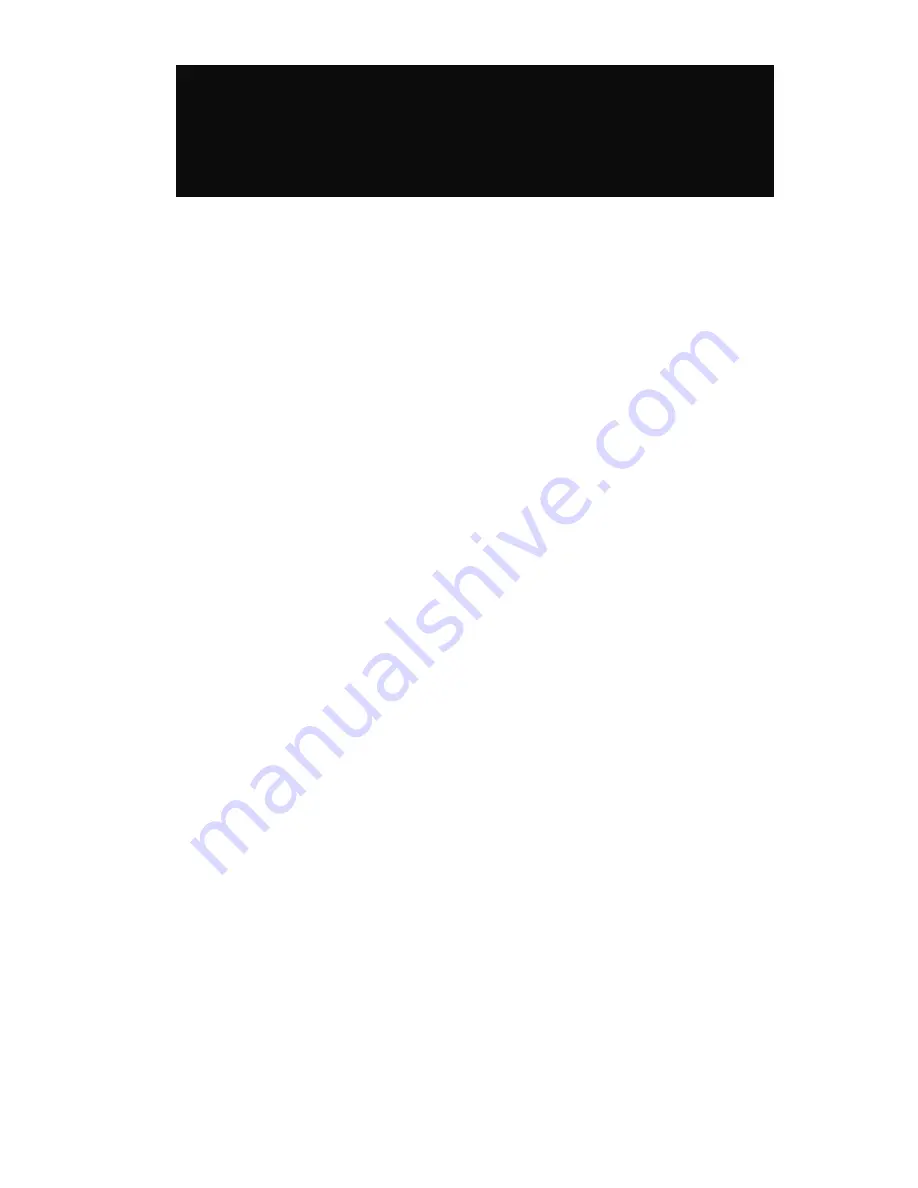
VMAC – Vehicle Mounted Air Compressors
Toll Free:
1-800-738-8622 Local: 1-250-740-3200
Fax: 1-250-740-3201
1
Installation Manual
PREDATAIR60
Hydraulic Compressor
1.0 General Information ...................................................................3
1.1 Specifications and Components ...............................................3
2.0 Installation Requirements..........................................................6
2.1 Ventilation Requirements..........................................................6
2.2 Hydraulic Requirements..........................................................11
2.3 Electrical Requirements ..........................................................12
2.4 Air Receiver Requirements .....................................................13
3.0 Installing the PREDATAIR60 ...................................................15
3.1 Mounting the Compressor.......................................................15
3.2 Connecting the Wiring.............................................................15
3.3 Speed Control .........................................................................20
4.0 Completing the Installation .....................................................23
4.1 Before Operation Checklist .....................................................23
4.2 After Engaging the Hydraulics Checklist.................................23
4.3 Setup, Performance Testing and Adjustments .......................24
5.0 Testing Ventilation ...................................................................26
5.1 Calculating Duty Cycle............................................................26
5.2 Testing the Installation ............................................................28
5.3 Analyzing the Test Results .....................................................31
6.0 Hydraulic System Data.............................................................34
6.1 Hydraulic Oil Type...................................................................34
6.2 Hydraulic Line Sizing ..............................................................35
6.3 Hydraulic System Filtration .....................................................40
6.4 Hydraulic Oil Reservoir ...........................................................40
6.5 Avoiding Cavitation .................................................................44
Ordering Parts.................................................................................44