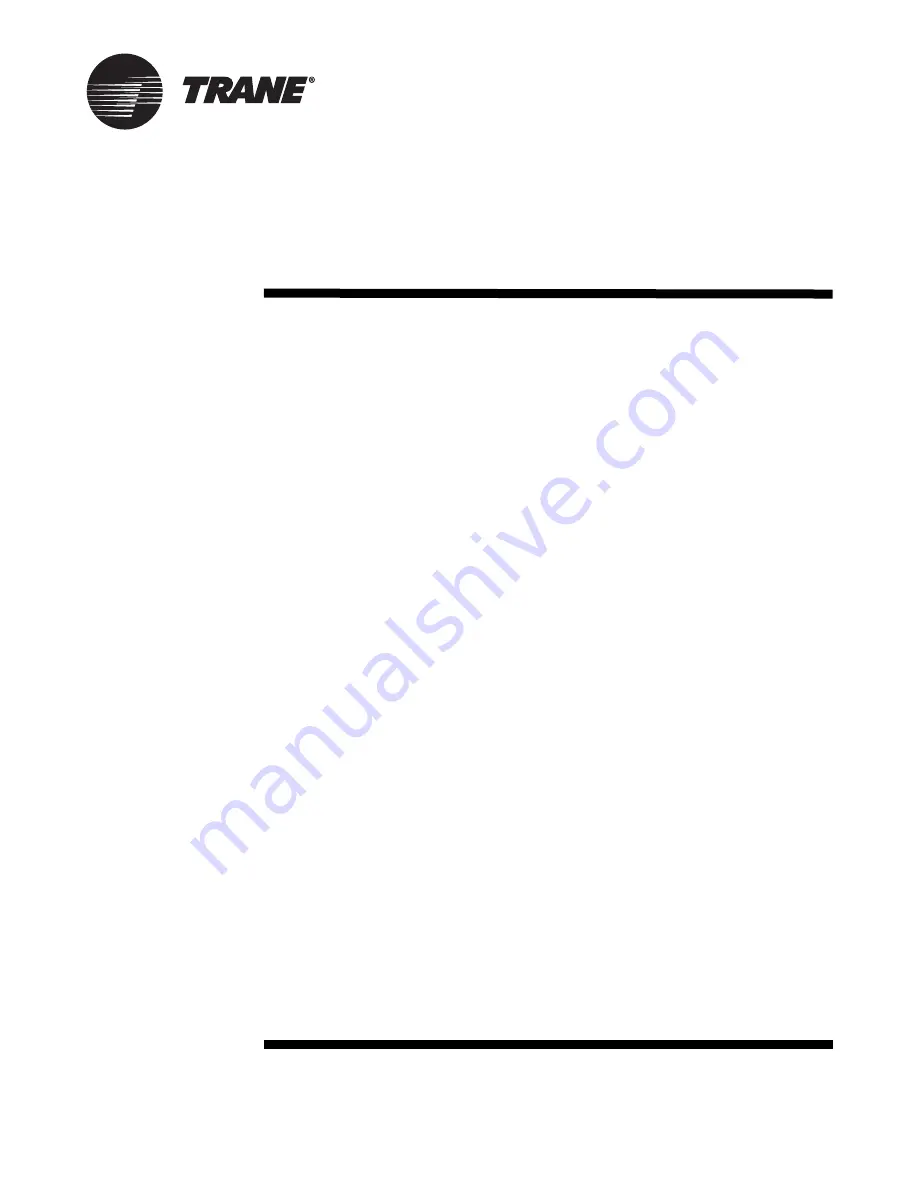
Service Alert
RTHD and RTAC
Control Operation, Setup and
Troubleshooting for RTAC and RTHD Units
with Tracer CH530 Controls
The purpose of this bulletin is to provide control operation and general
troubleshooting information on the RTAC Air Cooled Chillers and RTHD Water
Cooled Chillers with the CH530 controls. It is recommended that the service
technician be familiar with the CH530 operation prior to servicing the
microprocessor.
This bulletin is intended to serve as a supplement to the RTAC and RTHD IOMs,
the installation, operation and maintenance manuel. Subjects covered in this
bulletin are intended to provide more comprehensive information for the RTAC
and RTHD units.
Diagnostic
Troubleshooting
Repair
November 2005
RLC-SVD05A-EN