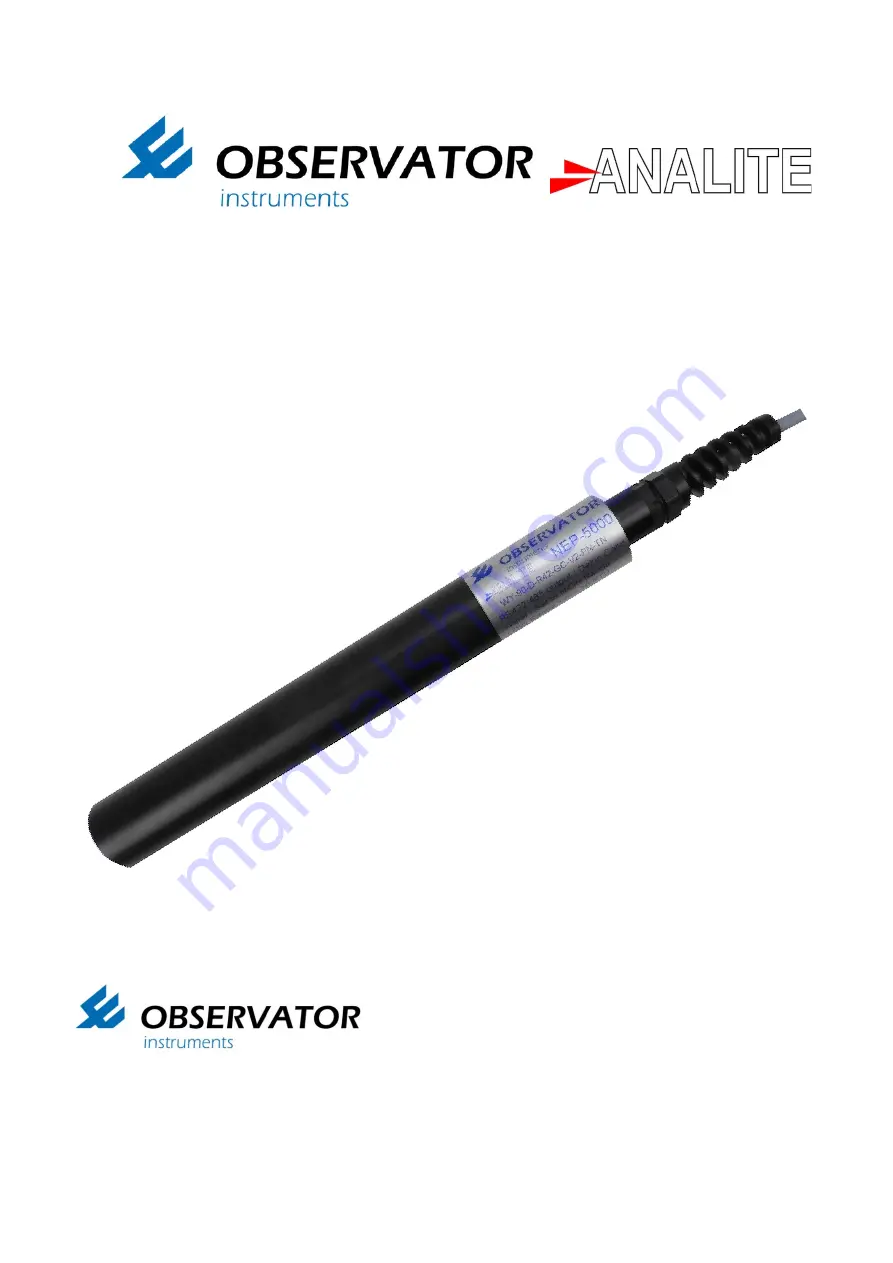
Observator Instruments
Copyright 2019
©
Page 1
Nep-5000 General Information
Manual
Version 2019-08-29 – August 2019
Author: Observator Instruments
NEP-5000 MANUAL
ABN 56 007 283 963
8-10 Keith Campbell Court, PO Box 9039
Scoresby, VIC 3179 AUSTRALIA
Tel: +61 3 8706 5000, Fax: +61 3 8706 5049
Email: [email protected]
Web: www.observator.com