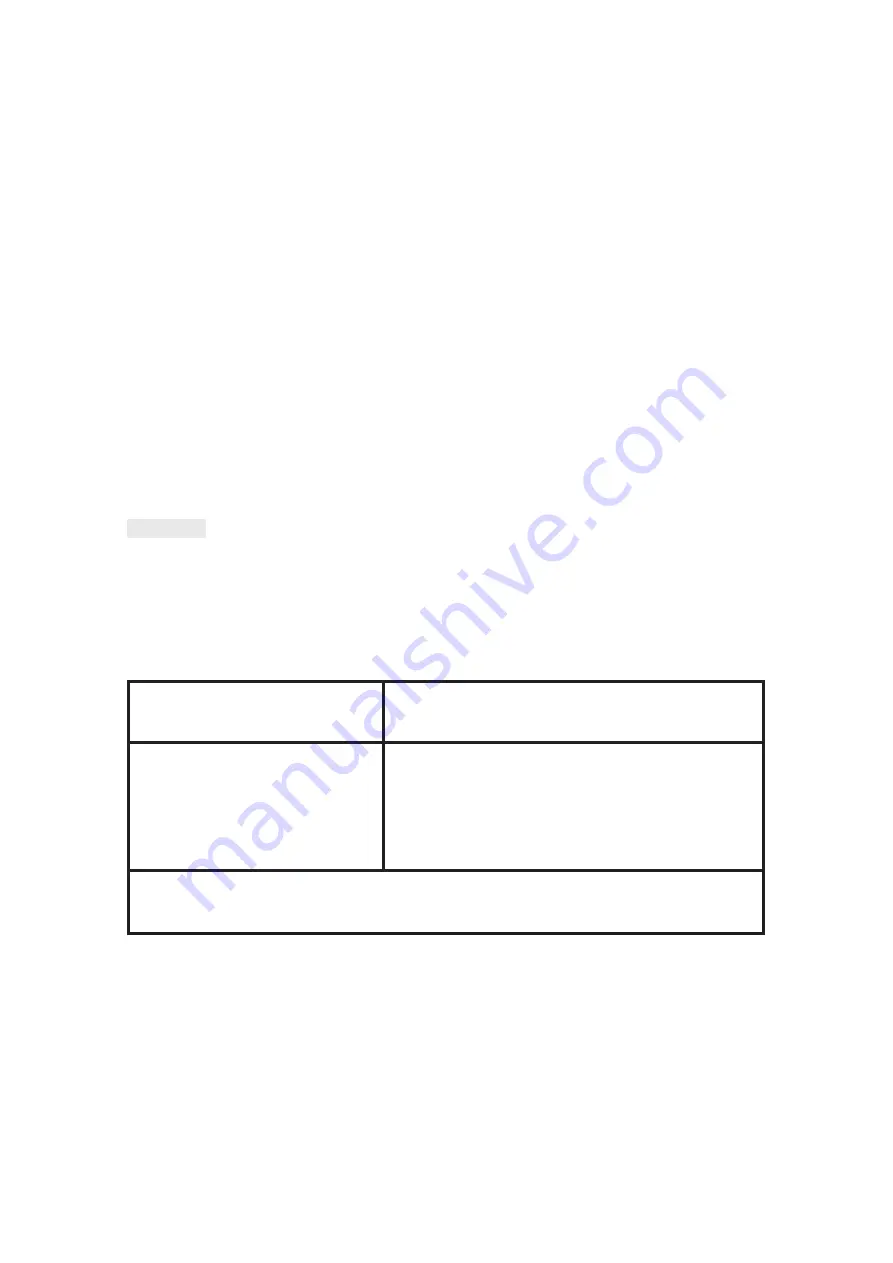
WARNING: ALL OPERATING AND MAINTENANCE PROCEDURES SHOWN ON THE NEXT
PAGE OF THIS MANUAL MUST BE FOLLOWED DAILY FOR PROPER OPERATION OF
YOUR WASCOMAT MACHINE.
PLEASE ENTER THE FOLLOWING INFORMATION AS IT APPEARS ON THE MACHINE(S)
DATA PLATE(S).
MAKE CERTAIN TO KEEP THIS MANUAL IN A SECURE PLACE FOR FUTURE
REFERENCE.
MACHINE TYPE OR MODEL
MACHINE SERIAL NUMBER(S)
ELECTRICAL CHARACTERISTICS: ________
VOLTS, _______ PHASE, _______
HZ.
OPERATING & MAINTENANCE MANUAL
WASCOMAT JUNIOR W 75
WASCOMAT SUPER JUNIOR W 105
WASCOMAT SENIOR W 125
WASCOMAT GIANT W 185
471 1562-75/04
00.23
Summary of Contents for Giant W 185
Page 2: ......
Page 6: ......
Page 38: ...31 40 Mechanical and electrical design 1700 W125 208 240 V 60 Hz single phase ...
Page 39: ...32 40 Mechanical and electrical design 1791 ...
Page 55: ......
Page 56: ......