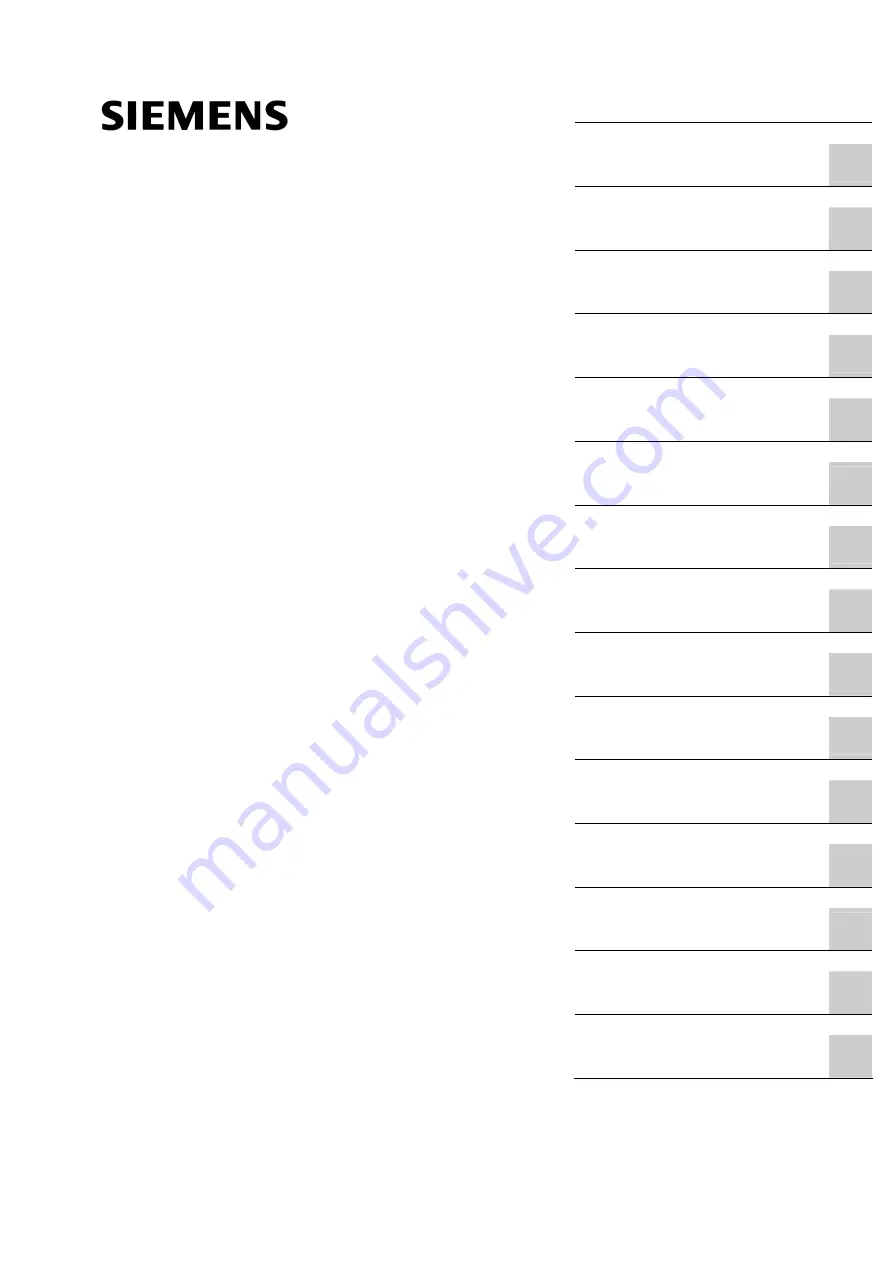
SINUMERIK SINUMERIK 802D sl Cylindrical grinding
______________
______________
______________
______________
______________
______________
______________
______________
______________
______________
______________
______________
______________
______________
______________
SINUMERIK
SINUMERIK 802D sl
Cylindrical grinding
Programming and Operating Manual
07/2009
6FC5398-4CP10-2BA0
Valid for
Control
software version
SINUMERIK 802D sl G/N
1.4