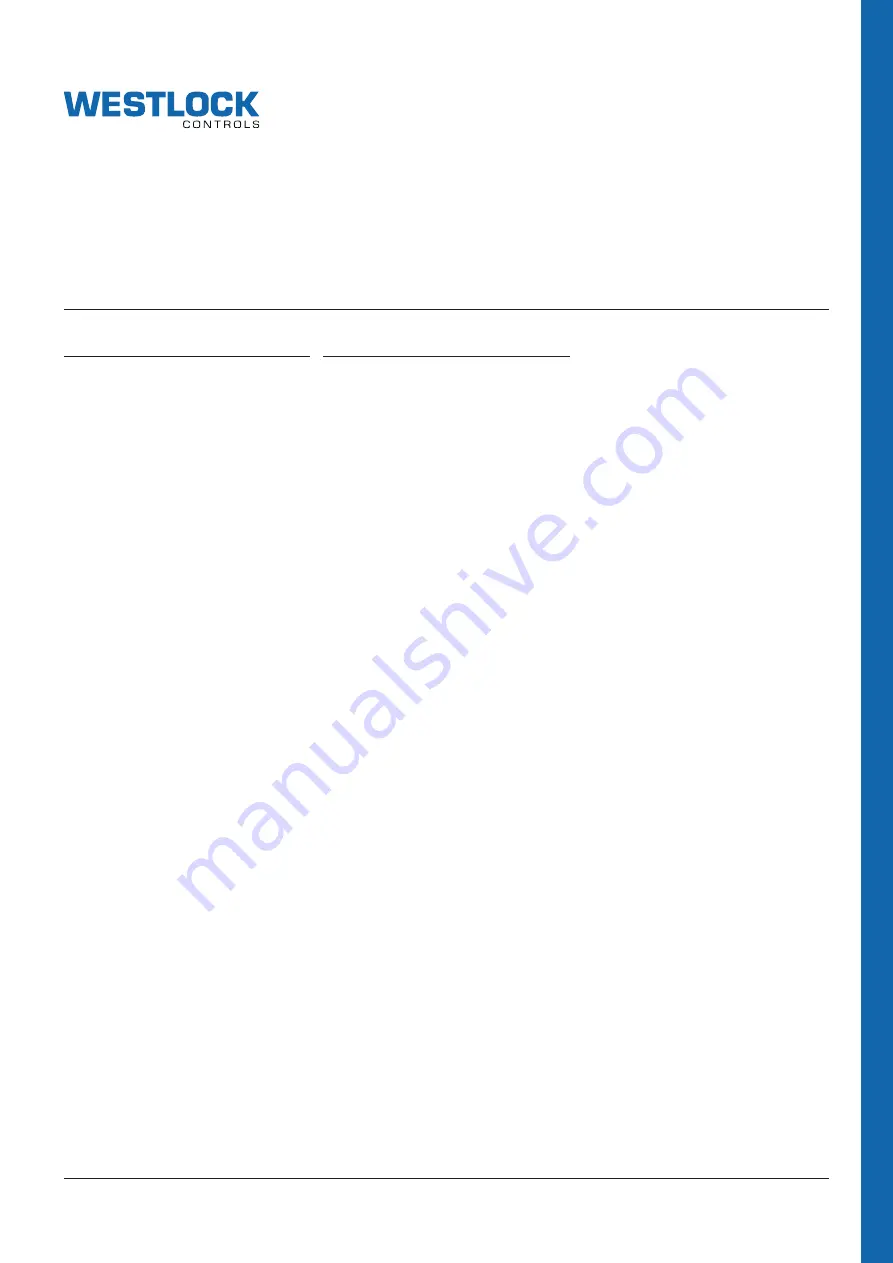
Page 1 of 33
DIGITAL EPIC-2
®
DTM
®
USER GUIDE
www.westlockcontrols.com
Copyright © Crane Co. All rights reserved.
VCIOM-04615-EN 17/03
TABLE OF CONTENTS
1 Introduction ................................................... 1
2 Installation ..................................................... 2
2.1 PACTWare ......................................... 2
2.2
HART Communication ...................... 2
2.3
DEPIC-2 DTM .................................... 2
3 Initial setup .................................................... 3
4 Parameterization (configuration) ................. 5
4.1 Login/Logout ..................................... 5
4.2
Device info ......................................... 5
4.3 Configuration .................................... 5
4.3.1 HART identification ........................... 5
4.3.2 Loop current ..................................... 6
4.3.3 View factory options .......................... 7
4.3.4 Factory defaults ................................ 7
4.3.5 Date/time setup ................................ 7
4.3.6 Basic configuration ........................... 8
4.3.7 PST configuration ........................... 10
4.3.8 Signature configuration .................. 12
4.3.9 SOVT configuration ......................... 13
4.3.10 Alert hysteresis configuration........ 13
4.3.11 Service/maintenance
configuration ................................... 14
4.3.12 Alarm configuration ........................ 14
5 Calibration ................................................... 16
5.1
Last full calibration ......................... 16
5.2
Full device controlled calibration .. 16
5.3
Full user controlled calibration ..... 17
5.4
Low position calibration ................. 17
5.5
High position calibration ................ 17
5.6
mA output calibration ..................... 17
5.7
PV Re-range .................................... 17
6 Diagnosis ..................................................... 18
6.1 Diagnostics ...................................... 18
6.1.1 Fixed mA loop test .......................... 18
6.1.2 Squawk ............................................ 18
6.1.3 Device reboot .................................. 18
6.1.4 FST ................................................... 19
6.1.5 PST ................................................... 25
6.1.6 SOVT ................................................ 28
6.2
Device specific status ..................... 29
6.2.1 Field device status .......................... 29
6.2.2 General alarm status ..................... 29
6.2.3 PST fail alarm status ...................... 29
6.2.4 Calibration error alarms ................ 30
6.2.5 Alert file ........................................... 31
6.2.6 Miscellaneous device status .......... 32
7 Abbreviations ............................................... 33
8 References ................................................... 33
1 INTRODUCTION
Westlock Controls Digital EPIC-2
®
is a second
generation ARM
®
Cortex-M3 microcontroller
based intelligent valve position transmitter with
an advanced diagnostics functions designed
especially for safety valves. The key application
of the DEPIC-2 is on emergency shut-down
valves to monitor the valve position in real-
time and perform diagnostics functions like
Partial-Stroke (PST), Full-Stroke Test (FST)
and Solenoid Operated Valve Test (SOVT) to
ensure valve will move to its fail-safe position
in emergency situation.
The DEPIC-2 is powered through the 9-24 V
analog signal from the control system and
provides 4-20 mA position feedback and digital
HART communication on the same signal to the
control system. The safety function is provided
from the 0-24 V digital signal from the safety
system to DEPIC-2 to de-energize the valve
during an emergency shutdown event.
A step by step guided setup wizard on 64x128
graphic LCD and 3 buttons provides an easy
way to configure, calibrate and operate the
device locally. In addition, the remote HART
®
DD or FDT
®
DTM can be used to configure,
calibrate and perform advanced diagnostics
functions on the device.
Under the hood is a powerful industry
leading low power 32 bit ARM
®
Cortex-M3
microcontroller with one non-contact Hall
Effect position sensor, two pressure sensors
and one temperature sensor. The low power
operation of the microcontroller keeps the
device operating even at 3.8 mA with HART
®
communication during an ESD event.
The DEPIC-2 can be easily mounted using
NAMUR compatible mounting kits on linear
or rotary actuator. The completely sealed and
potted electronics are resistant to dirt and
moisture and expanded temperature range of
-40°C to +85°C enhances the reliability of the
device to work in harsh environments.