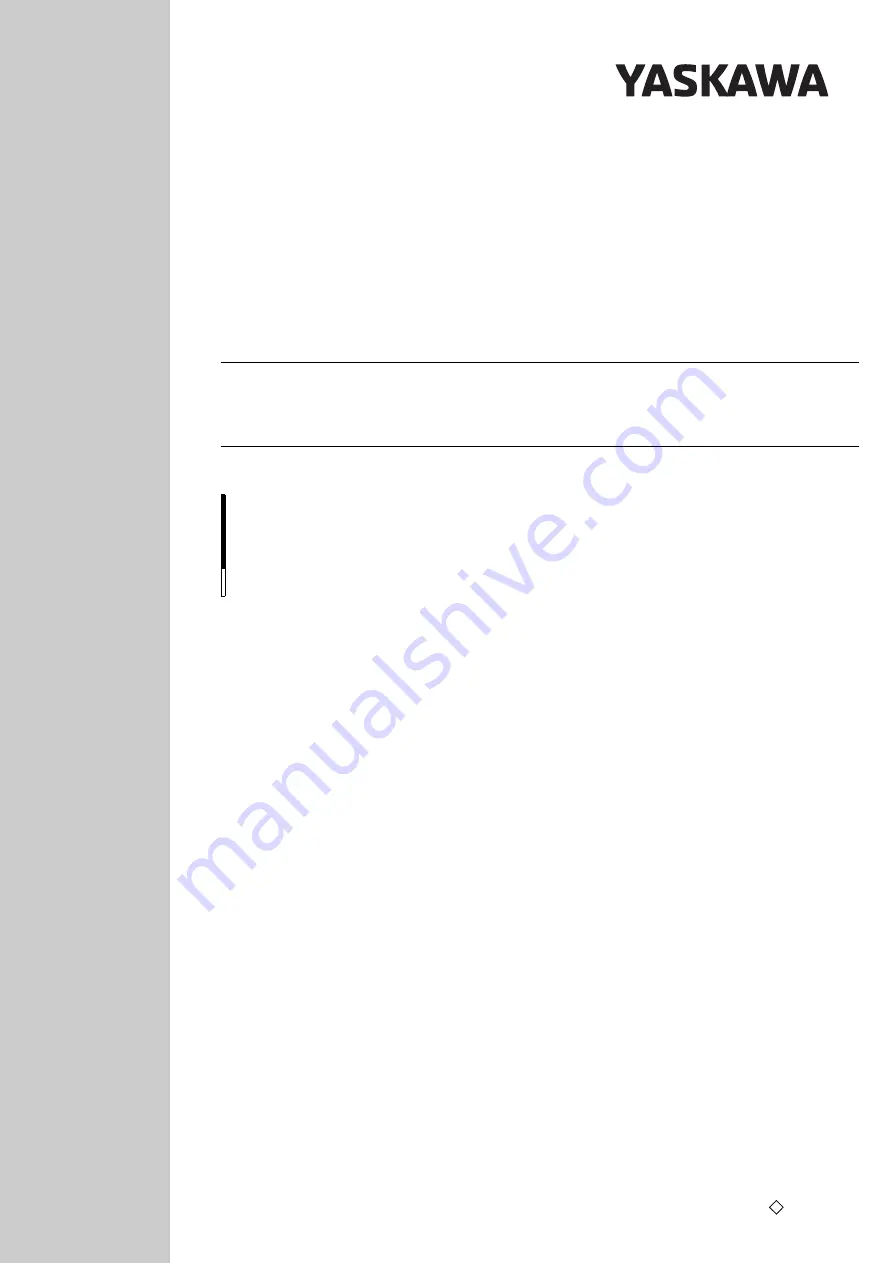
MANUAL NO.
HW1482771
Part Number:
169861-1CD
Revision:
2
3
DX200 OPTIONS
OPERATOR’S MANUAL
FOR WELDCOM FUNCTION:
ARC WELDING/DIGITAL I/F FUNCTION
MOTOMAN INSTRUCTIONS
Upon receipt of the product and prior to initial operation, read these instructions thoroughly, and
retain for future reference.
MOTOMAN-
INSTRUCTIONS
DX200 INSTRUCTIONS
DX200 OPERATOR’S MANUAL (for each purpose)
DX200 MAINTENANCE MANUAL
The DX200 operator’s manuals above correspond to specific usage. Be sure to use the appropriate manual.
1 of 75