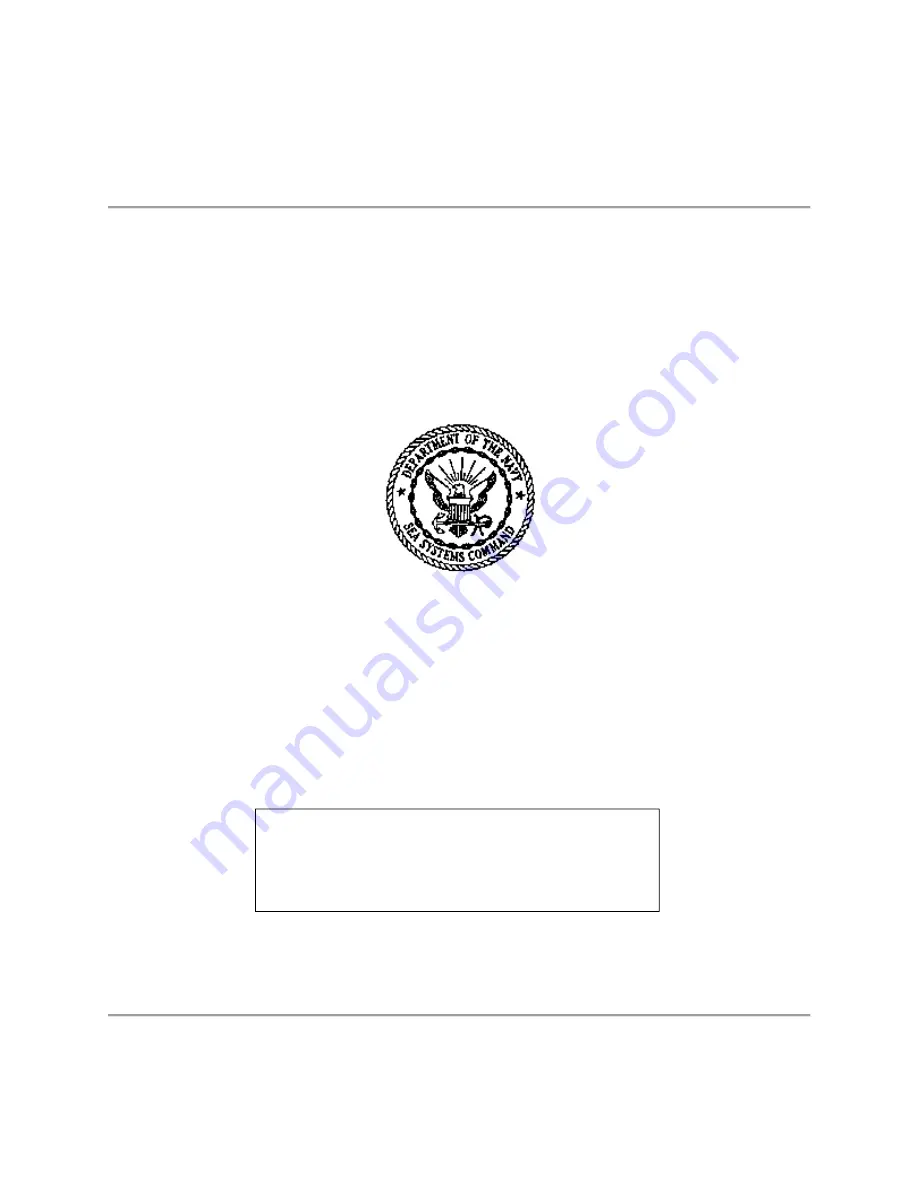
S6161-1L-FSE-010
0910-LP-113-0825
INSTALLATION AND OPERATION MANUAL FOR
JACKSON MSC
MODEL 10AB-N70 DISHWASHER
N00024-11-C-2111
JACKSON MSC, LLC.
P.O. BOX 1060
HWY. 25E
BARBOURVILLE, KY 40906
PUBLISHED BY DIRECTION OF COMMANDER, NAVAL SEA SYSTEMS COMMAND
APRIL 29, 2013
STATEMENT A
APPROVED FOR PUBLIC RELEASE
DISTRIBUTION UNLIMITED.
Summary of Contents for 10AB-N70
Page 8: ...Revision Letter Revision Date Made By Applicable ECNs Details...
Page 59: ...APPENDIX A DEMA Nitro Warewash Dispenser A 1...
Page 61: ...Part 1 Nitro Warewash Dispenser User s Manual...
Page 70: ...Part 2 Solid Rinse Bowl Installation Instructions...
Page 75: ...Part 3 Viking Bowl Installation Instructions...
Page 78: ...Part 4 Nitro Warewash Dispenser Training Manual...