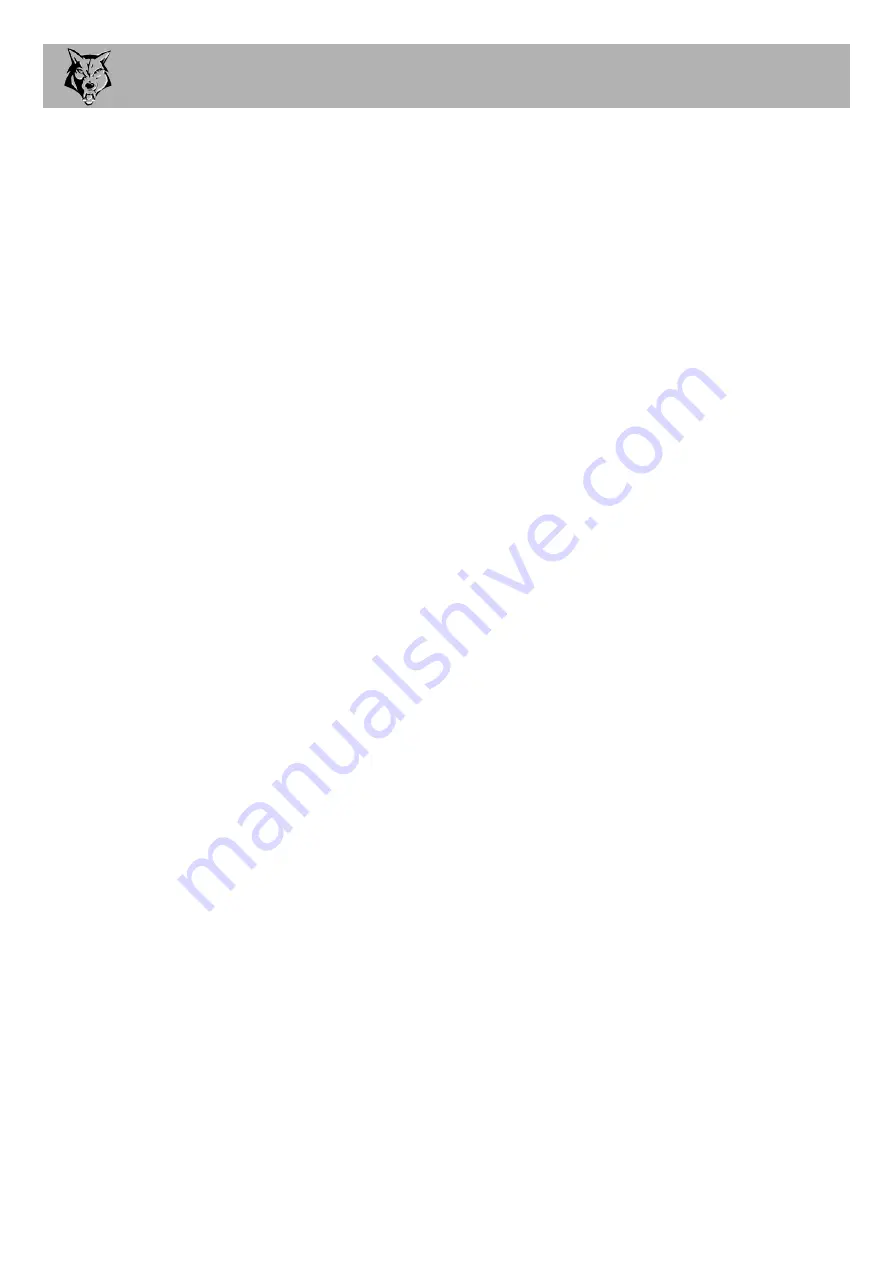
CONTENTS
Section
Page No.
INTRODUCTION
1
PURPOSE OF MACHINE
2
MACHINE DIMENSIONS & SPECIFICATIONS
2
PARTS LOCATION DIAGRAMS
3 & 4
SAFE WORKING
5
Operator’s Personal Protective Equipment Required
5
Basic Woodchipping Safety
5
General Safety Matters - Do’s and Dont’s
6
Noise Test
7
OPERATING INSTRUCTIONS
8
Safe Transportation
8
Hitching onto the Tow Ball
8
Unhitching the Chipper
8
Delivery
9
Operator’s Personal Protective Equipment Required
9
Engine Controls
9
Starting the Engine
9
Stopping the Engine
10
Daily Checks Before Starting
10
Starting to Chip
10
Chipping
10
Blade Wear
11
Blockages
11
SERVICE INSTRUCTIONS
12
Service Schedule
13
Engine Servicing
13
Engine Manufacturers Handbook
13
Spares
13
Safe Maintenance
14
Copper Ease Safety Information
14
Safe Lifting of the Chipper
14
Check Fittings
14
Change Blades
15
Tension Drive Belts
15
WARRANTY STATEMENT
16
EC DECLARATION OF CONFORMITY CERTIFICATE
17
DECALS
18 & 19
PARTS LISTS
20 - 29
16th Sept 09
Summary of Contents for TW 18/100G
Page 18: ...CERTIFICATE OF CONFORMITY 17...