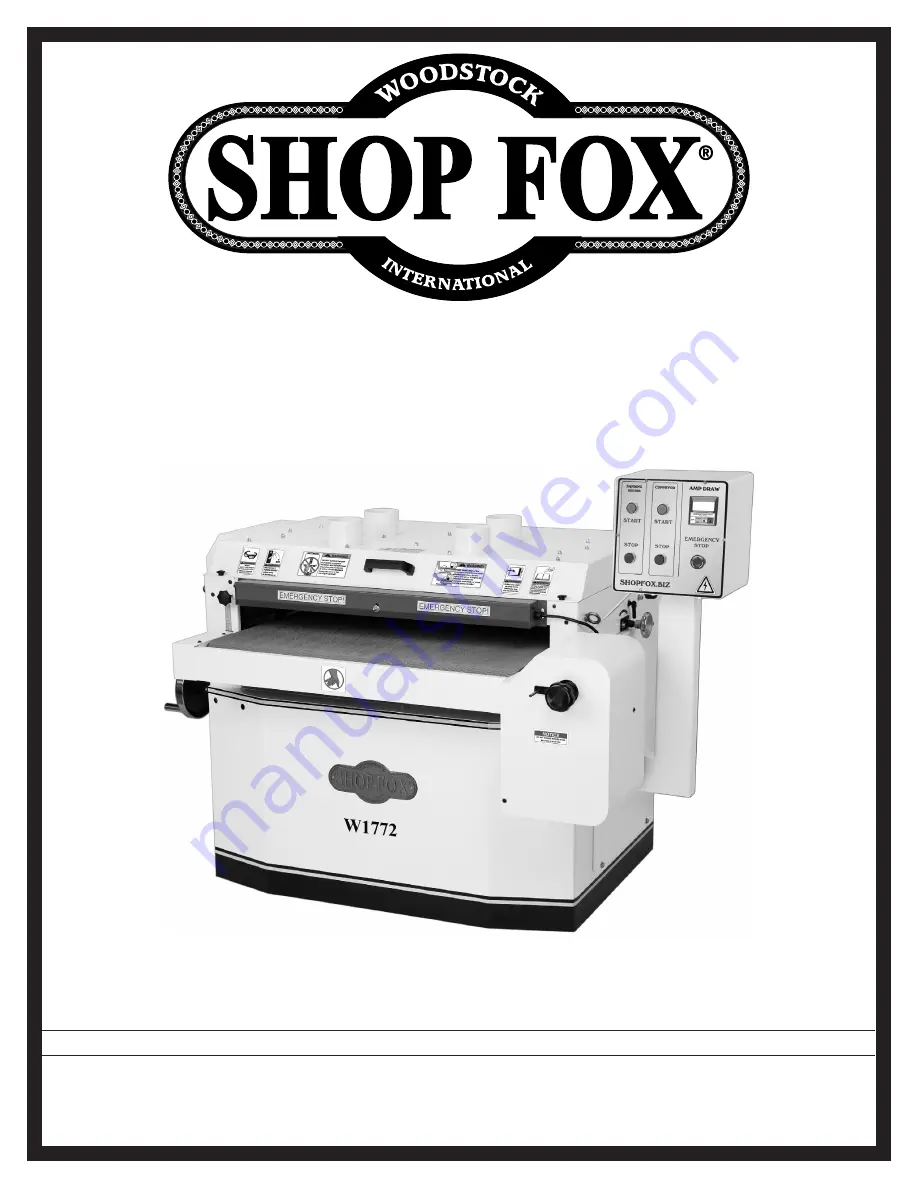
OWNER'S MANUAL
MODEL W1772/W1773
37" DRUM SANDER
Phone: (360) 734-3482 • Online Technical Support: [email protected]
COPYRIGHT © OCTOBER, 2007 BY WOODSTOCK INTERNATIONAL, INC.
WARNING: NO PORTION OF THIS MANUAL MAY BE REPRODUCED IN ANY SHAPE OR FORM WITHOUT
THE WRITTEN APPROVAL OF WOODSTOCK INTERNATIONAL, INC.
Printed in Taiwan
#9083BL
Summary of Contents for SHOP FOX W1772
Page 2: ......
Page 5: ...3 W1772 W1773 37 Drum Sander INTRODUCTION...
Page 6: ...4 W1772 W1773 37 Drum Sander INTRODUCTION...
Page 7: ...5 W1772 W1773 37 Drum Sander INTRODUCTION...
Page 8: ...6 W1772 W1773 37 Drum Sander INTRODUCTION...
Page 62: ...60 W1772 W1773 37 Drum Sander PARTS Conveyor Parts Breakdown...
Page 66: ...64 W1772 W1773 37 Drum Sander PARTS Electrical Components...
Page 72: ......