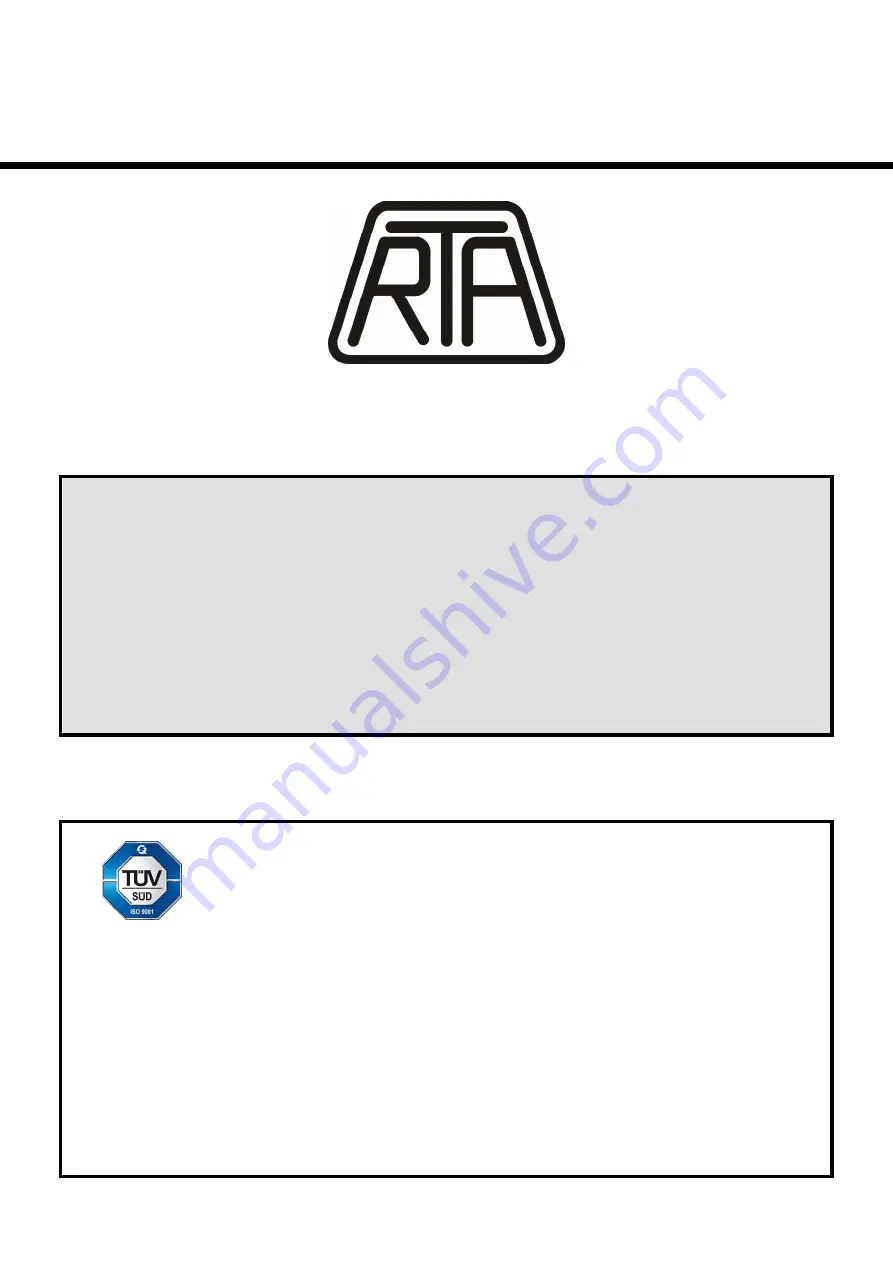
R.T.A. s.r.l. – XPETME05 – 11/20
MOTION CONTROL SYSTEMS
X-PLUS ET B4/S4
SERIES
STEPPING MOTOR DRIVES
INSTRUCTION MANUAL
R.T.A. s.r.l.
Via E. Mattei – Frazione DIVISA
27020 MARCIGNAGO (PV)
Tel. +39.0382.929.855 - Fax +39.0382.929.150
Internet:
http://www.rta.it
- e-mail:
R.T.A.
DEUTSCHLAND GmbH
Bublitzer Straße, 34
40599 DÜSSELDORF (Germany)
Tel. +49.211.749.668.60-Fax +49.211.749.668.66
Internet:
http://www.rta-deutschland.de
e-mail:
R.T.A. IBERICA
MOTION CONTROL SYSTEMS S.L.
C/Generalitat 22, 1° 3°
08850 GAVA – BARCELONA (Spain)
Tel. +34.936.388.805-Fax +34.936.334.595
Internet:
http://www.rta-iberica.es
e-mail: