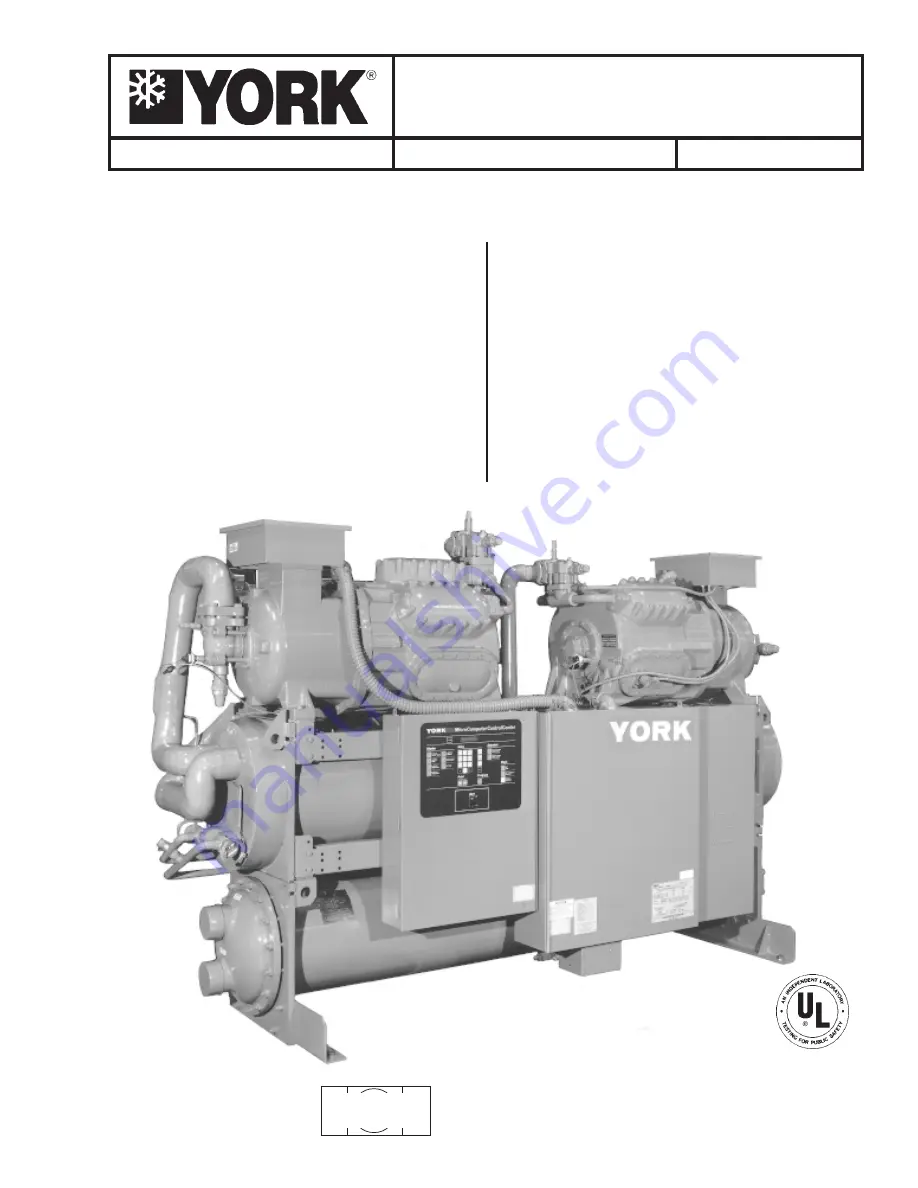
INSTALL., OPER., MAINT.
RecipPak LIQUID CHILLERS
WATER COOLED - RECIPROCATING HERMETIC
Supersedes: 150.24-NM27 (1295)
Form 150.24-NM27 (298)
MODELS
200, 230, 460-3-60
60 HZ
YCWJ45EE0, YCRJ45E00,
YCWJ55HE0, YCRJ55H00,
YCWJ56HF0, YCRJ56H00,
YCWJ66KH0, YCRJ66K00,
YCWJ67KH0, YCRJ67K00,
YCWJ77KH0, YCRJ77K00,
YCWJ88MH0, YCRJ88M00
YCWJ99MJ0, YCRJ99M00
STYLE A*
50 HZ
YCWJ56EE0, YCRJ56E00,
YCWJ66HE0, YCRJ66H00,
YCWJ67HF0, YCRJ67H00,
YCWJ77KH0, YCRJ77K00,
YCWJ78KH0, YCRJ78K00,
YCWJ88KH0, YCRJ88K00,
YCWJ99MH0, YCRJ99M00
STYLE A*
26214A
*With EPROM
(Standard, Brine & Metric Models, Combined)
031-01652-001
or
031-01096-001
Summary of Contents for YCWJ45EE0
Page 29: ...FORM 150 24 NM27 YORK INTERNATIONAL 29 CONTROL CIRCUIT With I O Expansion Board LD02106...
Page 30: ...30 YORK INTERNATIONAL FIG 9 SYSTEM WIRING...
Page 31: ...FORM 150 24 NM27 YORK INTERNATIONAL 31 LD02678...
Page 35: ...FORM 150 24 NM27 YORK INTERNATIONAL 35 LD02679...
Page 36: ...36 YORK INTERNATIONAL MICROPANEL CONNECTION DIAGRAM With I O Expansion Board LD02107...
Page 37: ...FORM 150 24 NM27 YORK INTERNATIONAL 37 LD02108...