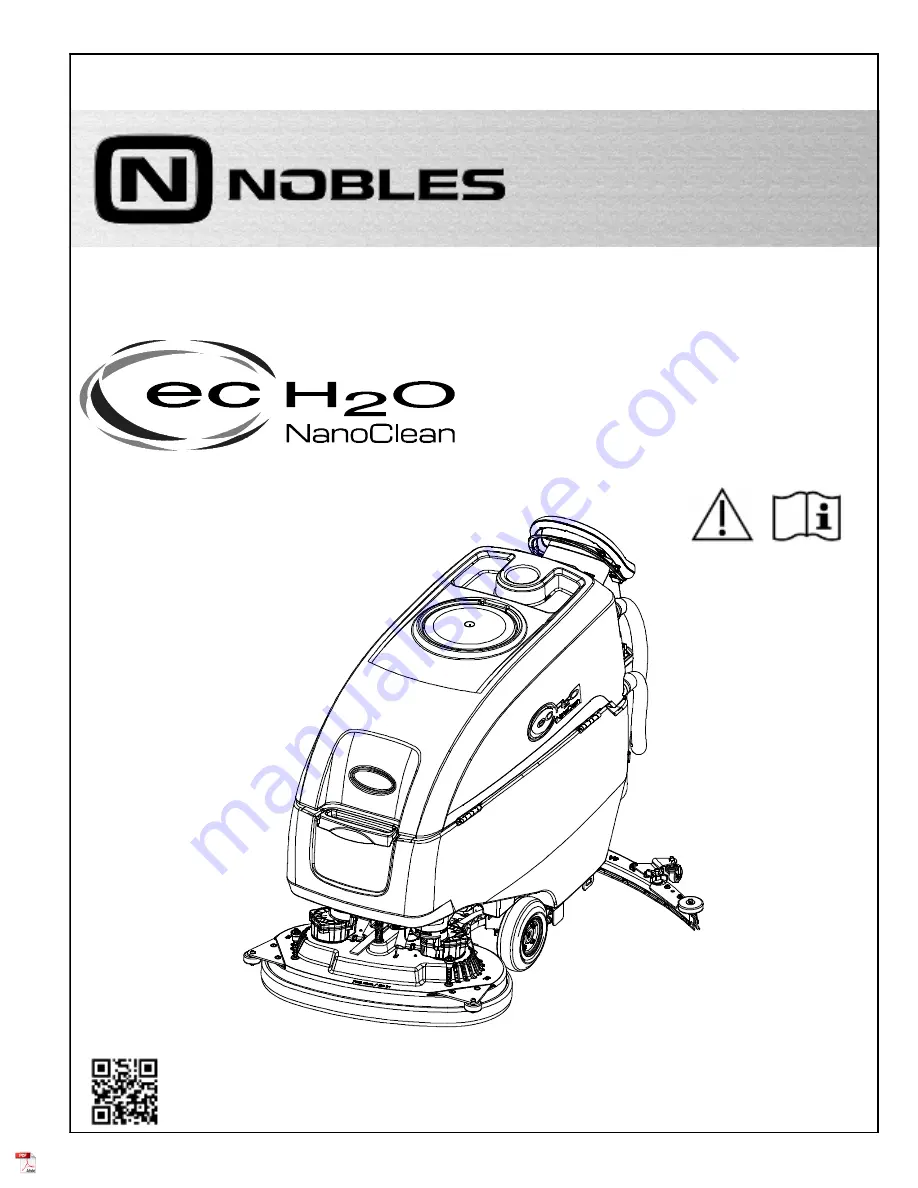
ENGLISH
For the latest Parts manuals and other
language Operator manuals, visit:
www.nobles.com/manuals
®
9015513
Rev. 03 (09-2020)
WALK-BEHIND FLOOR SCRUBBER
*9015513*
®
OPERATOR MANUAL
SPEED SCRUB 500
R
Tennant
True
®
Parts
IRIS
®
a Tennant Technology
Insta-Fit
™ Adapter
Smart-Fill
™ Automatic Battery Watering