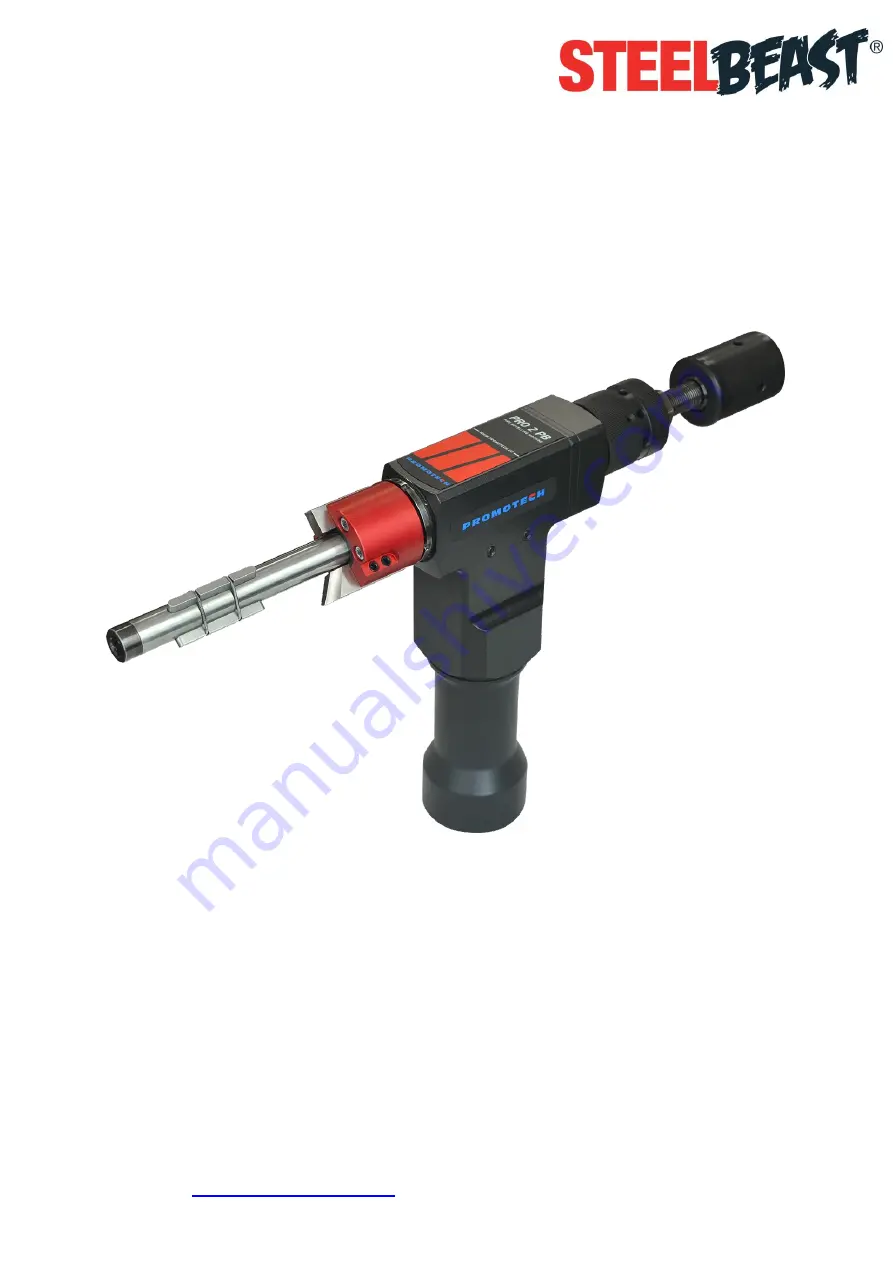
JEI Drilling & Cutting Solutions Ltd
Unit 21 Empire Business Park, Enterprise Way, Burnley, Lancashire,
BB12 6LT. Tel: 01706 229490 Fax: 01706 507347
Email: [email protected]
OPERATOR’S MANUAL
P
P
B
B
2
2
PIPE BEVELLING MACHINE