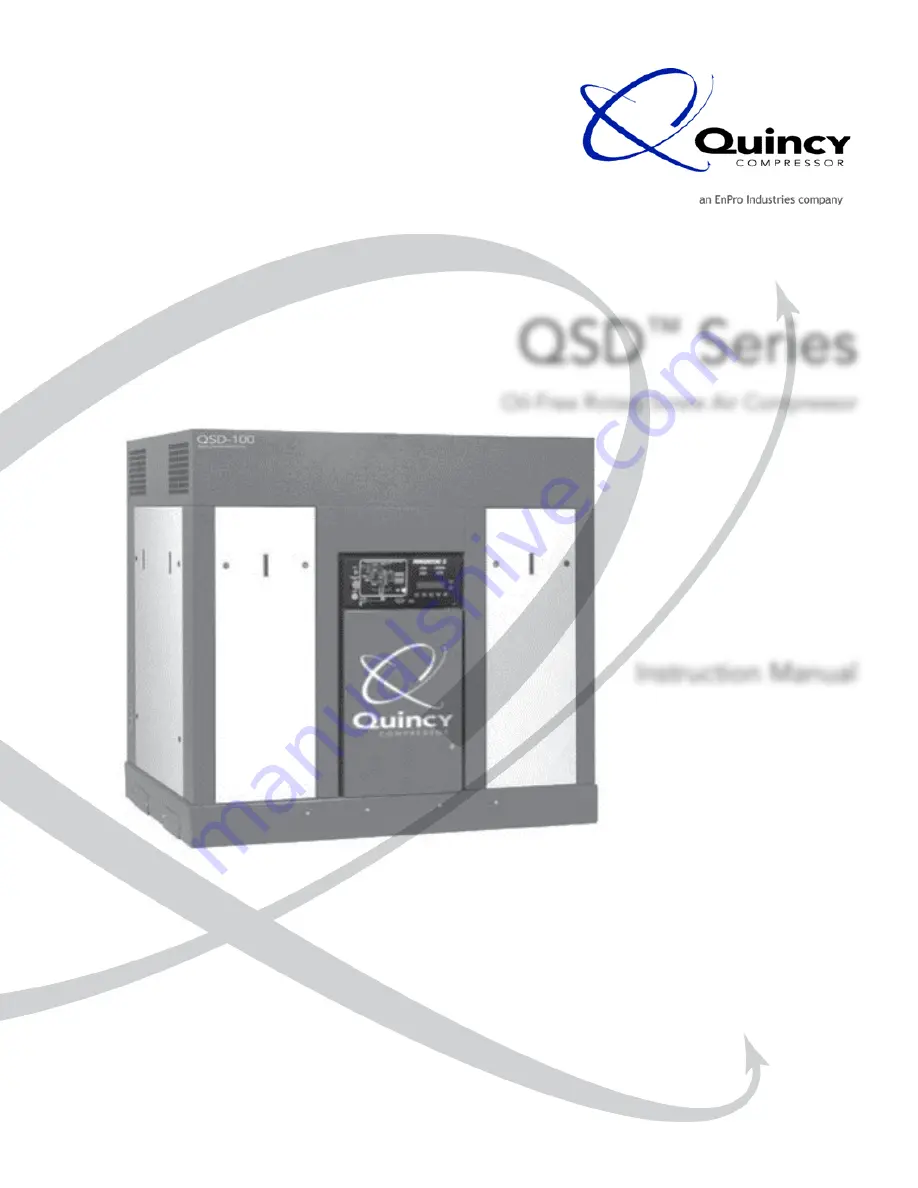
QSD
™
Series
Oil-Free Rotary Screw Air Compressor
Instruction Manual
This manual contains important safety information and should be made available to
all personnel who operate and/or maintain this product. Carefully read this manual
before attempting to operate or perform maintenance on this equipment.
Manual No. 65040-AB
January 2001 Edition
Summary of Contents for QSD 65040-AB
Page 2: ......
Page 10: ...Section II Description 8 Quincy Compressor QSD MODEL IDENTIFICATION...
Page 33: ...Section VII Service Adjustments Quincy Compressor QSD 31 THIS PAGE INTENTIONALLY LEFT BLANK...
Page 83: ...Notes Quincy Compressor QSD 81...
Page 84: ...Notes 82 Quincy Compressor QSD...
Page 85: ......