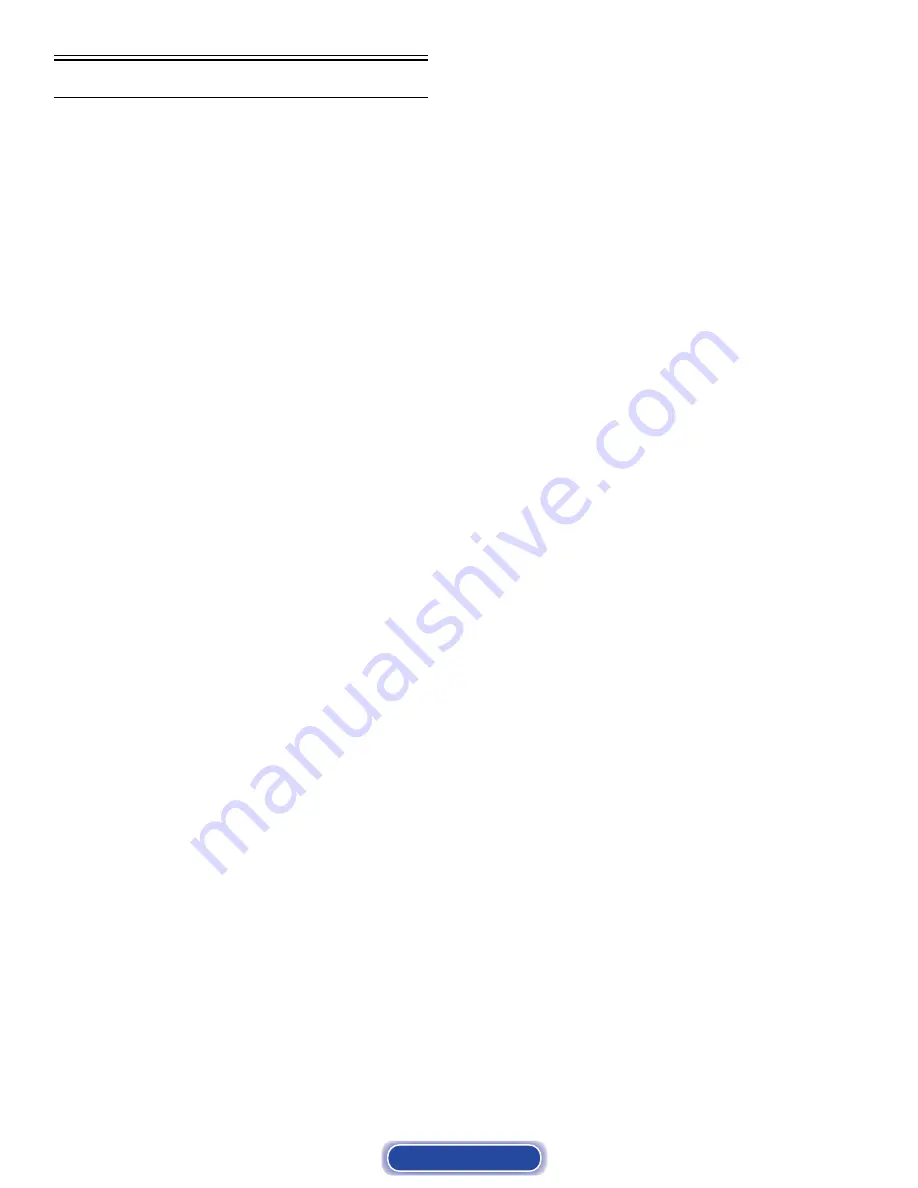
FOREWORD
This Arctic Cat Service Manual contains service, maintenance, and troubleshooting information for the 2008 Arctic
Cat UTV models. The complete manual is designed to aid service personnel in service-oriented applications.
This manual is divided into sections. Each section covers a specific vehicle component or system and, in addition to the
standard service procedures, includes disassembling, inspecting, and assembling instructions. When using this manual
as a guide, the technician should use discretion as to how much disassembly is needed to correct any given condition.
The service technician should become familiar with the operation and construction of each component or system by
carefully studying this manual. This manual will assist the service technician in becoming more aware of and efficient
with servicing procedures. Such efficiency not only helps build consumer confidence but also saves time and labor.
All Arctic Cat publications and decals display the words Warning, Caution, Note, and At This Point to emphasize
important information. The symbol
! WARNING
identifies personal safety-related information. Be sure to fol-
low the directive because it deals with the possibility of severe personal injury or even death. The symbol
! CAUTION
identifies unsafe practices which may result in vehicle-related damage. Follow the directive because
it deals with the possibility of damaging part or parts of the vehicle. The symbol
NOTE:
identifies supplementary
information worthy of particular attention. The symbol
AT THIS POINT
directs the technician to certain and
specific procedures to promote efficiency and to improve clarity.
At the time of publication, all information, photographs, and illustrations were technically correct. Some photographs
used in this manual are used for clarity purposes only and are not designed to depict actual conditions. Because Arctic
Cat Inc. constantly refines and improves its products, no retroactive obligation is incurred.
All materials and specifications are subject to change without notice.
Keep this manual accessible in the shop area for reference.
Product Service and
Warranty Department
Arctic Cat Inc.
© 2008 Arctic Cat Inc.
March 2008
®™ Trademarks of Arctic Cat Inc., Thief River Falls, MN 56701
Back to TOC