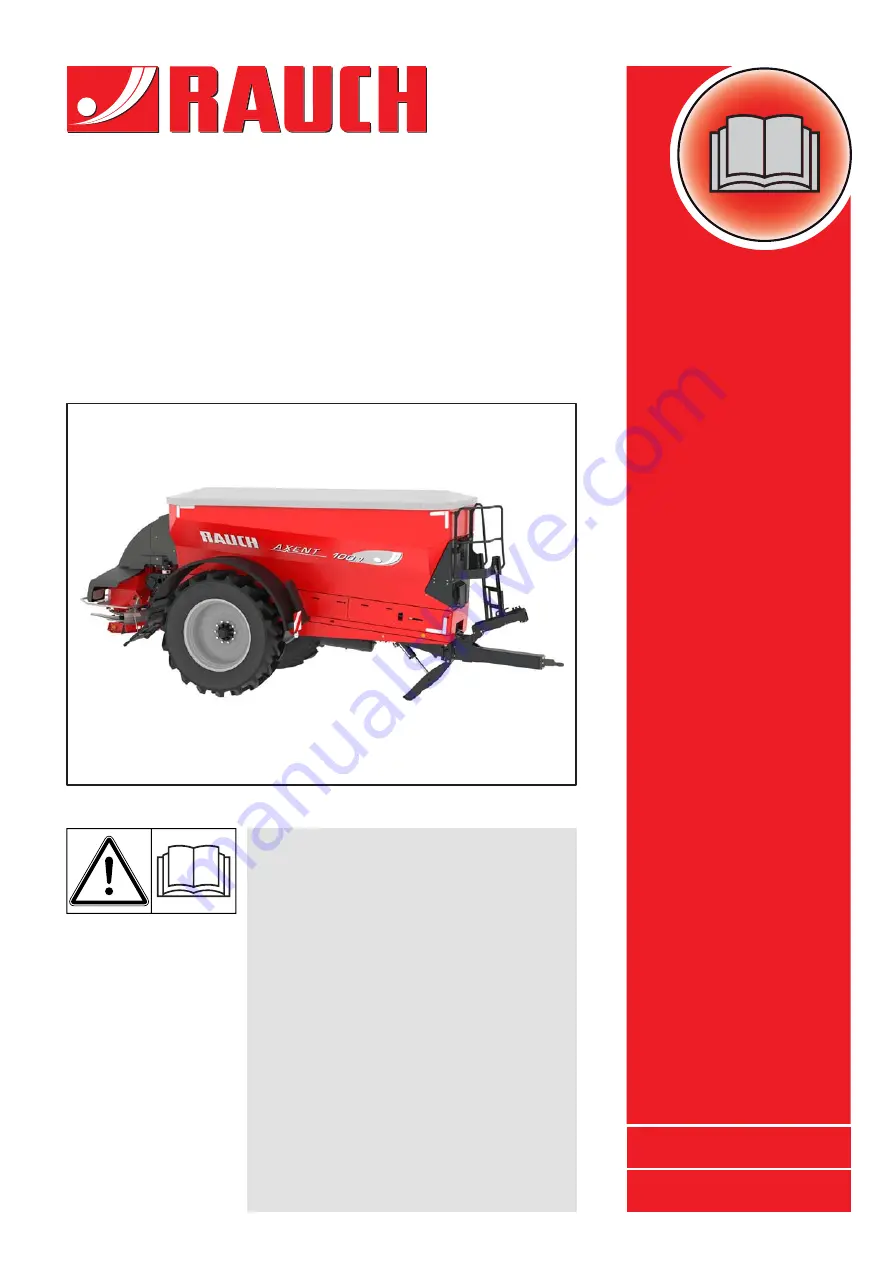
OPERATOR'S MANUAL
AXENT
5901645-
e
-en-0219
Please read carefully
before using the
machine.
Keep for future reference.
This instruction manual/assembly
instruction is to be considered as part of
the machine. Suppliers of new and sec-
ond-hand machines are required to
document in writing that the instruc-
tion manual/assembly instruction was
delivered with the machine and
handed over to the customer.
Original manual
Summary of Contents for AXENT Series
Page 8: ...Intended use 1 2...
Page 32: ...Safety 3 26...
Page 54: ...Technical data 4 48...
Page 56: ...Transport without tractor 5 50...
Page 122: ...Spreading operation 7 116...
Page 124: ...Faults and possible causes 8 118...
Page 162: ...General maintenance and servicing 9 156...
Page 168: ...Index D...
Page 170: ......