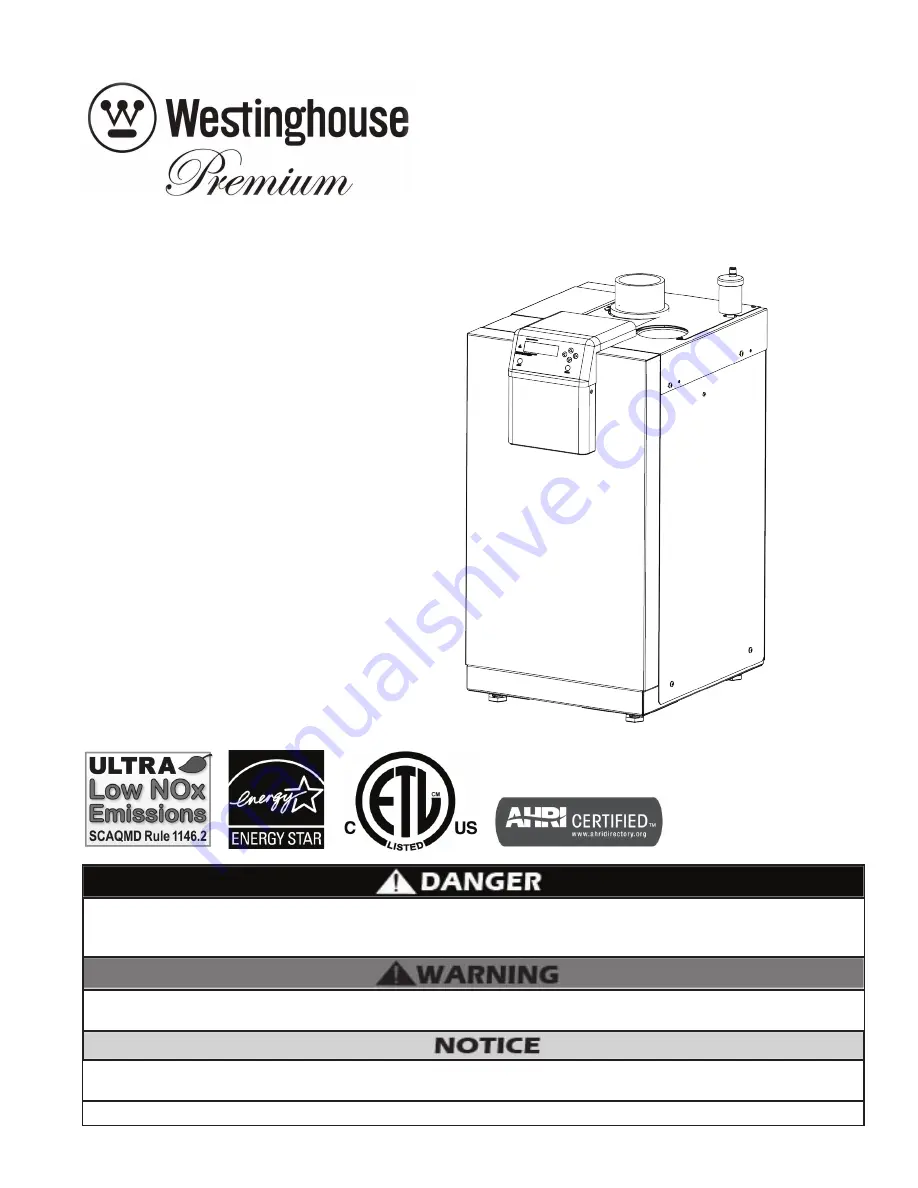
Premier
High Efficiency
Boilers
Installation
Start-Up
Maintenance
Parts
Warranty
WBRE**80 / 110 / 150 / 220 / 299 / 301 / 399
Models*
* “NG” Denotes Natural Gas Operation
“LP” Denotes Propane Gas Operation
This manual must only be used by a qualified installer / service technician. Read all instructions in this manual before
installing. Perform steps in the given order. Failure to do so could result in substantial property damage, severe
personal injury, or death.
Westinghouse reserves the right to make product changes or updates without notice and will not be held liable for
typographical errors in literature.
NOTE TO CONSUMER: PLEASE KEEP ALL INSTRUCTIONS FOR FUTURE REFERENCE.
WHL-052 Rev. 4.28.16
Improper installation, adjustment, alteration, service, or maintenance could void product warranty and cause
property damage, severe personal injury, or death.
Heat Exchanger Bears the ASME “H” Stamp
Summary of Contents for WBRE110
Page 13: ...WHL 052 Rev 4 28 16 13 Figure 5 Boiler Dimensions NOTE All Dimensions Are Approximate ...
Page 37: ...WHL 052 Rev 4 28 16 37 Figure 25 Internal Connection Diagram ...
Page 62: ...WHL 052 Rev 4 28 16 62 Figure 30 Combustion System Replacement Parts 80 220kBTU Models ...
Page 63: ...WHL 052 Rev 4 28 16 63 Figure 31 Combustion System Replacement Parts 299 399kBTU Models ...
Page 64: ...WHL 052 Rev 4 28 16 64 Figure 32 Cabinet Replacement Parts All Models ...
Page 65: ...WHL 052 Rev 4 28 16 65 Figure 33 Cabinet Replacement Parts All Models ...