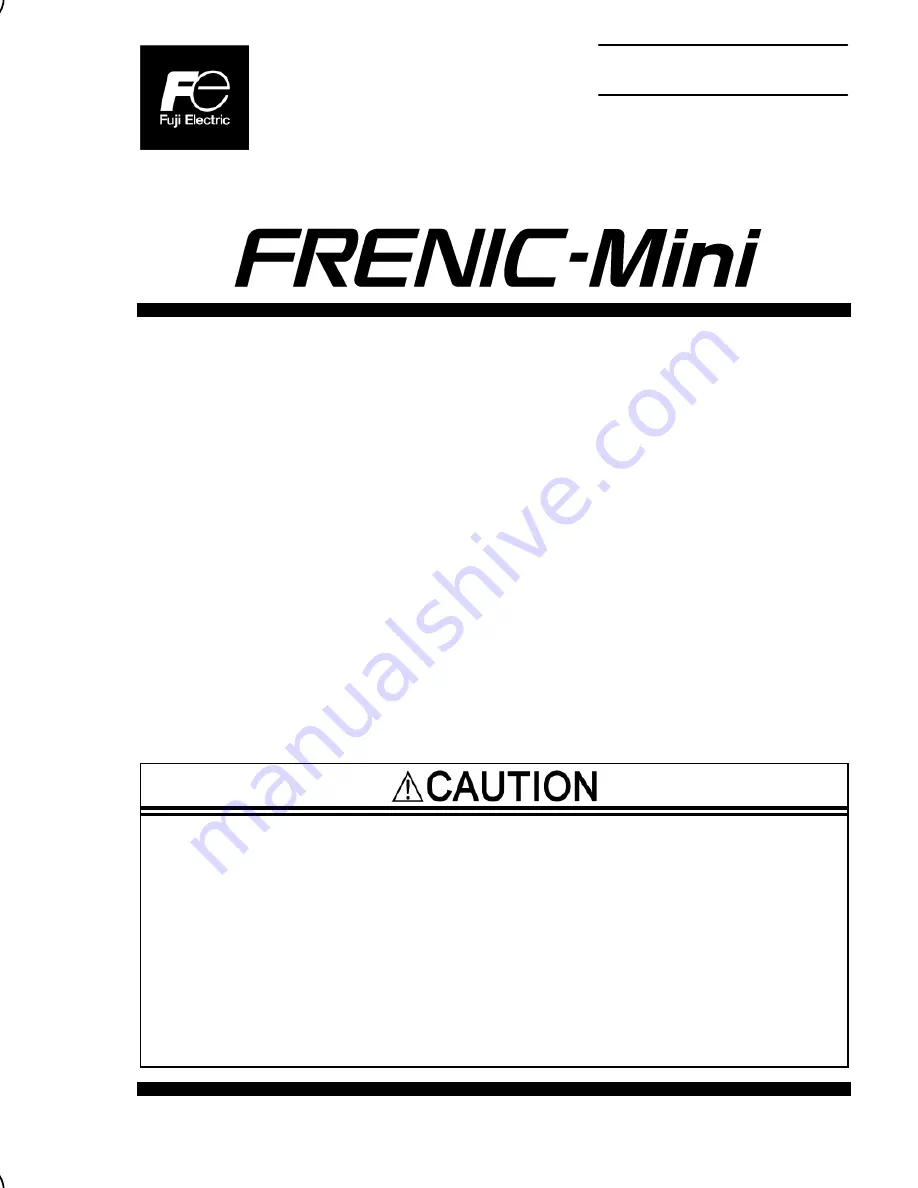
Instruction Manual
Compact Inverter
FRN
C2
-
Thank you for purchasing our FRENIC-Mini series of inverters.
• This product is designed to drive a three-phase induction motor and three-phase permanent
magnet synchronous motor. Read through this instruction manual and be familiar with the
handling procedure for correct use.
• Improper handling might result in incorrect operation, a short life, or even a failure of this
product as well as the motor.
• Deliver this manual to the end user of this product. Keep this manual in a safe place until this
product is discarded.
• For instructions on how to use an optional device, refer to the instruction and installation
manuals for that optional device.
Fuji Electric Co., Ltd.
INR-SI47-1729c-E