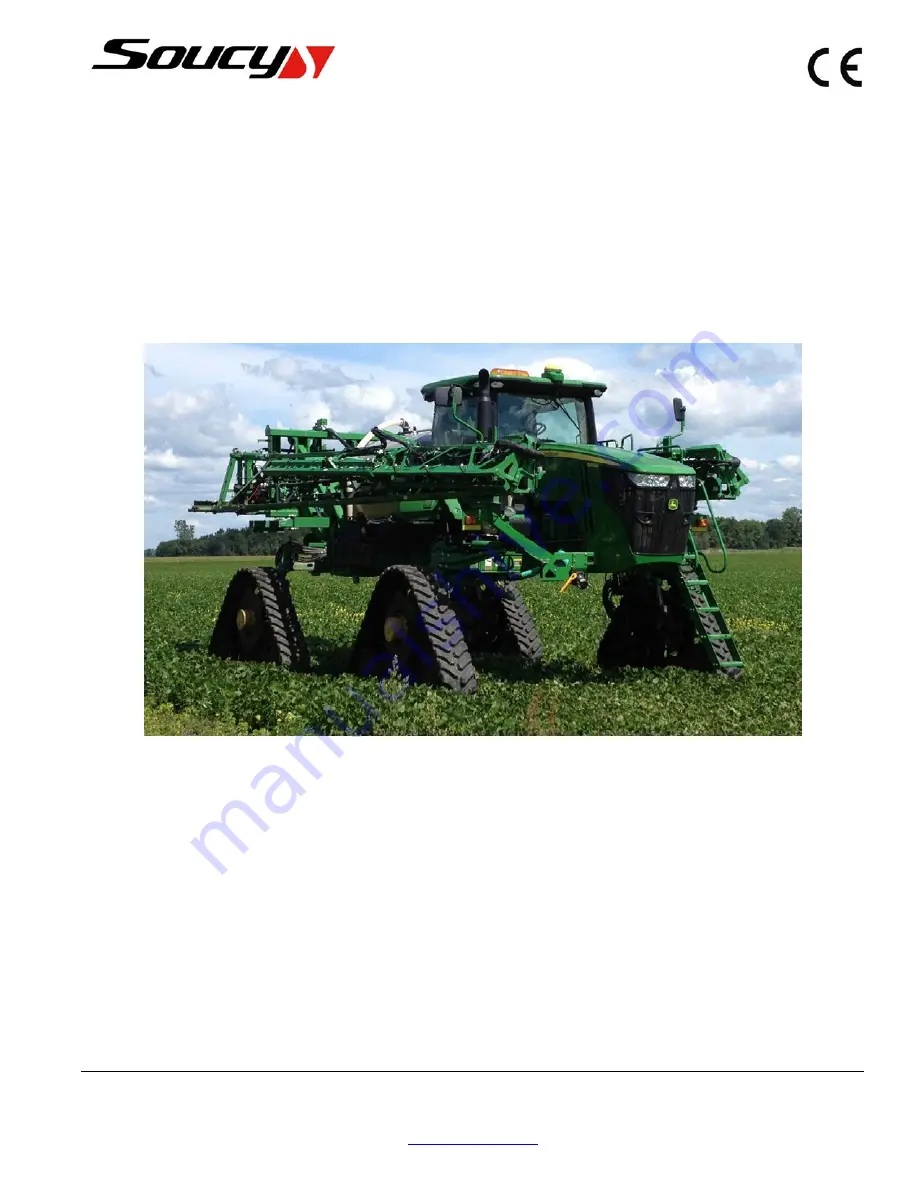
INSTALLATION, OPERATION AND MAINTENANCE GUIDE
FOR SOUCY TRACK SYSTEMS:
S-TECH 7016
installed on the following John Deere self-propelled sprayer models:
R4030 – R4038 – 4730 – 4830
A-8L0104-2-EN
Rev. B
May 2017
5450 St-Roch Street, P.O. Box 400 / Drummondville (Quebec) J2B 6W3 / CANADA
Toll free: 1 877 474-6665
Fax: 819 477-9423
Summary of Contents for S-TECH 7016
Page 8: ...Page Intentionally Left Blank INSTALLATION OPERATION AND MAINTENANCE GUIDE 4...
Page 15: ...INSTALLATION OPERATION AND MAINTENANCE GUIDE 11...
Page 16: ...Page Intentionally Left Blank INSTALLATION OPERATION AND MAINTENANCE GUIDE 12...
Page 18: ...Page Intentionally Left Blank INSTALLATION OPERATION AND MAINTENANCE GUIDE 14...
Page 56: ...Page Intentionally Left Blank INSTALLATION OPERATION AND MAINTENANCE GUIDE 52...
Page 66: ...Page Intentionally Left Blank INSTALLATION OPERATION AND MAINTENANCE GUIDE 62...
Page 70: ...Page Intentionally Left Blank INSTALLATION OPERATION AND MAINTENANCE GUIDE 66...
Page 74: ...Page Intentionally Left Blank INSTALLATION OPERATION AND MAINTENANCE GUIDE 70...
Page 78: ...Page Intentionally Left Blank INSTALLATION OPERATION AND MAINTENANCE GUIDE 74...
Page 83: ...INSTALLATION OPERATION AND MAINTENANCE GUIDE 79...