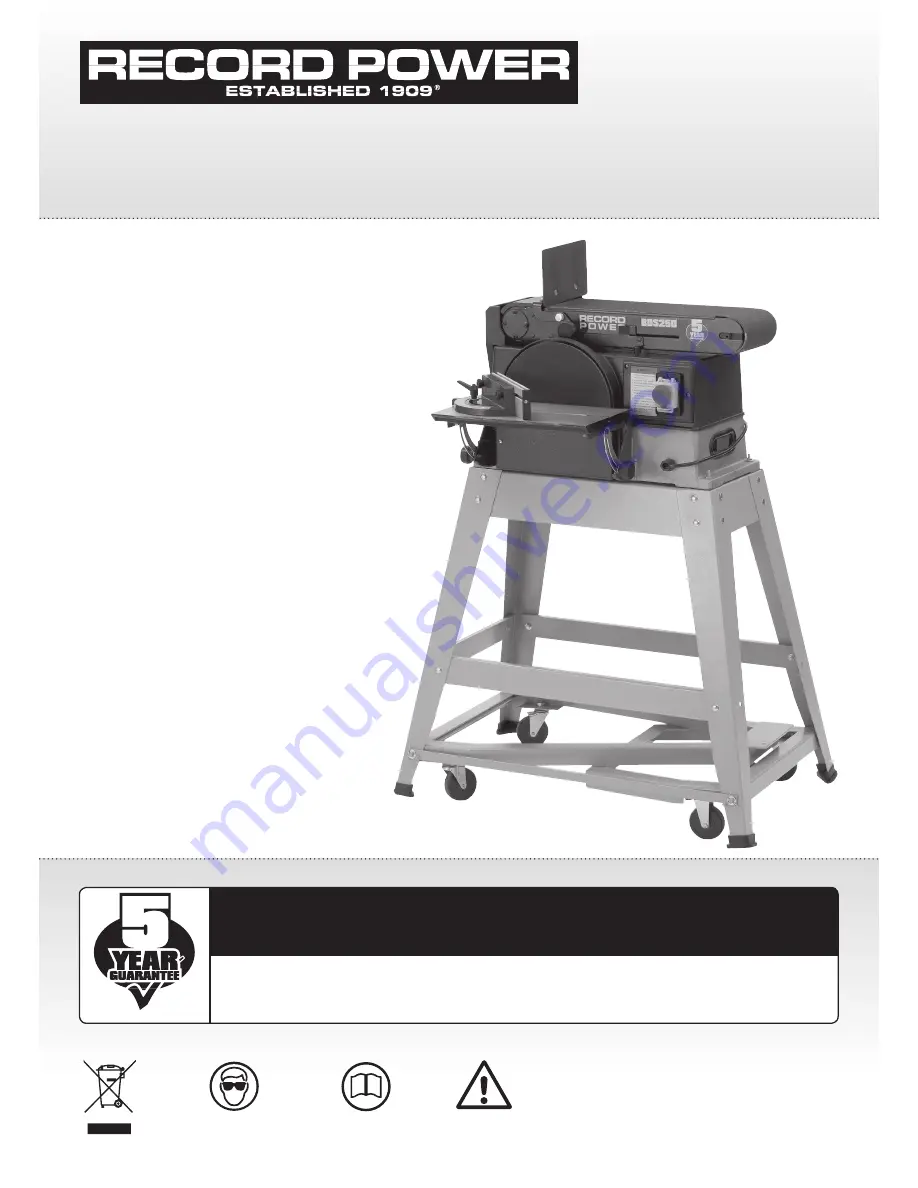
Original Instruction Manual
BDS250
10" x 6"
Belt & Disc Sander
Always wear safety glasses when
using woodworking equipment.
Always read the instructions
provided before using
woodworking equipment.
i
Kg
Version 3.0
January 2013
Show with optional stand and wheel kit.
To register this product please visit
www.recordpower.info
It is important to register your product as soon as possible in order to receive efficient after sales
support and be entitled to the full
5 year guarantee
. Your statutory rights are not affected.
Please see back cover for contact details.
Important
For your safety read instructions carefully
before assembling or using this product.
Save this manual for future reference.
i
Kg