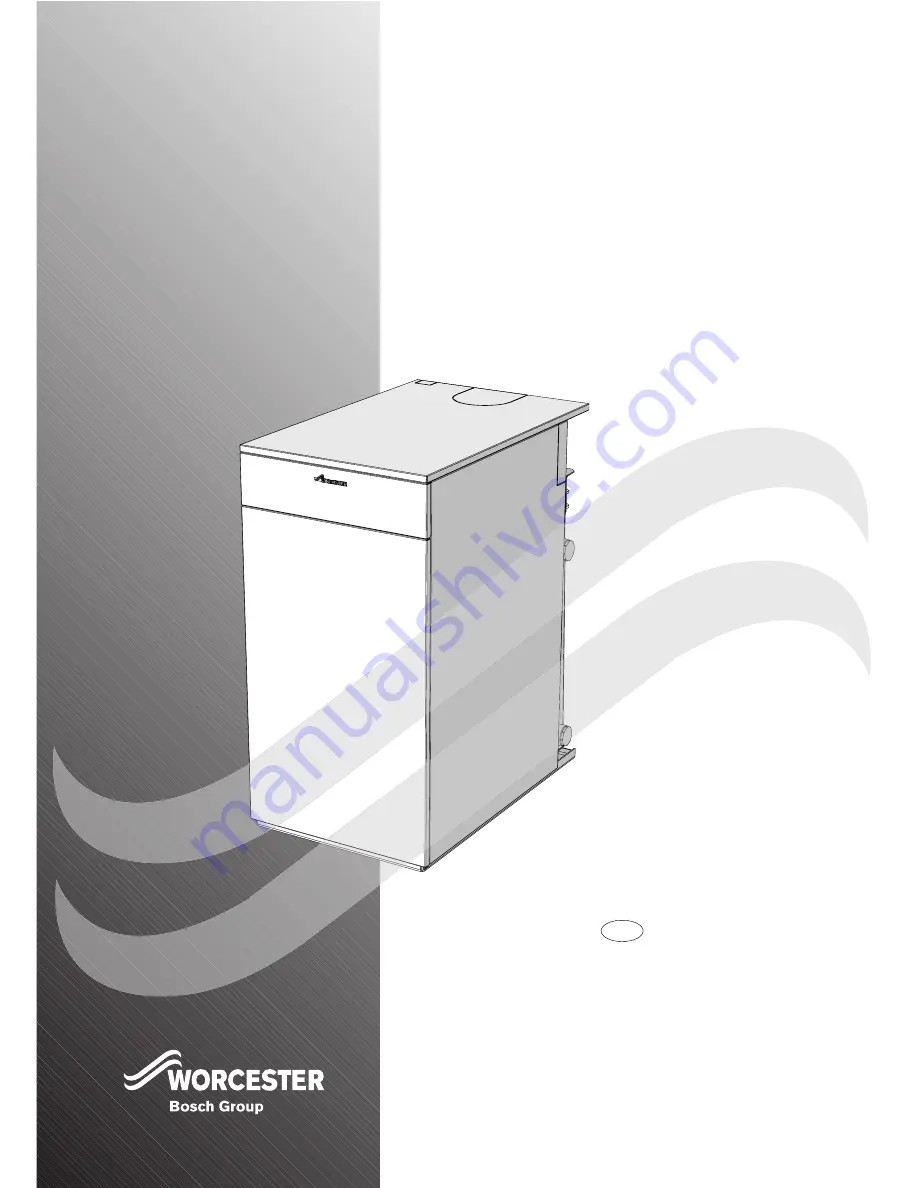
GREENSTAR UTILITY
32/50kW & 50/70kW
FLOOR STANDING OIL-FIRED CONDENSING BOILER
CONVENTIONAL FLUE & ROOM SEALED FLUE
THE APPLIANCE IS FOR USE WITH 28 SECOND KEROSENE
ONLY
GB/IE
8-716-109-711a (04.05)
INSTRUCTION MANUAL
INSTALLATION COMMISSIONING
& SERVICING
GB/IE
FOR FULLY PUMPED OPEN VENT OR SEALED CENTRAL HEATING SYSTEMS AND HOT
WATER CYLINDERS
Patent pending:
Application number 0327645.8
THE APPLIANCE IS FOR USE WITH 28 SECOND KEROSENE
THE APPLIANCE IS FOR USE WITH 28 SECOND KEROSENE
ONLY
GB/IE
INSTRUCTION MANUAL
GB/IE