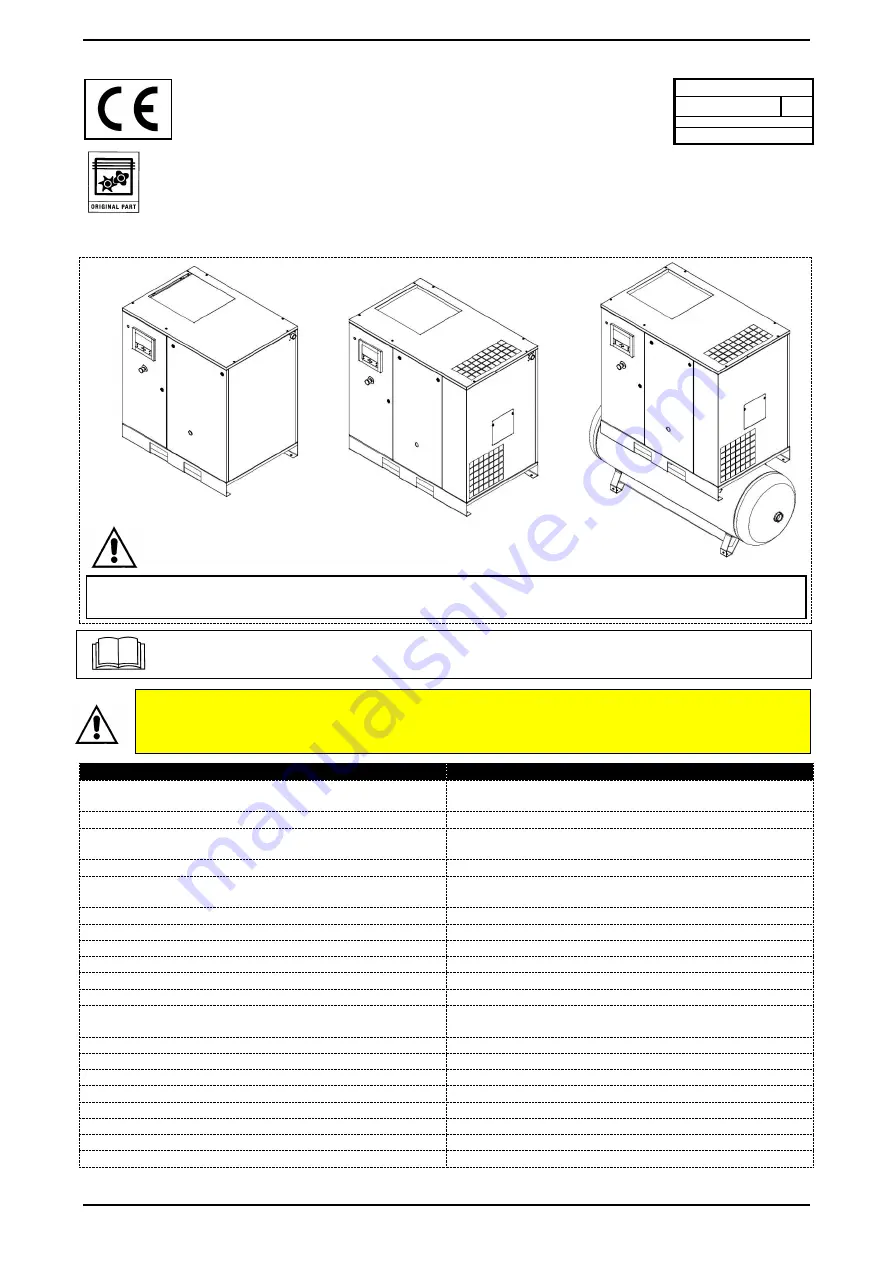
ENGLISH
.
Cod. 9828093300 00 - Vers. 04/2019 - 1
USE & MAINTENANCE MANUAL
QUIET ROTARY SCREW AIR COMPRESSORS
HP 20 - 25 - 30 - 35
KW 15
–
18.5 - 22 - 26
HP 20 - 25 - 30 - 35 (
IVR
)
KW 15
–
18.5 - 22 - 26(
IVR
)
(IVR
): Variable speed compressors (INVERTER)
ATTENTION: THE CAPACITORS INSIDE THE INVERTER MAY REMAIN LIVE FOR 15 MINUTES AFTER THE MACHINE HAS BEEN
DISCONNECTED FROM THE MAINS POWER.
ACTING ON THE INVERTER BEFORE 15 MINUTES HAVE PASSED MAY ENTAIL THE RISK OF ELECTROCUTION AND DEATH.
CONTENTS
PART A: NOTICES FOR THE USER
PART B: NOTICES RESERVED FOR PROFESSIONALLY QUALIFIED
PERSONNEL
1.0
GENERAL CHARACTERISTICS
20.0
START-UP
2.0
INTENDED USE
21.0
GENERAL ROUTINE MAINTENANCE REQUIRES TRAINED
PERSONNEL
3.0
OPERATING PRINCIPLE
22.0
OIL REPLACEMENT
4.0
GENERAL SAFETY REGULATIONS
23.0
OIL FILTER AND OIL SEPARATOR FILTER
REPLACEMENT
5.0
DESCRIPTION OF HAZARD SYMBOLS
24.0
MOTOR BEARING GREASING (IVR ONLY)
6.0
HAZARDOUS AREAS
25.0
OLEO-PNEUMATIC DIAGRAM
7.0
SAFETY DEVICES
26.0
DRYER CALIBRATIONS
8.0
POSITION OF LABELS
27.0
VARIABLE SPEED (IVR)
9.0
COMPRESSOR ROOM
10.0
TRANSPORT & HANDLING
11.0
UNPACKING
ATTENTION: A COPY OF THE WIRING DIAGRAMS IS INCLUDED IN
THE ELECTRICAL CABINET OF THE COMPRESSOR
12.0
INSTALLATION
13.0
OVERALL DIMENSIONS AND TECHNICAL DATA
14.0
ILLUSTRATION OF MACHINE
15.0
ROUTINE MAINTENANCE BY THE USER
16.0
STORAGE
17.0
DISMANTLING THE AIR COMPRESSOR
18.0
SPARE PARTS LIST FOR ROUTINE MAINTENANCE
19.0
TROUBLESHOOTING AND IMMEDIATE ACTIONS
Code
9828093300 00
Vers. 04/2019
READ THIS MANUAL CAREFULLY BEFORE PERFORMING ANY OPERATIONS ON THE AIR COMPRESSOR.
THIS MACHINE IS DESIGNED TO BE CONNECTED TO TWO DIFFERENT SOURCES OF ELECTRICAL POWER: THREE-PHASE
POWER SOURCE FOR COMPRESSOR, SINGLE PHASE POWER SOURCE FOR DRYER