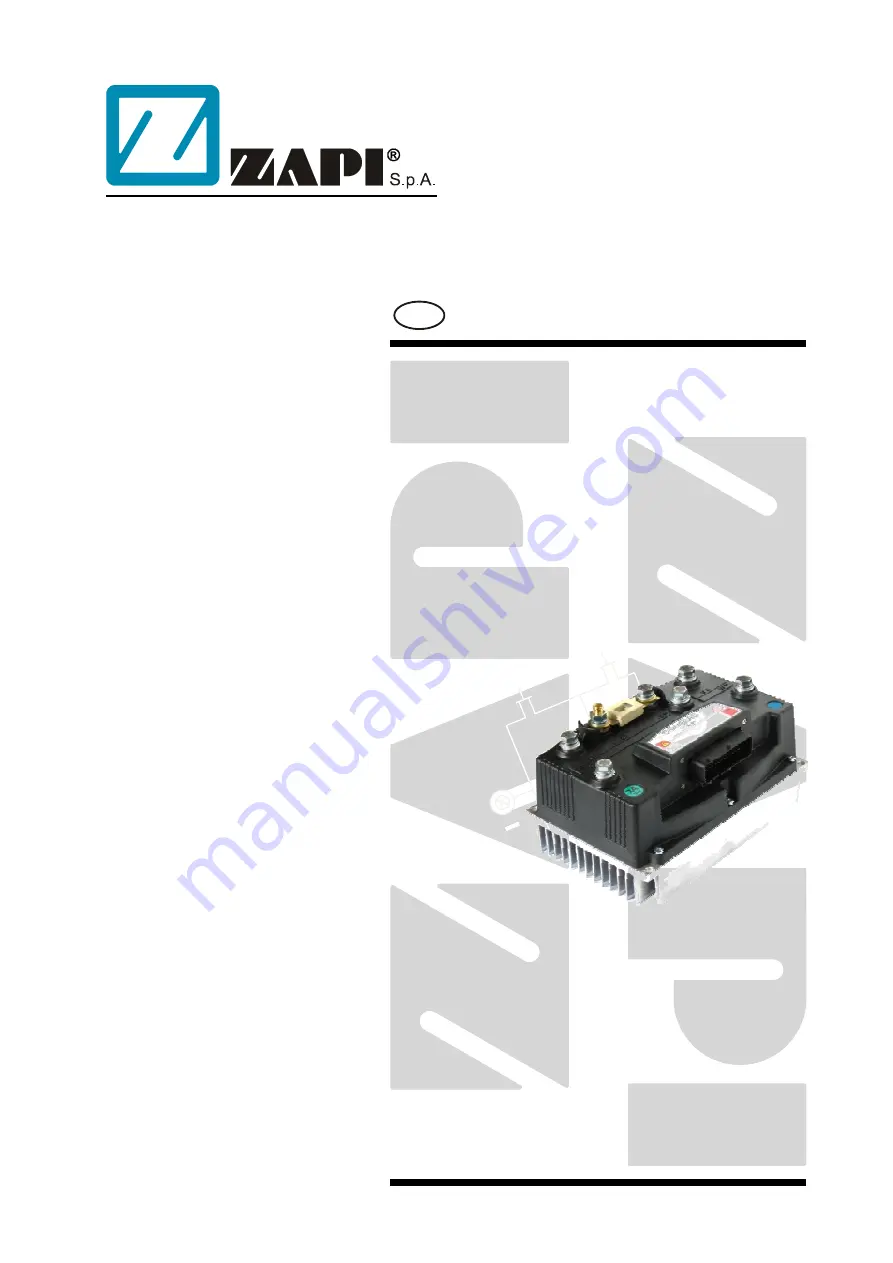
ELECTRONIC • OLEODYNAMIC • INDUSTRIAL
EQUIPMENTS CONSTRUCTION
Via Parma, 59 – 42028 – POVIGLIO (RE) – ITALY
Tel +39 0522 960050 (r.a.) – Fax +39 0522 960259
e-mail: [email protected] – web: www.zapispa.it
EN
User Manual
COMBI AC1
Summary of Contents for COMBI AC1
Page 29: ...7 DRAWINGS 7 1 Mechanical drawing AEQZP0BA COMBI AC1 User Manual Page 29 86...
Page 30: ...7 2 Connection drawing 7 2 1 AmpSaab version Page 30 86 AEQZP0BA COMBI AC1 User Manual...
Page 31: ...7 2 2 AmpSeal version AEQZP0BA COMBI AC1 User Manual Page 31 86...
Page 37: ...9 3 2 Master AmpSeal version AEQZP0BA COMBI AC1 User Manual Page 37 86...
Page 38: ...9 3 3 Slave AmpSaab version Page 38 86 AEQZP0BA COMBI AC1 User Manual...
Page 39: ...9 3 4 Slave AmpSeal version AEQZP0BA COMBI AC1 User Manual Page 39 86...