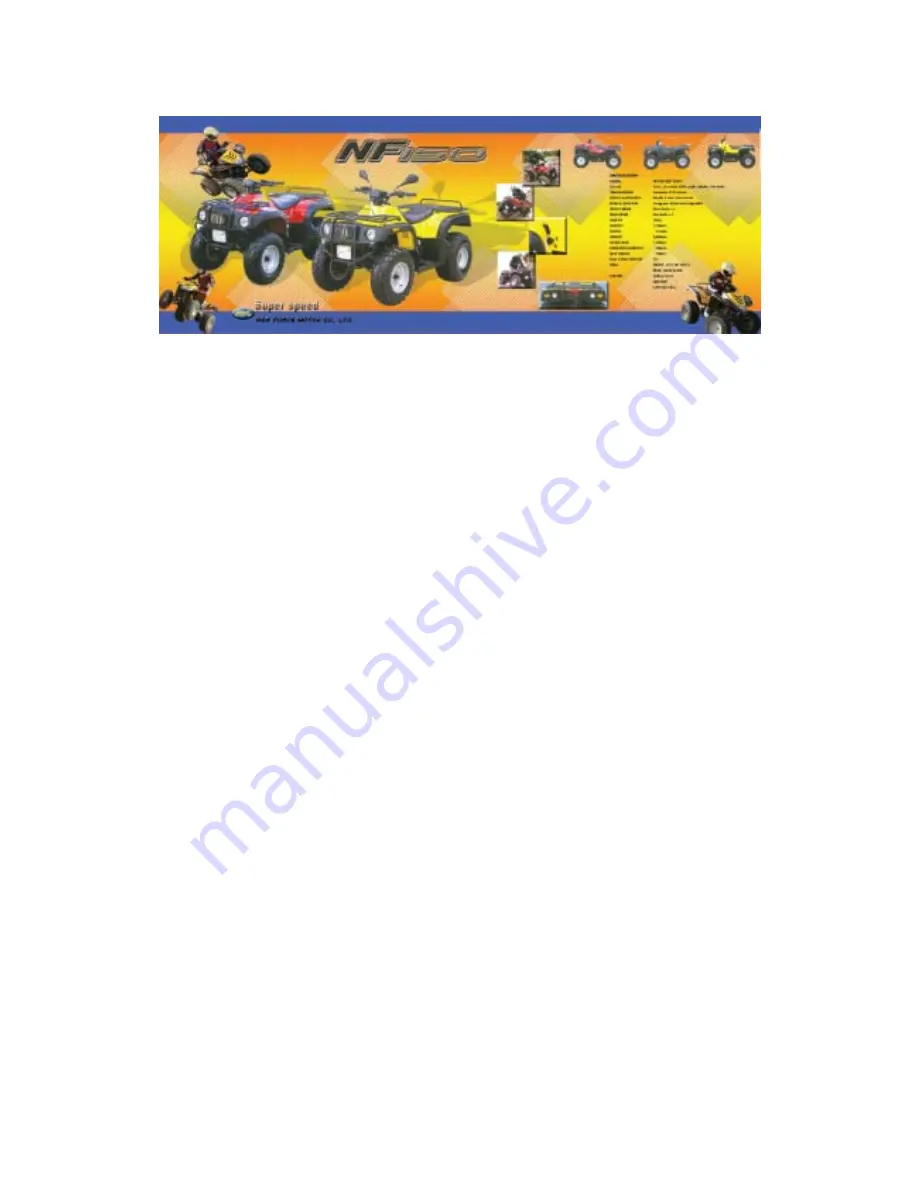
NF150- 150cc Utility Repair Manual
CONTENTS
1. INFORMTION 2
2. MAINTENANCE 6
3. ENGINE REMOVAL AND INSTALLATION 12
4. ENGINE FUEL SYSTEM 13
5. ENGINE LUBRICATION AND COOLING SYSTEM 15
6.
ENGINE
COMBUSTION
SYSTEM
16
7. TRANSMISSION SYSTEM
25
8.
FRONT
WHEEL
AND
STEERING
SYSTEM
30
9. REAR WHEEL SYSTEM
38
10.
BODY
COVER
AND
EXHAUST
PIPE
41
11.
ELECTRICAL
SYSTEM
43
12.
TROUBLE
SHOOTING
47
Summary of Contents for NF150
Page 49: ...49 11 8 WIRING DIAGRAMS ...