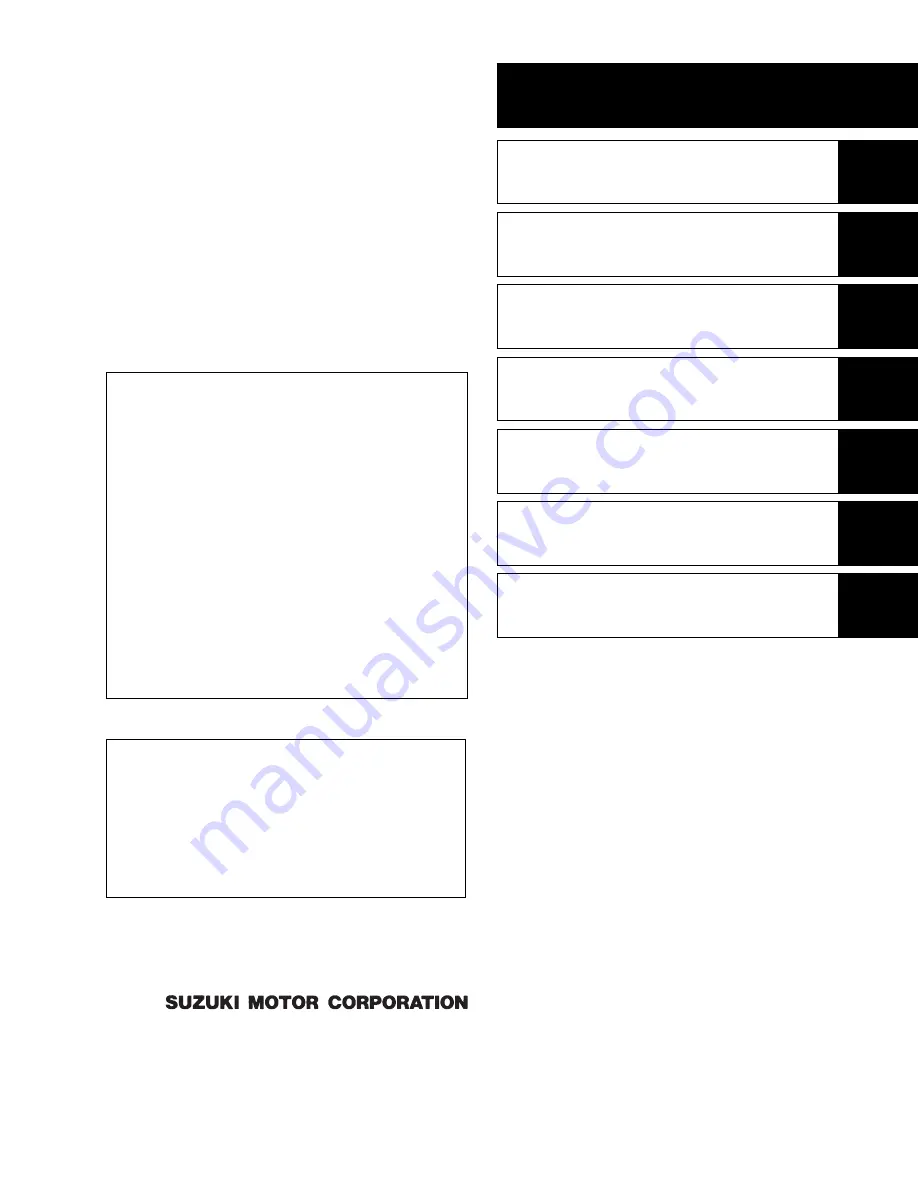
GROUP INDEX
GENERAL INFORMATION
1
PERIODIC MAINTENANCE
2
ENGINE
3
FUEL SYSTEM
4
CHASSIS
5
ELECTRICAL SYSTEM
6
SERVICING INFORMATION
7
FOREWORD
This manual contains an introductory description on
the SUZUKI LT-Z50 and procedures for its inspec-
tion/service and overhaul of its main components.
Other information considered as generally known is
not included.
Read the GENERAL INFORMATION section to
familiarize yourself with the vehicle and its mainte-
nance. Use this section as well as other sections to
use as a guide for proper inspection and service.
This manual will help you know the vehicle better so
that you can assure your customers of fast and reli-
able service.
© COPYRIGHT SUZUKI MOTOR CORPORATION 2005
* This manual has been prepared on the basis
of the latest specifications at the time of publi-
cation. If modifications have been made since
then, differences may exist between the con-
tent of this manual and the actual vehicle.
* Illustrations in this manual are used to show
the basic principles of operation and work
procedures. They may not represent the
actual vehicle exactly in detail.
* This manual is written for persons who have
enough knowledge, skills and tools, including
special tools, for servicing SUZUKI vehicles.
If you do not have the proper knowledge and
tools, ask your authorized SUZUKI motorcy-
cle dealer to help you.
Inexperienced mechanics or mechanics
without the proper tools and equipment
may not be able to properly perform the
services described in this manual.
Improper repair may result in injury to the
mechanic and may render the vehicle
unsafe for the rider.
99500-40011-03E
PartShark.com
877-999-5686
Summary of Contents for LT-Z50
Page 2: ...P a r t S h a r k c o m 8 7 7 9 9 9 5 6 8 6 ...
Page 15: ...P a r t S h a r k c o m 8 7 7 9 9 9 5 6 8 6 ...
Page 36: ...PERIODIC MAINTENANCE 2 21 P a r t S h a r k c o m 8 7 7 9 9 9 5 6 8 6 ...
Page 41: ...P a r t S h a r k c o m 8 7 7 9 9 9 5 6 8 6 ...