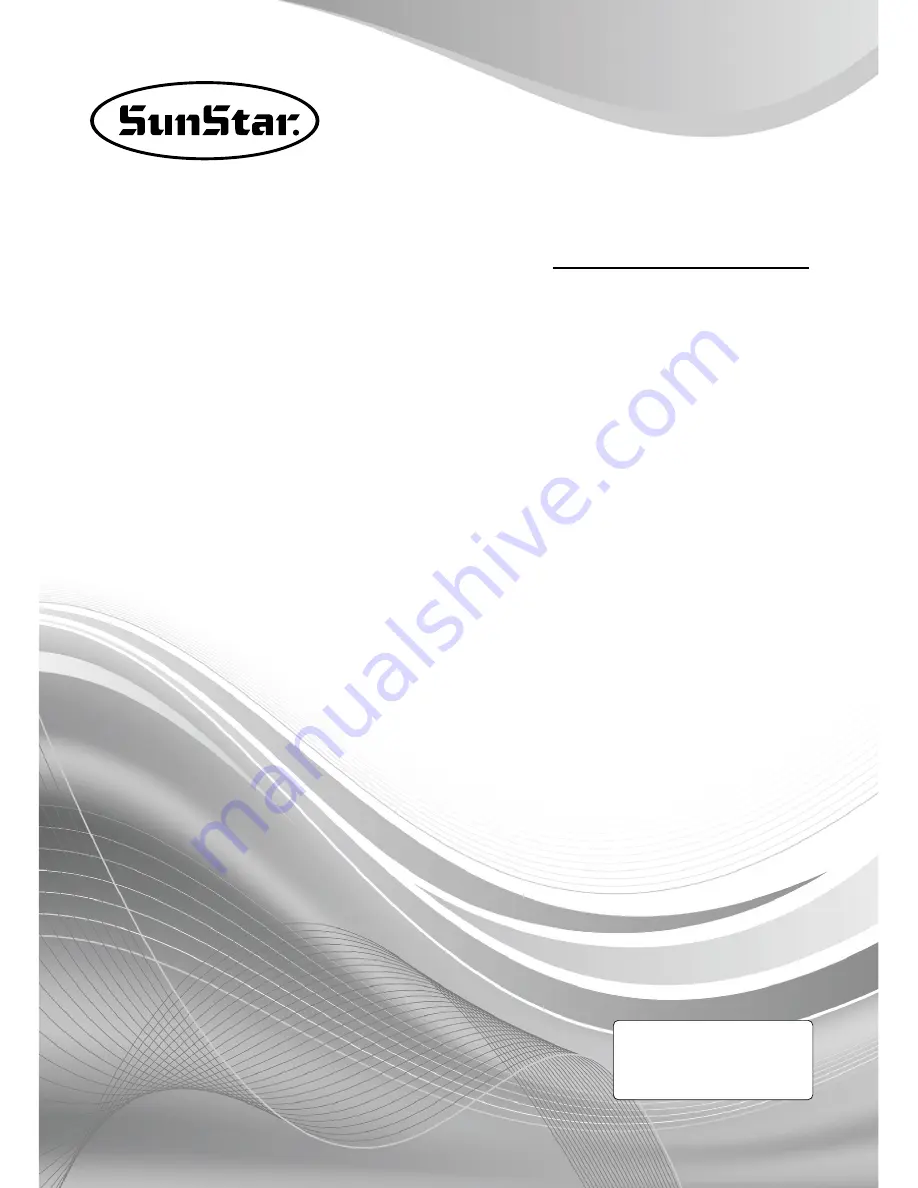
1) FOR AT MOST USE WITH EASINESS,
PLEASE CERTAINLY READ THIS MANUAL
BEFORE STARTING USE.
2) KEEP THIS MANUAL IN SAFE PLACE
FOR REFERENCE WHEN THE MACHINE
BREAKS DOWN.
M
MM
ME
E--1
12
20
02
20
01
1
USER
’
’
S MANUAL
KM-1170 SERIES
1-Needle, Unison Feed
Lock Stitch M/C
KM-1172 SERIES
2-Needle, Unison Feed
Lock Stitch M/C
R
S
Su
un
nS
Sttaarr C
CO
O..,, L
LT
TD
D..
Summary of Contents for KM-1170BLX
Page 2: ......
Page 14: ...14 Fig 4 5 Thread trimming ...