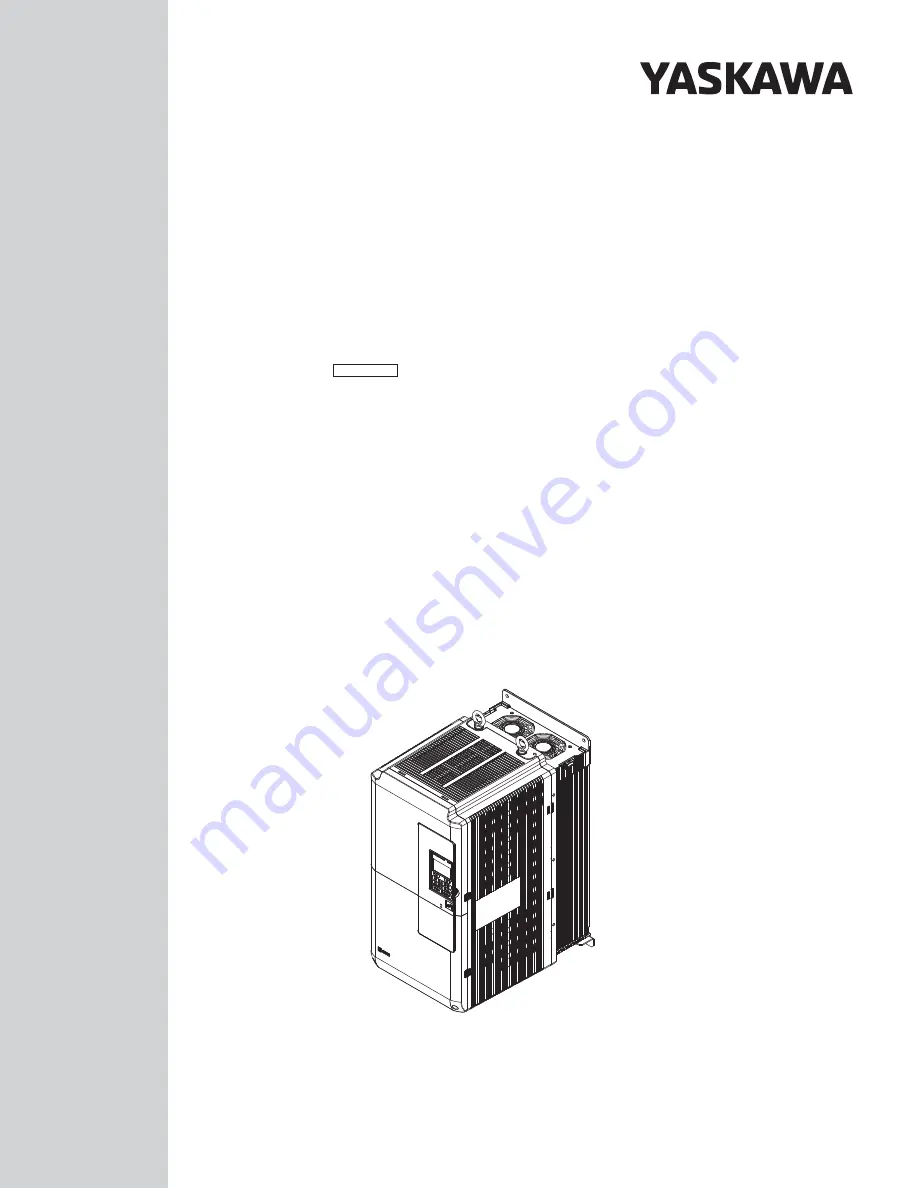
Z1000U HVAC MATRIX Drive
Low Harmonic Drive for HVAC Applications
Quick Start Guide
MANUAL NO. TOEP C710636 11
E
Models: 200 V Class: 7.5 to 75 kW (10 to 100 HP ND)
400 V Class: 5.5 to 260 kW (7.5 to 350 HP ND)
To properly use the product, read this manual thoroughly and retain
for easy reference, inspection, and maintenance. Ensure the end user
receives this manual.
Type: CIMR-ZU