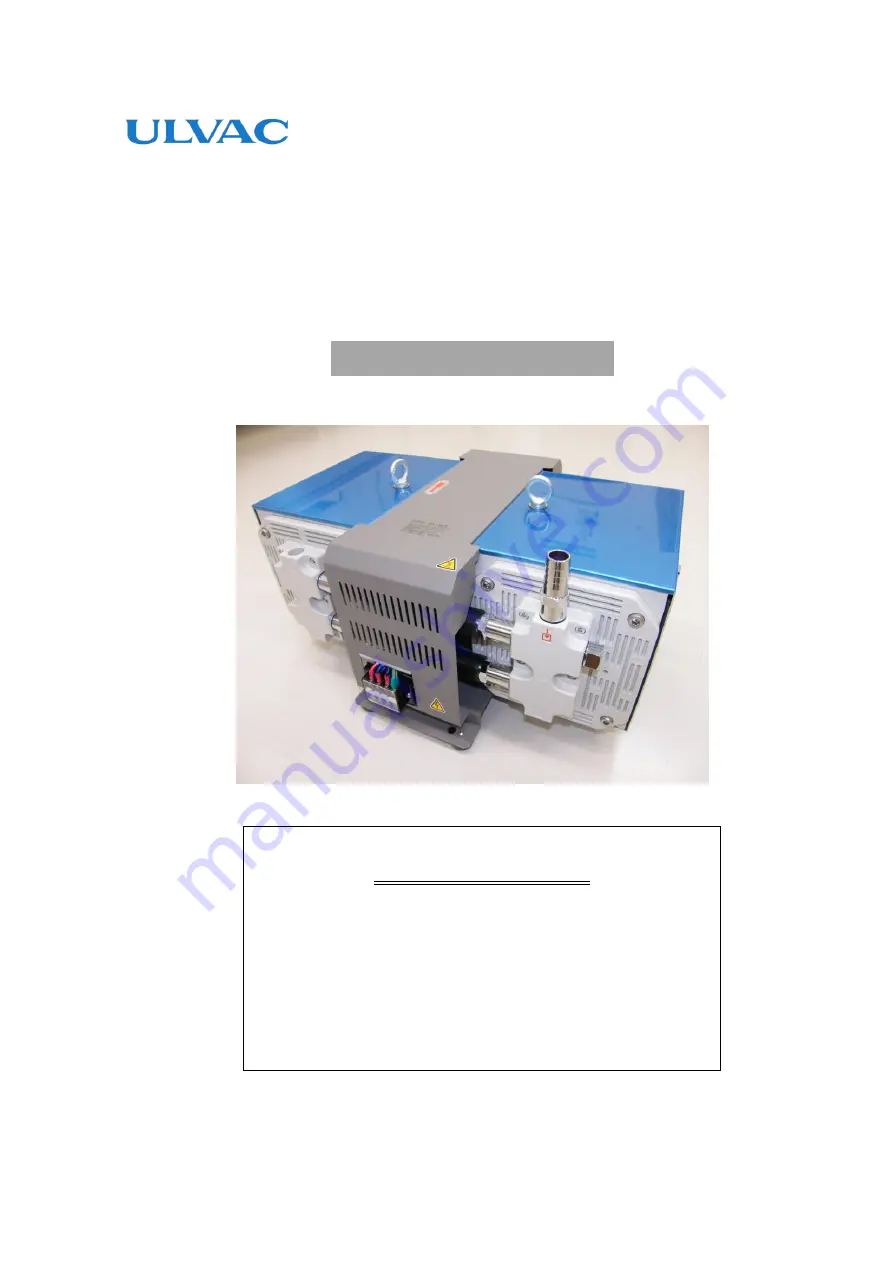
No.27700-2-01-8
INSTRUCTION MANUAL
Diaphragm-type Dry Vacuum Pump
Model: DAL-181D, 361S
Request to Users
Please read this manual thoroughly to ensure safe and
effective use of the equipment.
Keep this manual in a safe place.
Due to periodic improvements in performance, the
equipment described in this manual is subject to
changes in dimensions and specifications without prior
notice.
ULVAC KIKO,Inc.