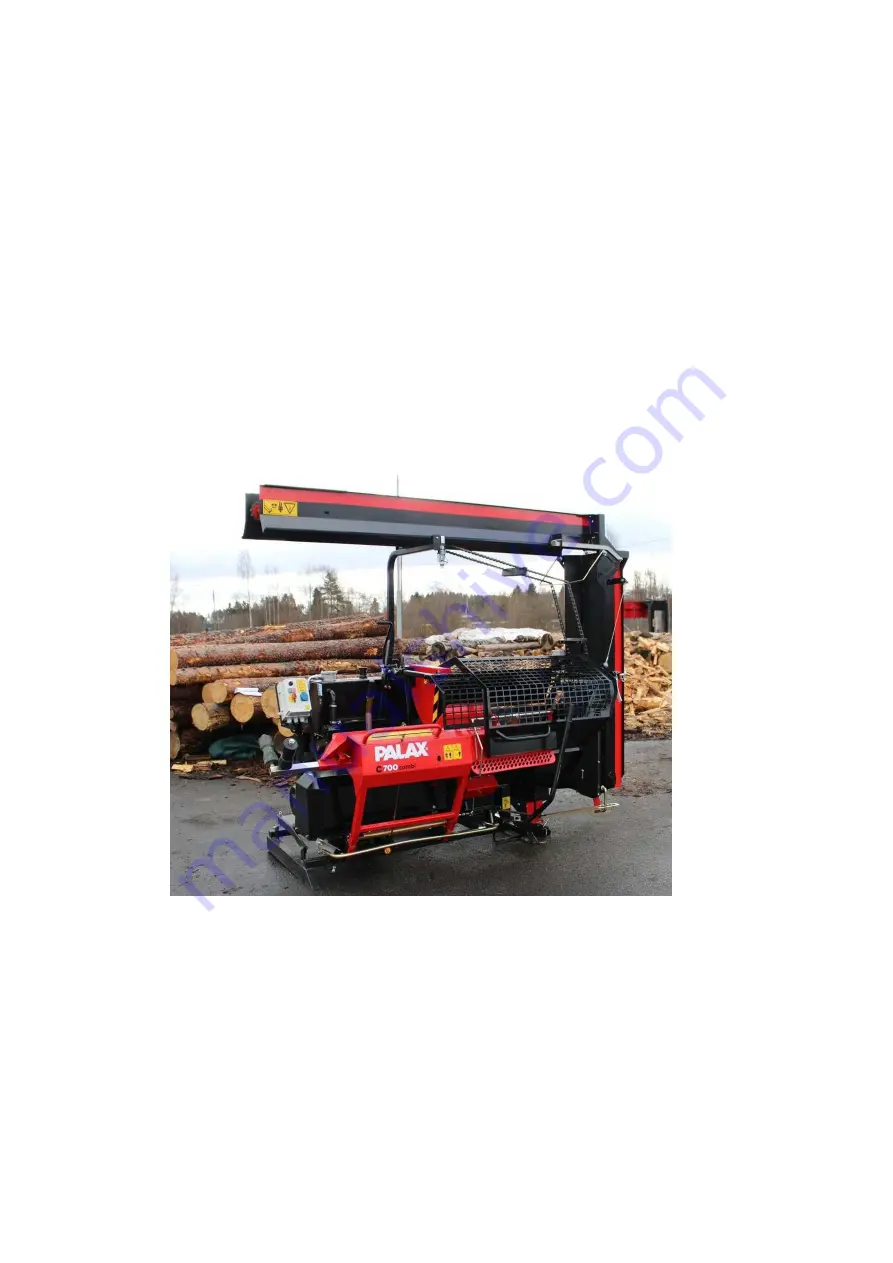
1-2018
translation
OPERATING INSTRUCTIONS
PALAX C700
COMBI
powered by tractor
powered by electricity
powered by combustion engine
swinging conveyor of 4.3-metres with hydraulic
motor
SERIAL NUMBER _______________________
YEAR OF MANUFACTURE
_______________________
PALAX
LAHDENTIE 9
FI-61400 YLISTARO, FINLAND
TEL. +358 6 4745100
WWW.PALAX.FI
Summary of Contents for C700 COMBI
Page 38: ...34 translation 10 ELECTRIC DIAGRAMS ...
Page 39: ...35 translation ...