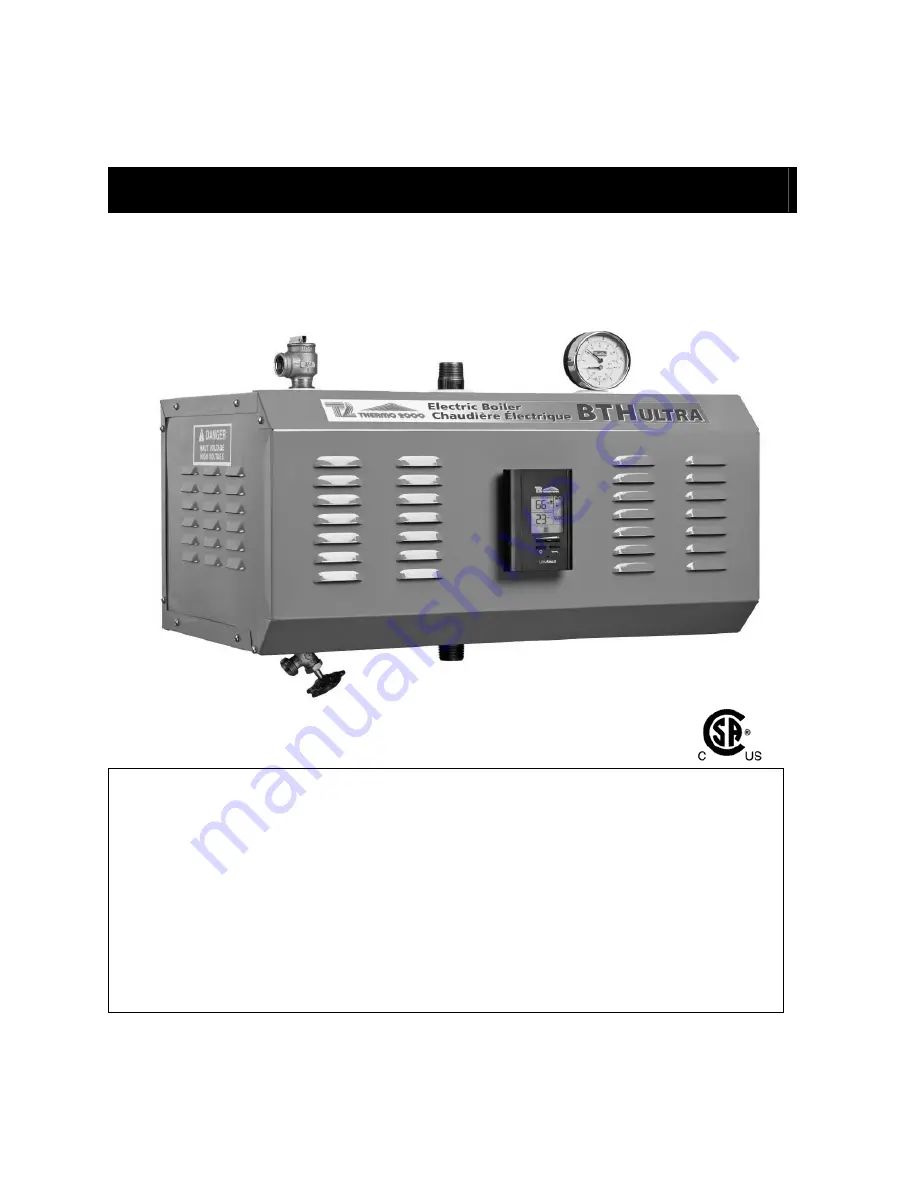
BTH
ULTRA
Electric Boilers
M
odel s rangi ng from 6 kW to 33 kW :
120/ 24 0 V ol t s ( 1 ph a se )
INSTALLATION & OPERATION MANUAL
Your
BTH ULTRA Electric Boiler
has been carefully assembled and factory tested to provide
years of trouble-free service. The following information and safety measures are provided to
enable proper installation, operation, and maintenance of this product.
It is imperative that all persons who are expected to install, operate or adjust this boiler should
read these instructions carefully.
Any questions regarding the operation, maintenance, service or warranty of this electric boiler
should be directed to the supplier.
When all installation steps have been completed, insert this installation manual in its original
envelope, and keep in a safe place (close to the boiler) for future reference.
THERMO 2000 INC.
revision : April 2011
Printed in Canada