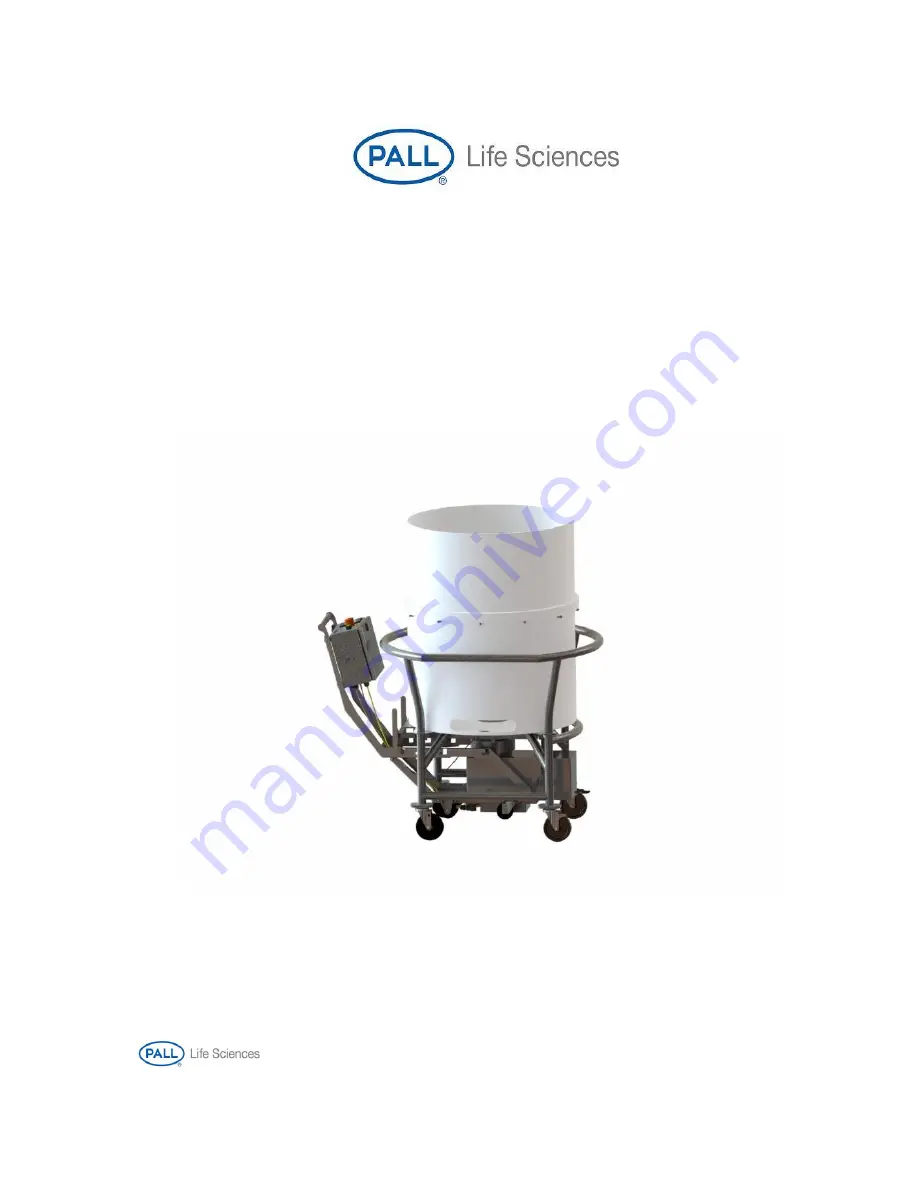
Pall Life Sciences.
USA:
Port Washington, NY, USA 1 800 717 7255 toll free (USA),+1 516 484 5400 phone
,
[email protected] e-mail
, www.pall.com
.
Europe: Fribourg, Switz41 (0)26 350 53 00 phone,
[email protected] e-mail. Asia-Pacific : +65 6389 6500 phone, [email protected] e-mail
© 2012, Pall Corporation. Pall, Allegro, Kleenpak, Stax and the Allegro Design are trademarks of Pall Corporation. ®
indicates a trademark registered in the USA and TM indicates a common law trademark.
Filtration.Separation.Solution
is a service mark of Pall Corporation.
LevMixer
®
Single-Use Mixing System
OPERATOR MANUAL
Models DB-300, DB-300C
USD 3184