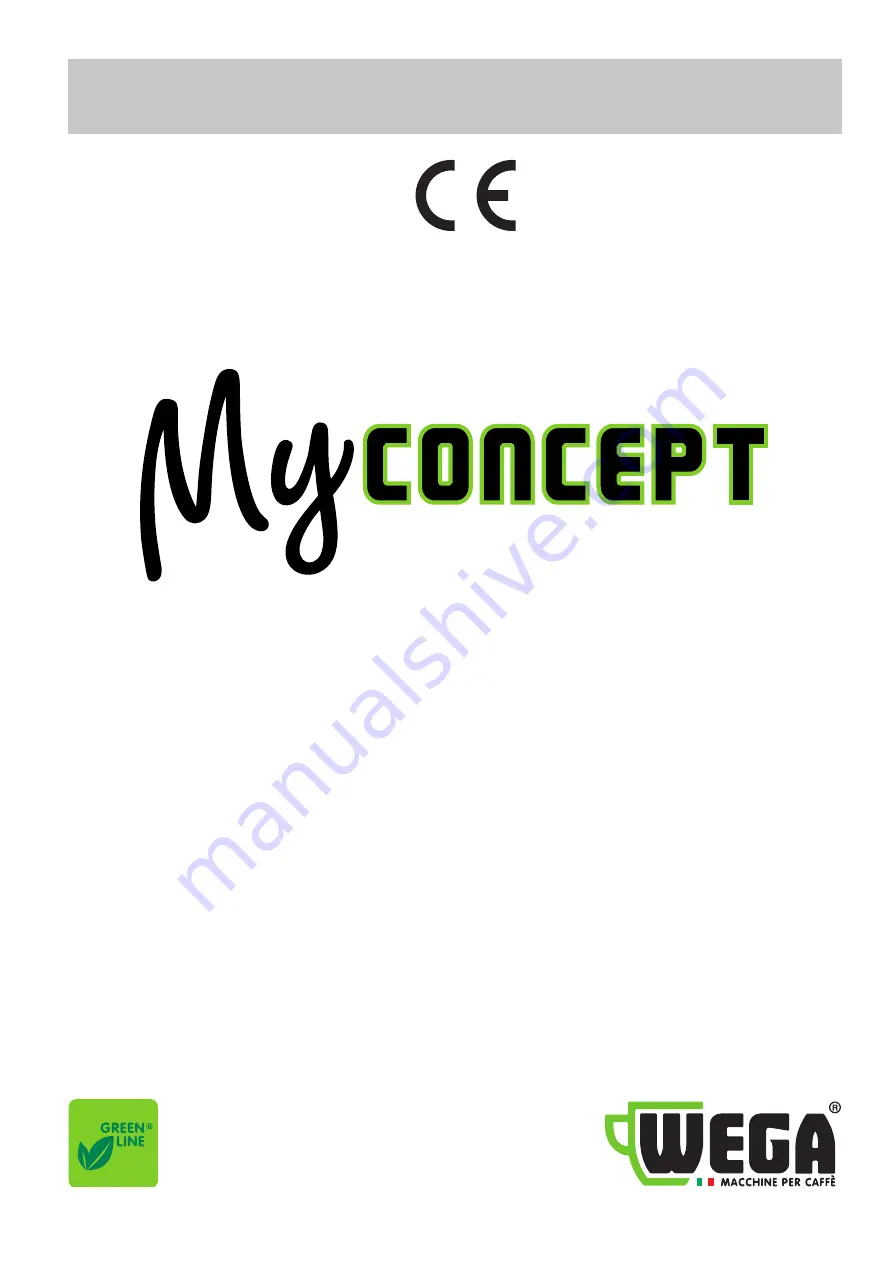
WEGA MACCHINE PER CAFFÈ S.r.l.
Via Condotti Bardini, 1 - 31058 SUSEGANA (TV) - ITALY - Tel. +39.0438.1799700 - Fax +39.0438.1884890 - www.wega.it - [email protected]
2006/42/CE Direttiva macchine
EVDP
ESPRESSO COFFEE MACHINE
Use and maintenance manual. TECHNICIANS instructions.
FONDO VERDE CHIARO PANTONE 376C
LOGO VERDE SCURO PANTONE 348C
FONDO VERDE CHIARO C:56; M:0; Y:100; K:0
LOGO VERDE SCURO C:100; M:0; Y:79; K:28