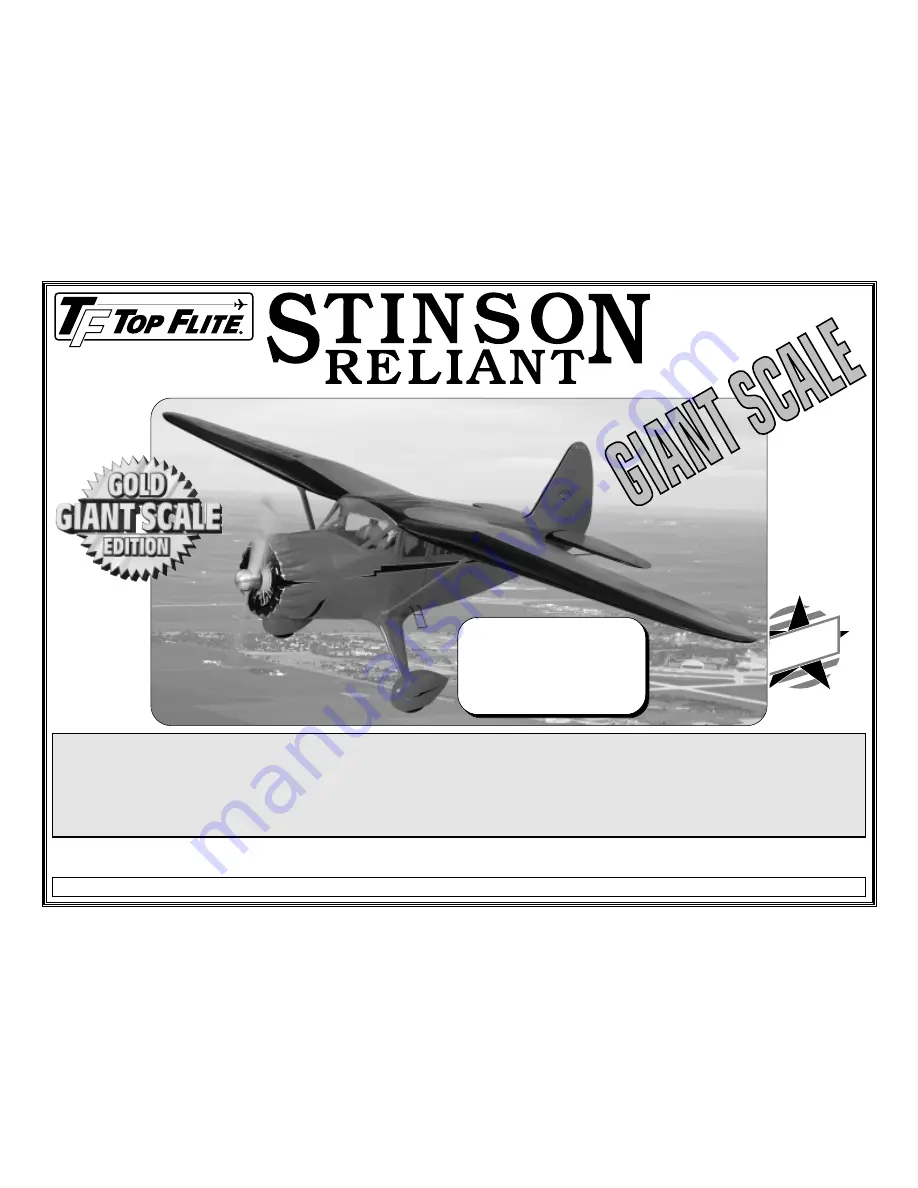
WARRANTY.....
Top Flite Models guarantees this kit to be free of defects in both material and workmanship at the date of purchase. This warranty does
not cover any component parts damaged by use or modification. In no case shall Top Flite‘s liability exceed the original cost of the purchased kit. Further, Top Flite reserves
the right to change or modify this warranty without notice. In that Top Flite has no control over the final assembly or material used for final assembly, no liability shall be assumed
nor accepted for any damage resulting from the use by the user of the final user-assembled product. By the act of using the user-assembled product the user accepts all
resulting liability.
If the buyer is not prepared to accept the liability associated with the use of this product, the buyer is advised to immediately return this kit in new and
unused condition to the place of purchase.
Top Flite Models P.O. Box 788 Urbana, Il 61803
Technical Assistance Call (217)398-8970 [email protected]
READ THROUGH THIS INSTRUCTION BOOK FIRST. IT CONTAINS IMPORTANT INSTRUCTIONS AND WARNINGS CONCERNING THE ASSEMBLY AND USE OF THIS MODEL.
USA
M
ADE IN
STNGP03
V1.0
Entire Contents © Copyright 1999
Wingspan:
100.5" [2553mm]
Wing Area:
1487 sq. in. [95.9 sq. dm]
Weight:
16 - 25 Lbs. [7258 - 11340g]
Wing Loading:
24.8 - 38.7 oz./sq. ft.
[75.7 - 118.1 g/sq. dm]
Fuselage Length:
67.8 in. [1722mm]
Summary of Contents for Stinson Reliant
Page 8: ... 8 DIE CUT PATTERNS ...
Page 9: ... 9 DIE CUT PATTERNS ...
Page 57: ......
Page 58: ......
Page 59: ......
Page 60: ......