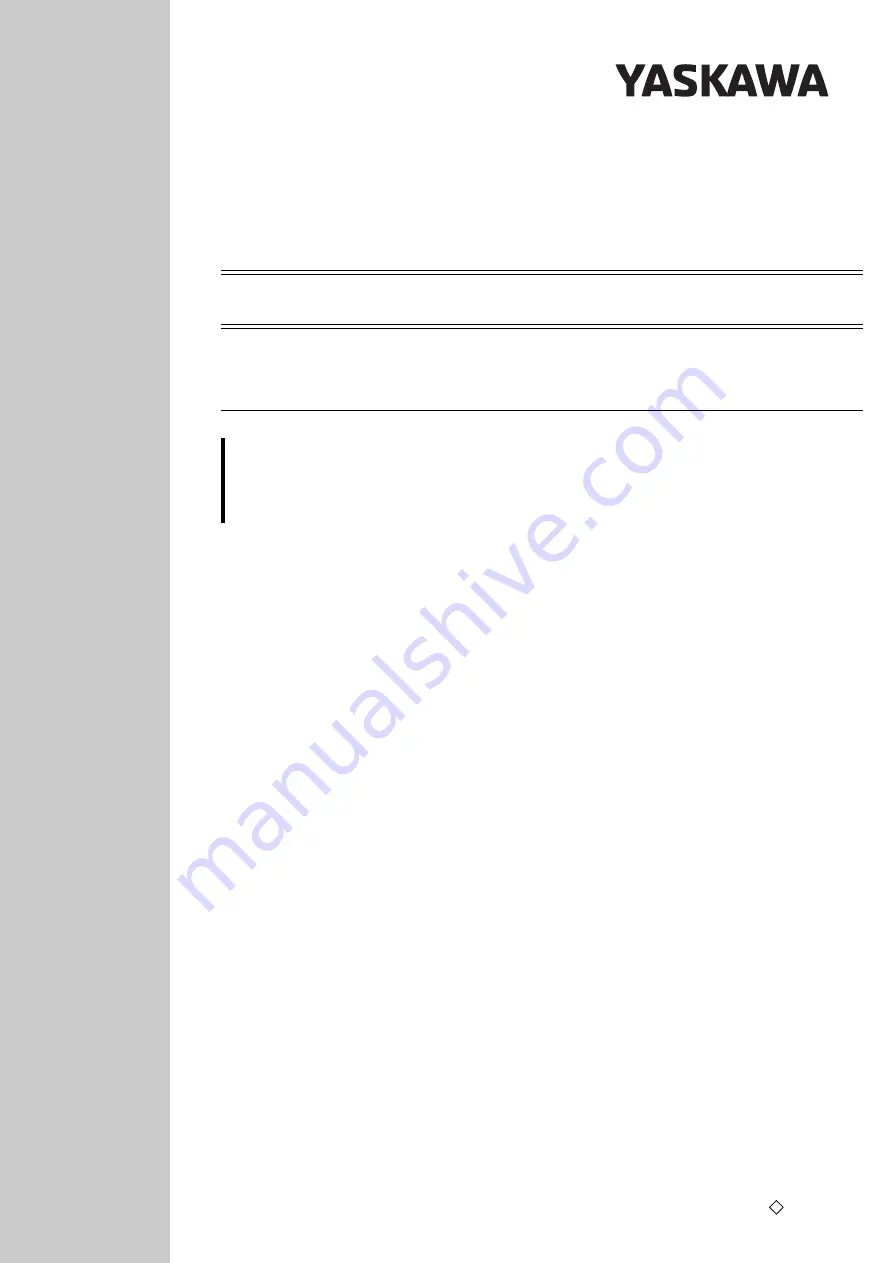
MANUAL NO.
HW1482870
Part Number:
170904-1CD
Revision:
5
6
MOTOMAN-MPL80
II
INSTRUCTIONS
TYPE:
YR-MPL0080-J00 (DX200 STANDARD SPECIFICATION)
Upon receipt of the product and prior to initial operation, read these instructions thoroughly, and
retain for future reference.
MOTOMAN INSTRUCTIONS
MOTOMAN-MPL80
II
INSTRUCTIONS
DX200 INSTRUCTIONS
DX200 OPERATOR’S MANUAL (for each purpose)
DX200 MAINTENANCE MANUAL
1 of 81