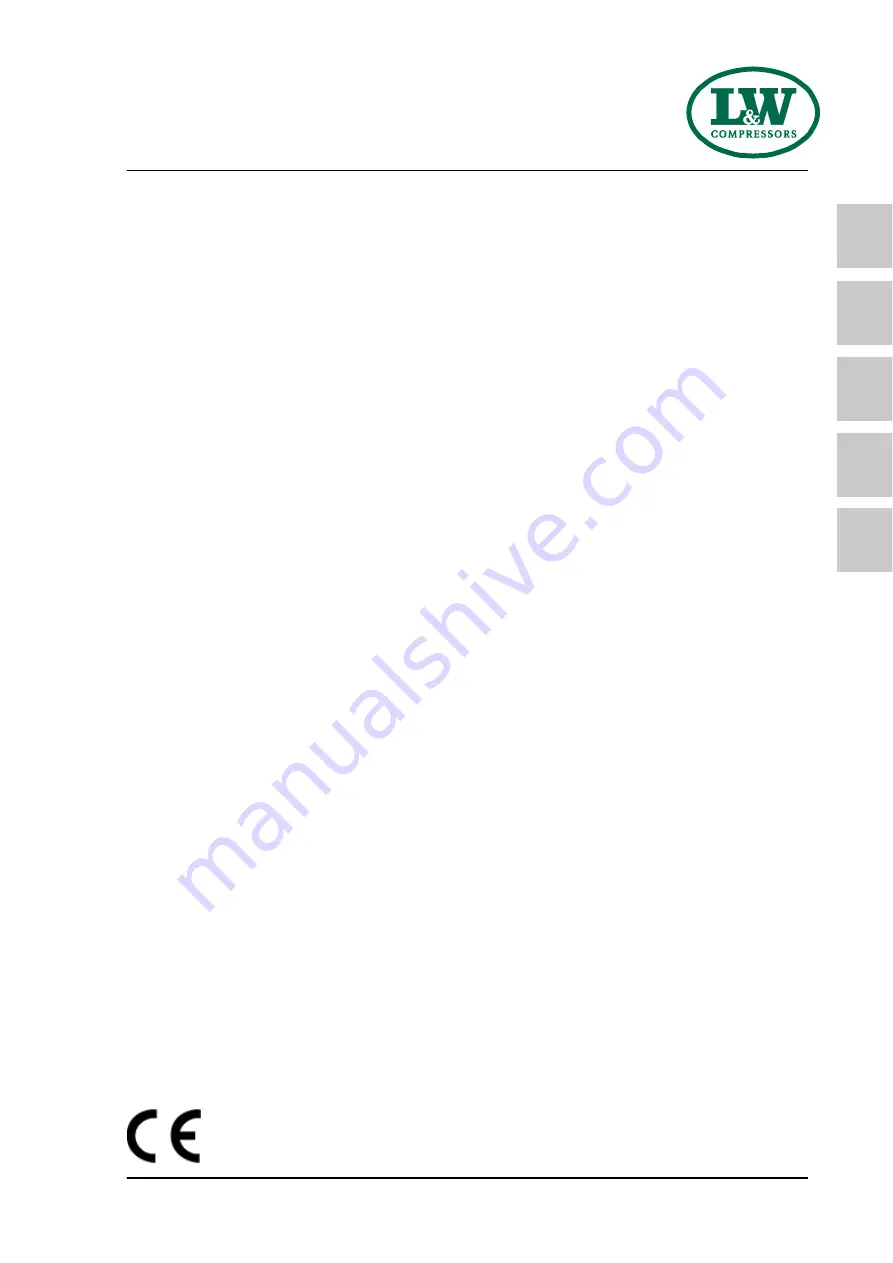
C H A P T E R O V E R V I E W
Operating Instructions
..............................................................................................................
ECC - Electronic Compressor Control (if equipped)
.........................................................
Spare Parts Lists
..........................................................................................................................
Options
(if equipped)
.................................................................................................................
Attachment
....................................................................................................................................
A
B
C
D
E
Manufacturer in terms of 97/23/EC
The full name and address of the manufacturer is:
Lenhardt & Wagner GmbH
An der Tuchbleiche 39
68623 Hüttenfeld / Germany
Phone: +49 (0) 62 56 - 85 88 0 - 0
Fax: +49 (0) 62 56 - 85 88 0 - 14
E-Mail: [email protected]
Internet: www.lw-compressors.com
Version: 21.06.2013
Содержание LW 230 ES
Страница 3: ...A Operating Instructions Breathing Air Compressor LW 230 ES LW 280 ES LW 320 ES Version 02 01 2017 ...
Страница 12: ...A S A F E T Y P R E C A U T I O N S ...
Страница 19: ...A I N S TA L L AT I O N ...
Страница 26: ...A O P E R AT I O N ...
Страница 34: ...A R E M E D Y I N G FA U LT S ...
Страница 39: ...A M A I N T E N A N C E A N D S E R V I C E ...
Страница 68: ...A M A I N T E N A N C E R E C O R D S ...
Страница 76: ...B Operating Instructions ECC Electronic compressor control www uebler net Version 11 12 E ...
Страница 96: ...C ERSATZTEILLISTEN SPARE PARTS LISTS DETAILANSICHTEN DETAILED VIEWS ...
Страница 109: ...C Version 11 05 2016 Baugruppe Kompressorblock Assembly Compressor Block C 13 LW 230 280 320 ES ...
Страница 158: ...D O P T I O N S ...
Страница 160: ...D A U T O S T A R T F U N C T I O N D 2 LW 230 280 320 ES ...
Страница 165: ...D O I L P R E S S U R E G A U G E D 7 LW 230 280 320 ES ...
Страница 168: ...D O I L P R E S S U R E M O N I T O R I N G D 10 LW 230 280 320 ES ...
Страница 172: ...D O I L T E M P E R A T U R E M O N I T O R I N G D 14 LW 230 280 320 ES ...
Страница 175: ...D I N T E R S TA G E P R E S S U R E G A U G E D 17 LW 230 280 320 ES ...
Страница 179: ...D C Y L I N D E R H E A D T E M P E R AT U R E M O N I T O R I N G D 21 LW 230 280 320 ES ...
Страница 182: ...D 2 0 0 3 0 0 B A R PA R A L L E L F I L L I N G P R E S S U R E O P E R AT I O N D 24 LW 230 280 320 ES ...
Страница 186: ...D A I R C O O L E R C O N N E C T I O N K I T D 28 LW 230 280 320 ES ...
Страница 189: ...D C O N D E N S A T E TA N K 6 0 LT R D 31 LW 230 280 320 ES ...
Страница 194: ...E A T T A C H M E N T Version 11 12 E ...