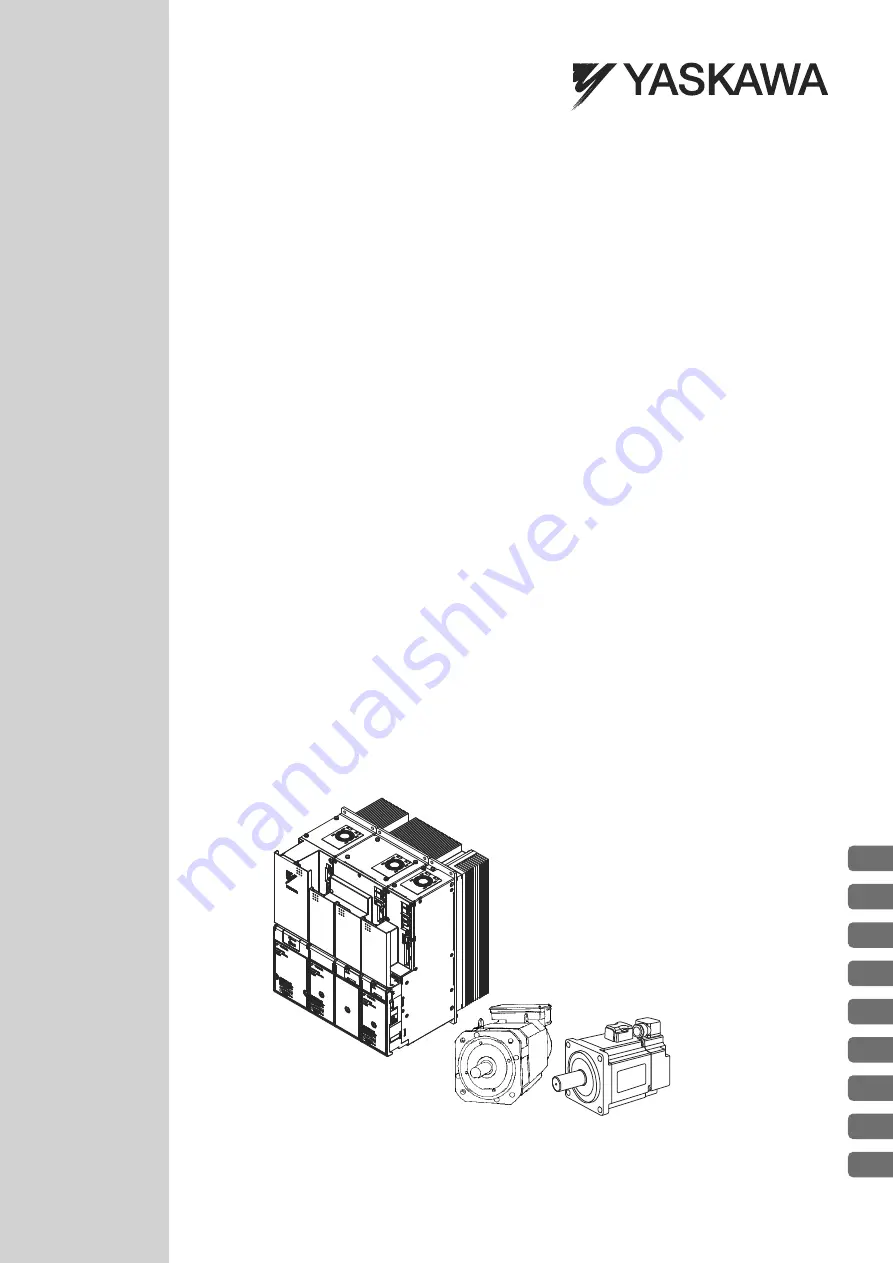
UAK
J-
C
Spindle motor
SGMGV-
8
Servomotor
CACP-JU
3
Power regeneration converter
CACR-JU
2
SERVOPACK
For Application Development in Servo Systems
Σ
-
V
-SD Series
AC Servo Drives
USER'S MANUAL
MANUAL NO. SIEP S800000 87A
1
2
3
4
5
6
7
8
9
Application Overview
MECHATROLINK-
III
Communications
Machine-specific Settings
Feed Axis Operation
Spindle Axis Operation
Additional Functions
Servo Drive Management
Monitoring
Alarm and Warning
Processing