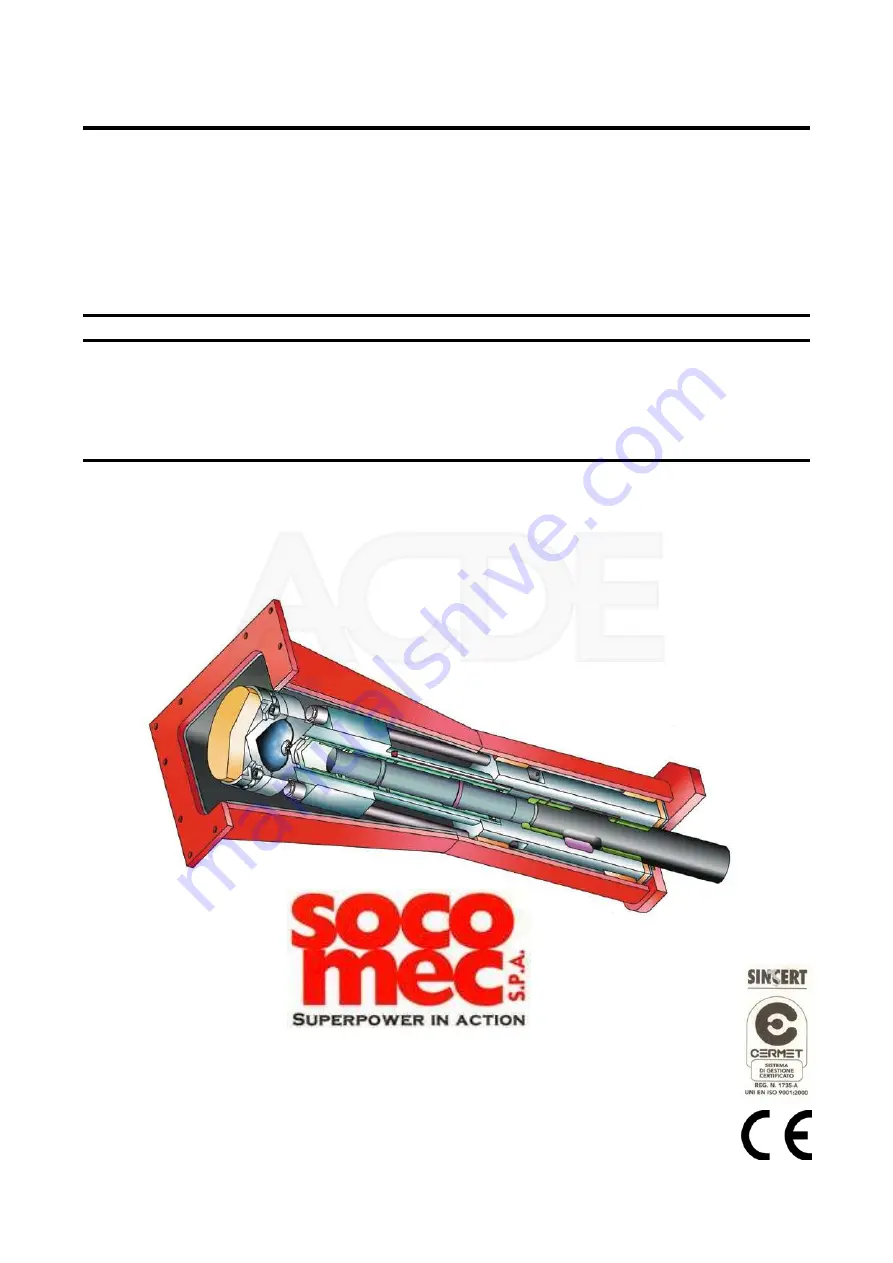
CATALOGUE
USE - MAINTENANCE
AND SPARE PARTS
Hydraulic Demolition Breaker
MDO 1600 TS
Before carrying out any operation with or on the machine, you must
read
carefully and understand each individual instruction written in this
manual
43014 Medesano (Parma) Italia - Strada Ferrari, 38
Phone +39 0525 - 420929 - Fax +39 0525 - 420375
http://www.socomecspa.com
E-mail: [email protected]
Nederland B.V.
Summary of Contents for MDO 1600 TS
Page 34: ...44 39 41 43 45 36 35 38 40 42 46 37 STROKE CHANGER 34 Page of 48 10 Nederland B V ...
Page 40: ...101 96 98 100 99 97 DISTRIBUTOR GROUP 40 Page of 48 13 Nederland B V ...
Page 42: ...107 104 106 101 105 109 108 103 102 ACCUMULATOR GROUP 42 Page of 48 14 Nederland B V ...
Page 46: ...129 132 125 134 127 128 126 133 130 133 131 GREASING SYSTEM 46 Page of 48 16 Nederland B V ...