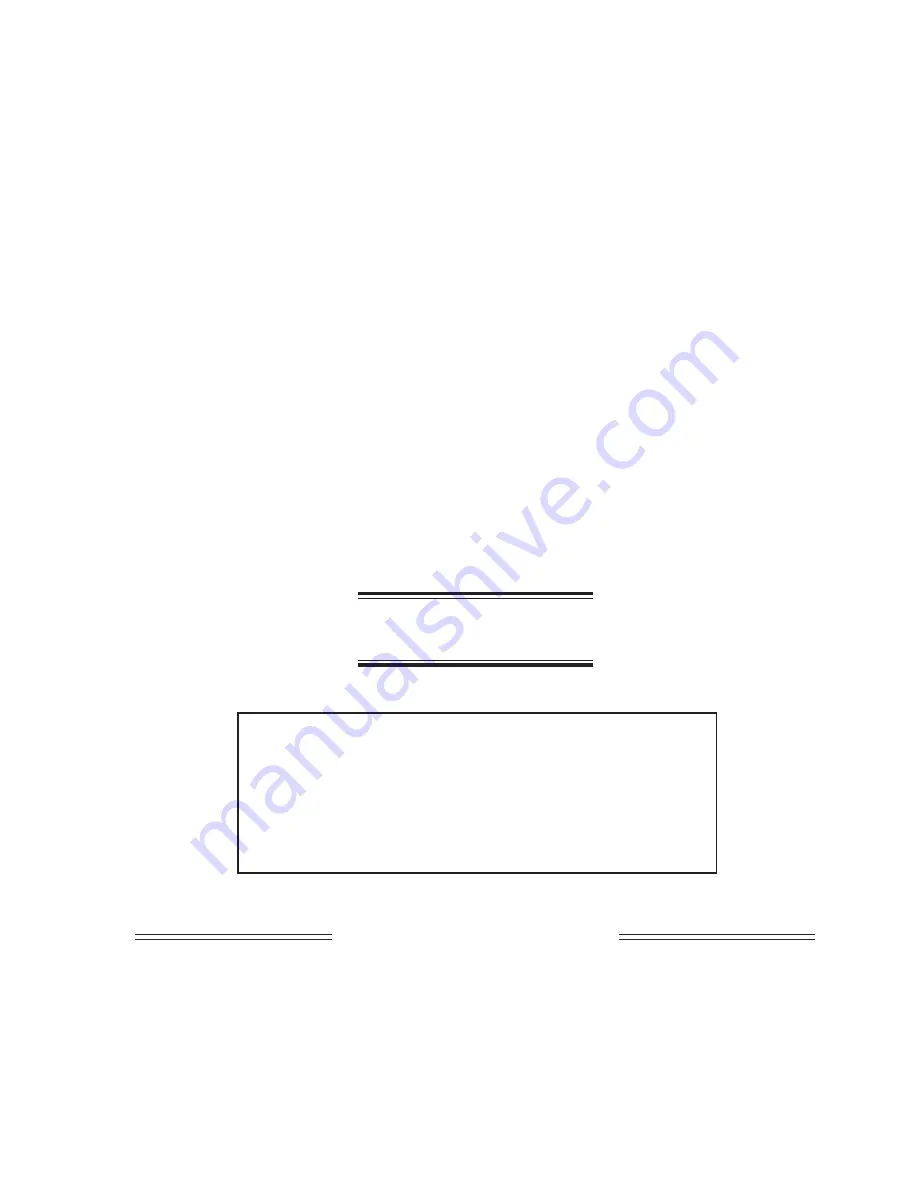
RISO INTERNATIONAL GROUP
RISO KAGAKU CORPORATION (JAPAN)
RISO DEUTSCHLAND GMBH (GERMANY)
RISO, INC. (U.S.A.)
RISO FRANCE (FRANCE)
RISO EUROPE LIMITED (U.K.)
RISO IBERICA (SPAIN)
RISO HONG KONG (HONG KONG)
RISO CANADA (CANADA)
RISO UK (U.K.)
ZHUHAI RISO TECHNOLOGY (CHINA)
RISO THAILAND LIMITED (THAILAND)
RISO AFRICA (SOUTH AFRICA)
RISOGRAPH ITALIA (ITALY)
Copyright : 2002 Riso Kagaku Corporation
All Rights Reserved. This Technical Manual was prepared and
written for the exclusive use of RISO International Group Certified
Dealers. Reproduction and/or transmittal of this material in any form
or by any means, including photocopying or recording of the
information is strictly prohibited without the consent of a member of
RISO International Group.
VERSION
FEBRUARY 2002
V8000
SERIES
TECHNICAL MANUAL
Содержание V8000 Series
Страница 30: ... 1 19 CHAPTER 1 MAINTENANCE 4 Removing Exterior Covers Rear cover Rear cover P0112 ...
Страница 31: ... 1 20 CHAPTER 1 MAINTENANCE Front doors L R Front door R Front door L P0113 P0114 P0115 P0116 ...
Страница 42: ... 2 6 CHAPTER 2 MACHINE OVERVIEW MEMO ...
Страница 54: ... 3 12 CHAPTER 3 MAIN DRIVE SECTION MEMO ...
Страница 78: ... 4 24 CHAPTER 4 FIRST PAPER FEED SECTION MEMO ...
Страница 92: ... 5 14 CHAPTER 5 SECOND PAPER FEED SECTION MEMO ...
Страница 105: ... 6 13 CHAPTER 6 PAPER DRUM SECTION Gripper shaft unit Gripper collar P0630 P0631 REAR Gripper shaft unit FRONT ...
Страница 112: ... 6 20 CHAPTER 6 PAPER DRUM SECTION MEMO ...
Страница 133: ... 8 7 CHAPTER 8 PRINT DRUM SECTION Hanger E Clamp plate base ass y P08006 P08007 Screen ass y Hanger TA ...
Страница 141: ... 8 15 CHAPTER 8 PRINT DRUM SECTION Pressure control motor ass y P08028 P08029 Pressure control motor ass y Connector ...
Страница 170: ... 8 44 CHAPTER 8 PRINT DRUM SECTION MEMO ...
Страница 178: ... 9 8 CHAPTER 9 VERTICAL PRINT POSITION SECTION MEMO ...
Страница 206: ... 11 20 CHAPTER 11 MASTER DISPOSAL SECTION MEMO ...
Страница 209: ... 12 3 CHAPTER 12 FB ORIGINAL SCANNING SECTION MEMO ...
Страница 263: ... 15 1 CHAPTER 15 TIMING CHARTS Contents This chapter is not completed ...
Страница 333: ... 18 4 CHAPTER 18 FUNCTIONS MEMO ...
Страница 355: ... 20 18 CHAPTER 20 PRINTED CIRCUIT BOARDS MEMO ...