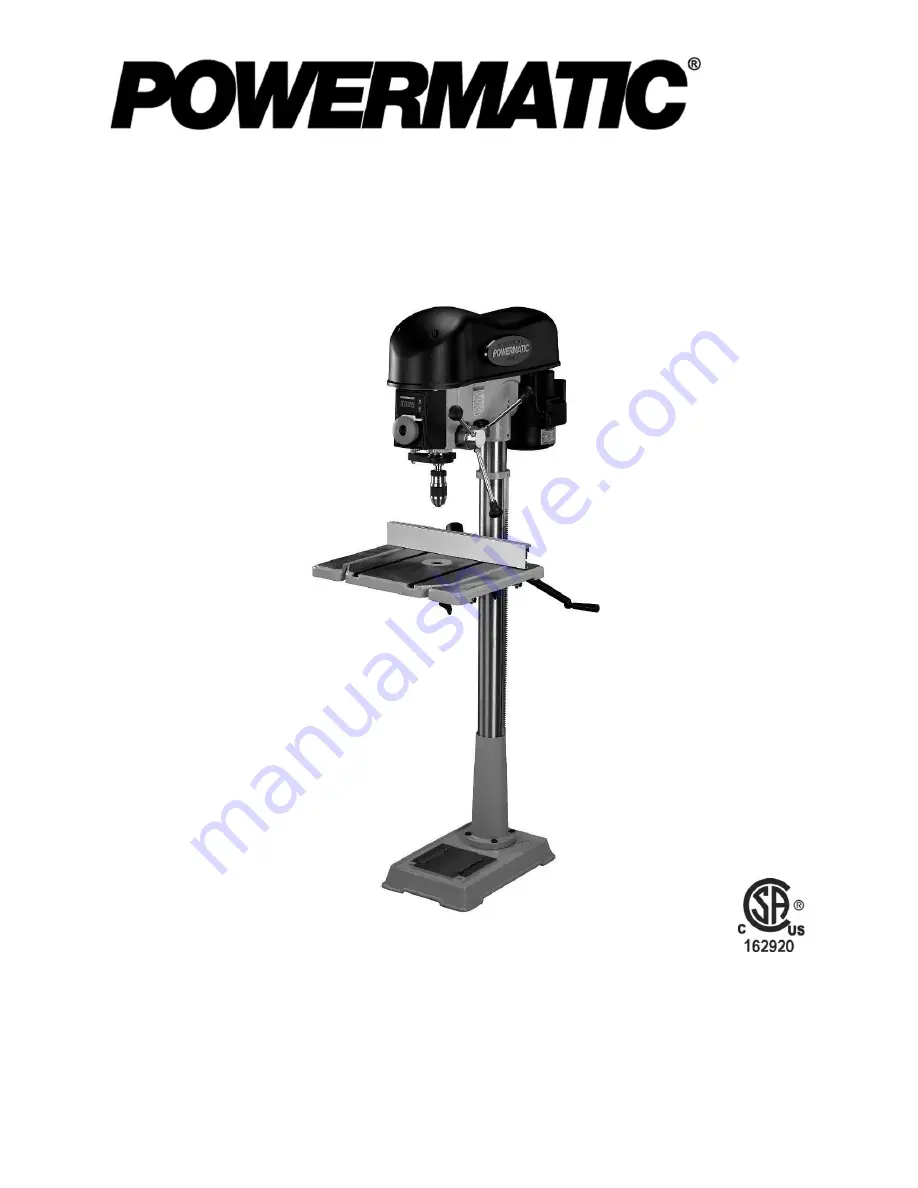
Operating Instructions and Parts Manual
18-inch Variable Speed Drill Press
Model 2800
for serial # 7040001 and up
WALTER MEIER (Manufacturing) Inc.
427 New Sanford Road
LaVergne, Tennessee 37086
Part No. M-1792800
Ph.: 800-274-6848
Revision C1 04/2010
www.powermatic.com
Copyright © 2010 Walter Meier (Manufacturing) Inc.
Summary of Contents for 2800
Page 20: ...20 Model 2800 Drill Press ...
Page 25: ...25 Electrical Connections ...
Page 26: ...26 Electrical Connections ...
Page 27: ...27 ...