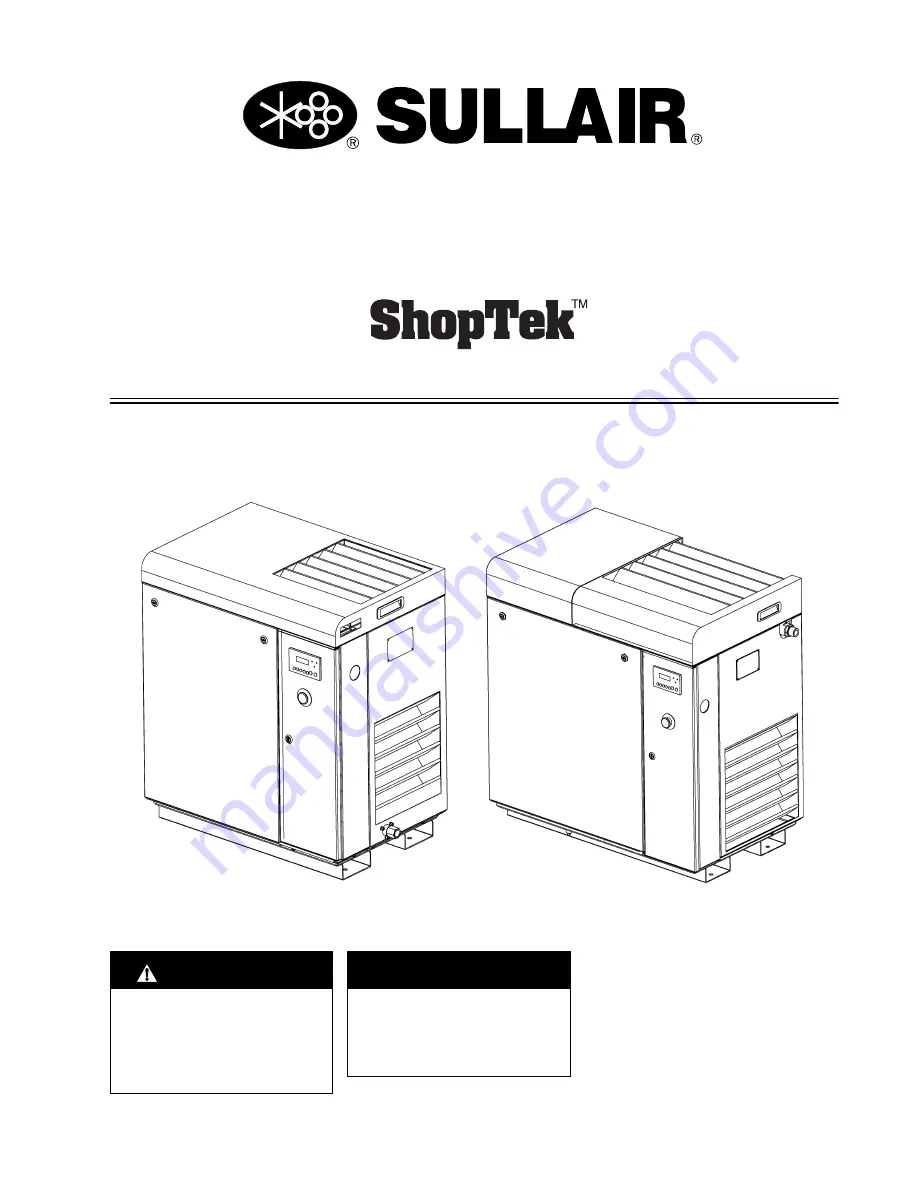
ST4, ST5, ST7, ST11, ST15
4 – 15 kW (5 – 20 hp)
Three-phase 60 Hz
PART NUMBER:
88292018-236 R00
The information in this manual is current as of its
publication date and applies to compressor models
indicated on this cover with
serial number
:
37216100224
and all subsequent serial numbers until next revision of
this manual or release of a replacement manual.
USER MANUAL
Publication date: 03/31/2017
Copyright © 2017 Sullair, LLC. All rights reserved.
WARRANTY NOTICE
Failure to follow the instructions
and procedures in this manual,
or misuse of this equipment, will
void
its warranty.
Subject to EAR, ECCN EAR99 and related export control restrictions.
SAFETY WARNING
Users are required to read the
entire User Manual before han-
dling or using the product. Keep
the User Manual in a safe place
for future reference.