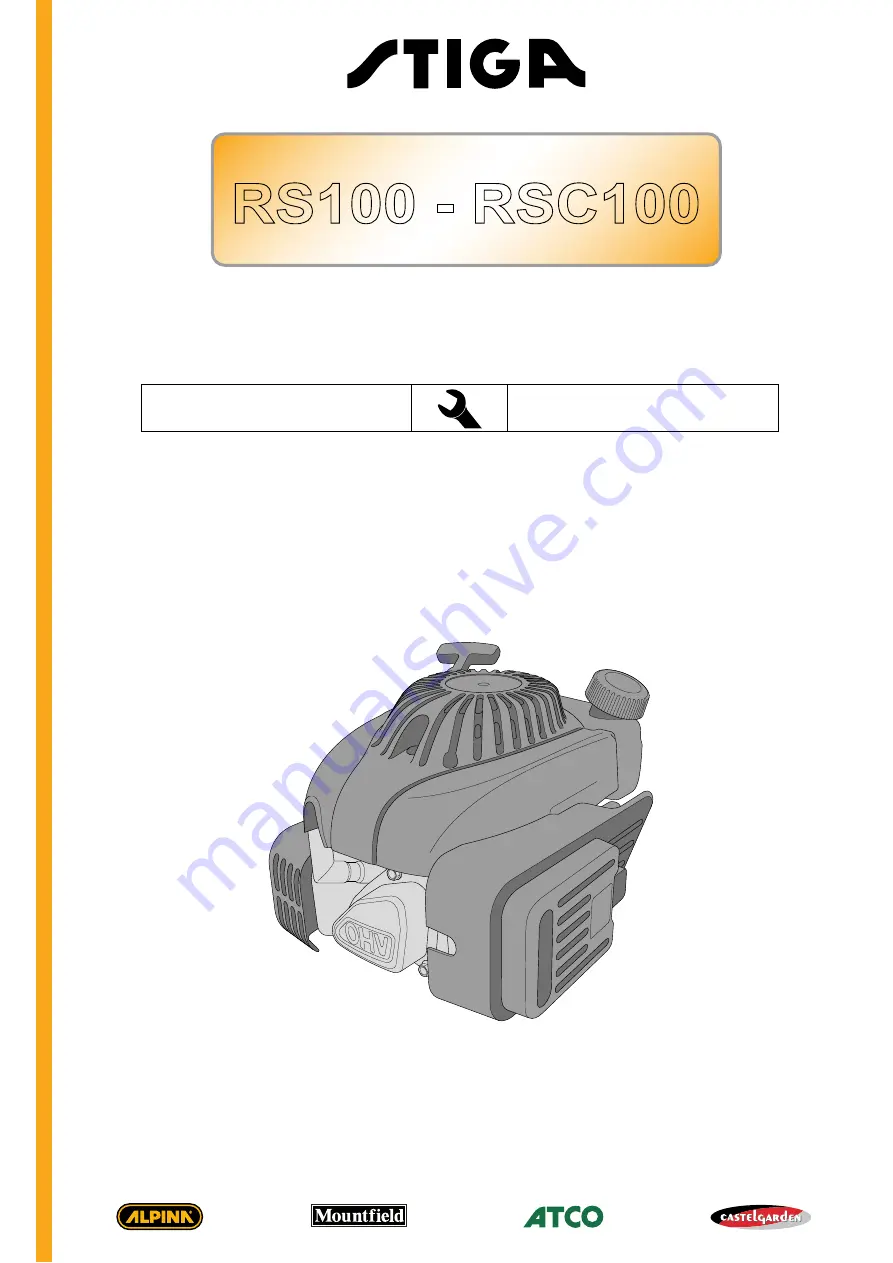
WORKSHOP MANUAL
WORKSHOP MANUAL
The manufacturer reserves the right to make all the necessary technical or commercial improvements to
its products, so there may be some differences between the series of engines and the contents of this
manual. However the basic specifications and different operating procedures will remain the same.
by STIGA - No use of the illustrations or duplication, reproduction or translation, even partial, of the texts
in this document may be made without explicit authorization.
IMPORTANT NOTICE :
The information contained herein is intended for Service Operations and professionals
only, able to competently perform the operations described herein, using the appropriate equipment in
order to safeguard se-curity and performance of the machine. The manufacturer is not liable for damages
or injuries arising from operations performed by individuals or inadequate facilities.
PRODUCTION YEAR
Rel. 0.0
2018
RS100 - RSC100
RS100 - RSC100