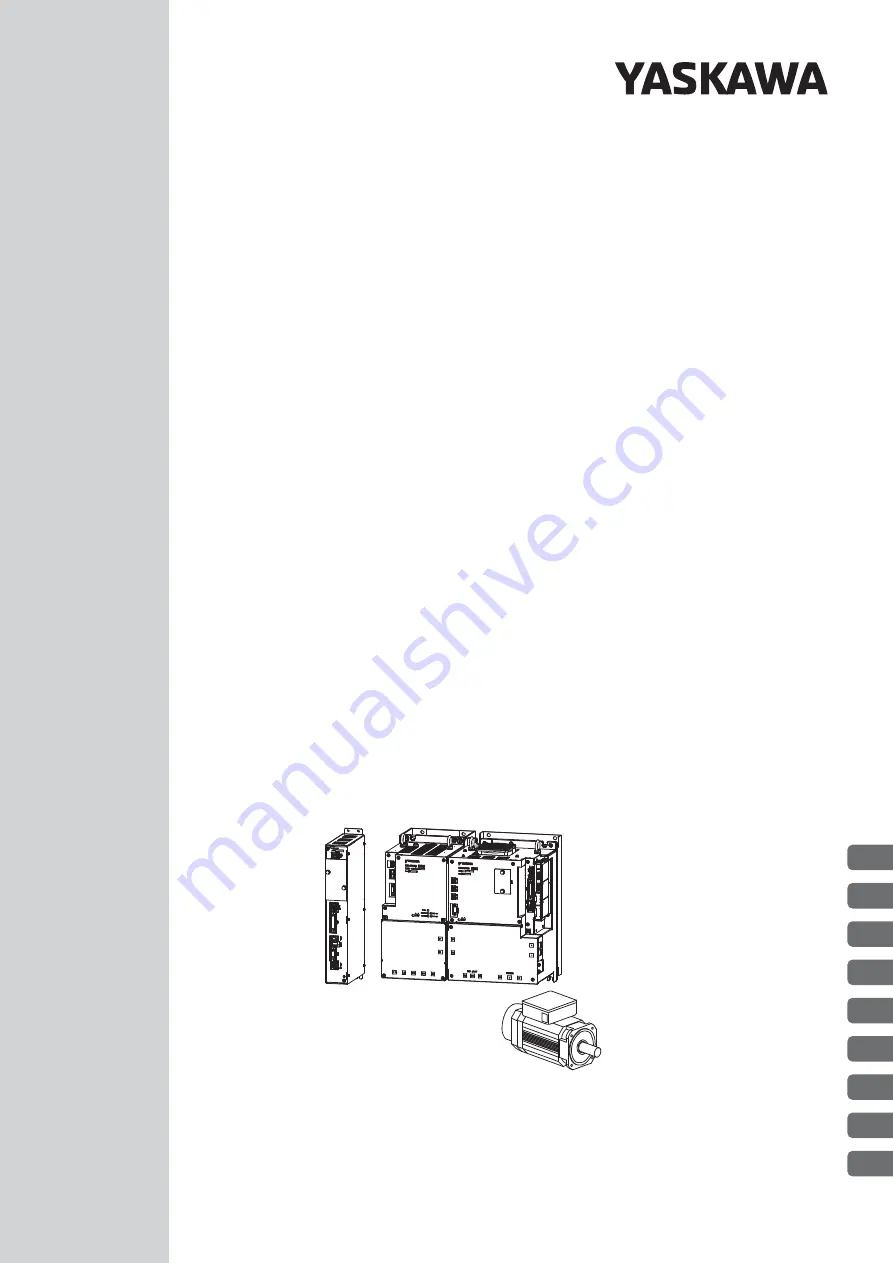
Multi-Winding Drive Unit Model: JUSP-MD
D
A
SERVOPACK Model: SGDV-
J
Converter Model: SGDV-COA
Servomotor Model: SGMVV
Multi-Winding Drive Unit
Rotational Motor
MECHATROLINK-
II
Communications References
-
V
Series
AC Servo Drives
USER’S MANUAL
For Use with Large-Capacity Models
Design and Maintenance
MANUAL NO. SIEP S800001 69D
1
2
3
4
5
6
7
8
9
Outline
Panel Operator
Wiring and Connection
Operation
Adjustments
Utility Functions (Fn
)
Monitor Displays (Un
)
Troubleshooting
Appendix