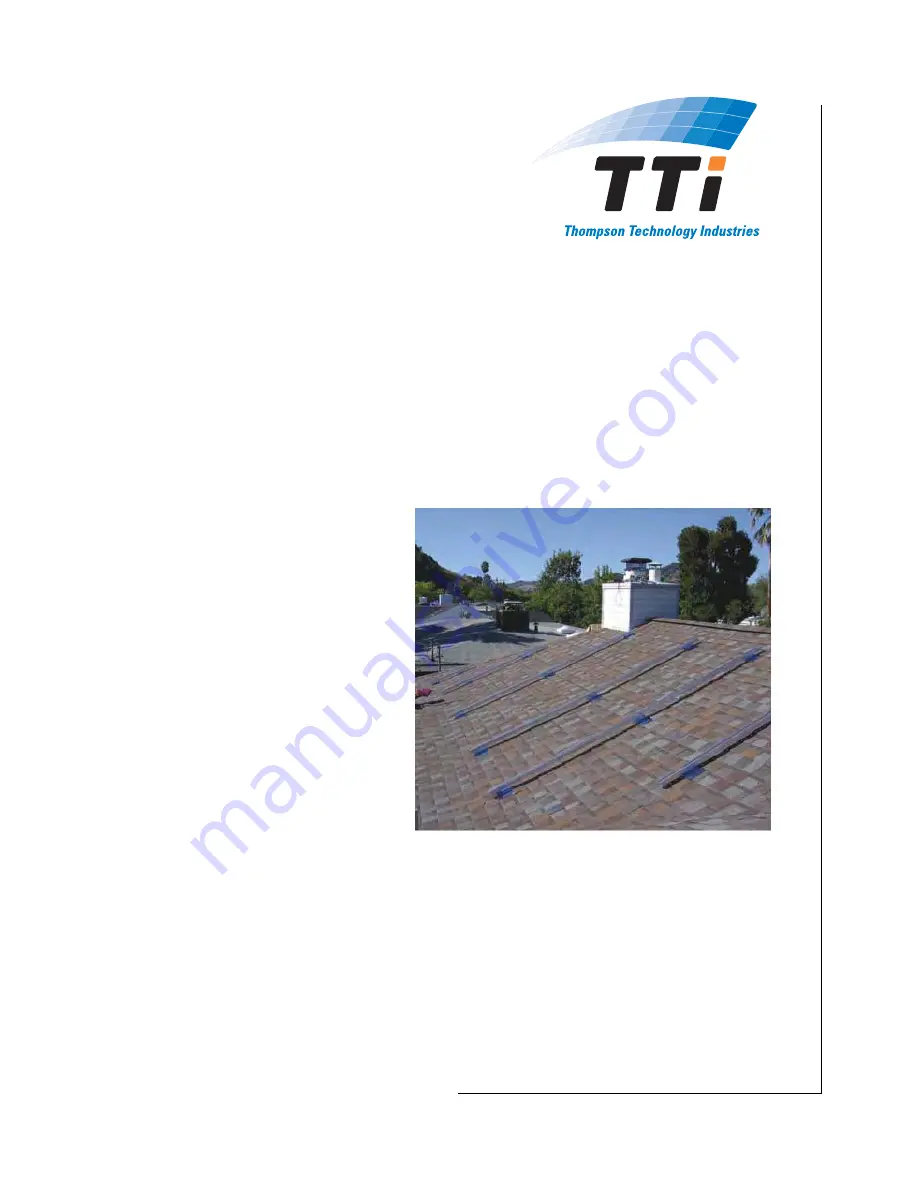
Proprietary Information
Thompson Technology Industries, Inc.
16 Digital Drive
Novato, CA 94949
www.thompsontec.com
Installation Manual
FLAT JACK® Low-Profile Roof Mount
System
Part Number 99906 Rev. D
Release 11.17.2008
NOTICE
This document is proprie-
tary, and must not be repli-
cated. It is for TTi internal
use only and is subject to
changes for upgrades and
improvements.
Summary of Contents for FLAT JACK
Page 6: ...This page intentionally blank ...
Page 14: ...This page intentionally blank ...
Page 28: ...This page intentionally blank ...