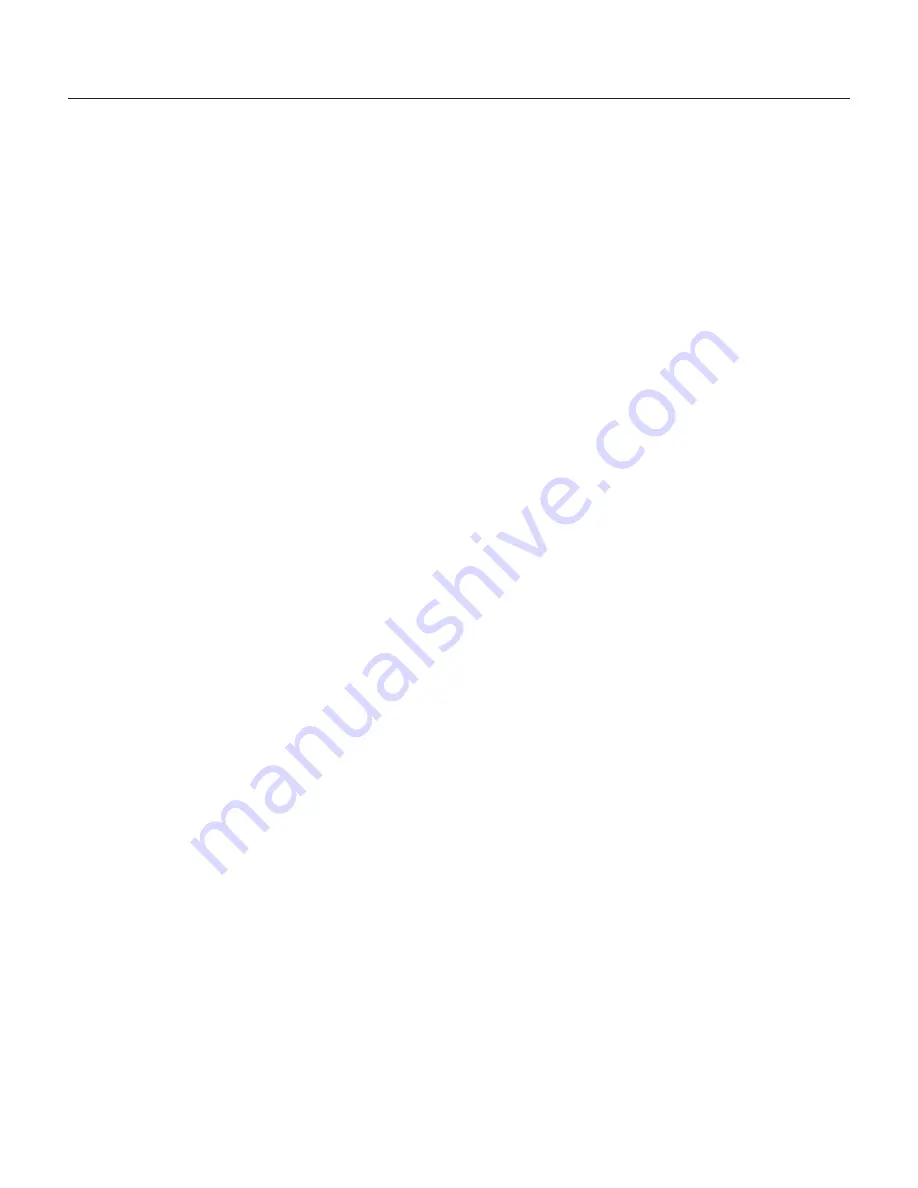
Introduction:
This manual covers the assembly, installation, start
up, operation and maintenance of the 2000 remote
low side cuber system.
A service parts list is located in the center of this manual.
Keep this manual for future reference. Note and follow Caution and Warning notices.
Eclipse
ä
2000
September 2003
Page 1
Table of Contents
Configuration: · · · · · · · · · · · · · · · · · Page 2
Technical Specifications · · · · · · · · · · · · Page 3
Model Number Locations · · · · · · · · · · · Page 4
Cabinet Drawings, Ice Making System · · · · Page 5
Cabinet Drawings, Compressor Package and
Condensers · · · · · · · · · · · · · · · · · · Page 6
Proper Combinations: · · · · · · · · · · · · · Page 7
Create the System· · · · · · · · · · · · · · · Page 8
System Examples · · · · · · · · · · · · · · · Page 9
System Examples · · · · · · · · · · · · · · · Page 10
Place Remote System · · · · · · · · · · · · · Page 11
System Location · · · · · · · · · · · · · · · · Page 12
Route Tubing · · · · · · · · · · · · · · · · · Page 13
Ice Making Section · · · · · · · · · · · · · · Page 14
Compressor Package · · · · · · · · · · · · · Page 15
Condensing Section Assembly · · · · · · · · Page 16
Condensing Section Assembly · · · · · · · · Page 17
Ice making section: · · · · · · · · · · · · · · Page 18
Bin Thermostat - Routing · · · · · · · · · · · Page 19
Bin Thermostat - Bracket & Bulb · · · · · · · Page 20
Water and Drain · · · · · · · · · · · · · · · · Page 21
Water and Drain · · · · · · · · · · · · · · · · Page 22
Ice Making Section Set Up · · · · · · · · · · Page 23
Coupling Connections: · · · · · · · · · · · · Page 24
Condensing Unit Connections · · · · · · · · · Page 25
Final Placement & Bin Thermostat Deployment Page 26
Controller Operation · · · · · · · · · · · · · · Page 27
Purge Adjustment · · · · · · · · · · · · · · · Page 28
Initial Start Up - 2000 Only · · · · · · · · · · Page 29
Startup: Three Phase Compressor (CP2086 Only)
· · · · · · · · · · · · · · · · · · · · · · · · · Page 30
System Operation:· · · · · · · · · · · · · · · Page 31
Refrigeration Details: · · · · · · · · · · · · · Page 32
Technicians Only: Freeze Cycle Sequence of Operation
· · · · · · · · · · · · · · · · · · · · · · · · · Page 33
Technicians Only: Harvest Cycle Sequence of Operation
· · · · · · · · · · · · · · · · · · · · · · · · · Page 34
Sanitation and Cleaning · · · · · · · · · · · · Page 35
Power and Water Interruptions · · · · · · · · Page 36
Other Maintenance · · · · · · · · · · · · · · Page 37
Water Distributors · · · · · · · · · · · · · · · Page 38
Ice Sensors · · · · · · · · · · · · · · · · · · Page 39
Water Level Sensor Maintenance · · · · · · · Page 40
Service Diagnosis · · · · · · · · · · · · · · · Page 41
Service Diagnosis · · · · · · · · · · · · · · · Page 42
Service Diagnosis · · · · · · · · · · · · · · · Page 43
Controller Features & Last Error Recall · · · · Page 44
Operational Characteristics 2000 lb system · · Page 45
Refrigeration System Service · · · · · · · · · Page 46